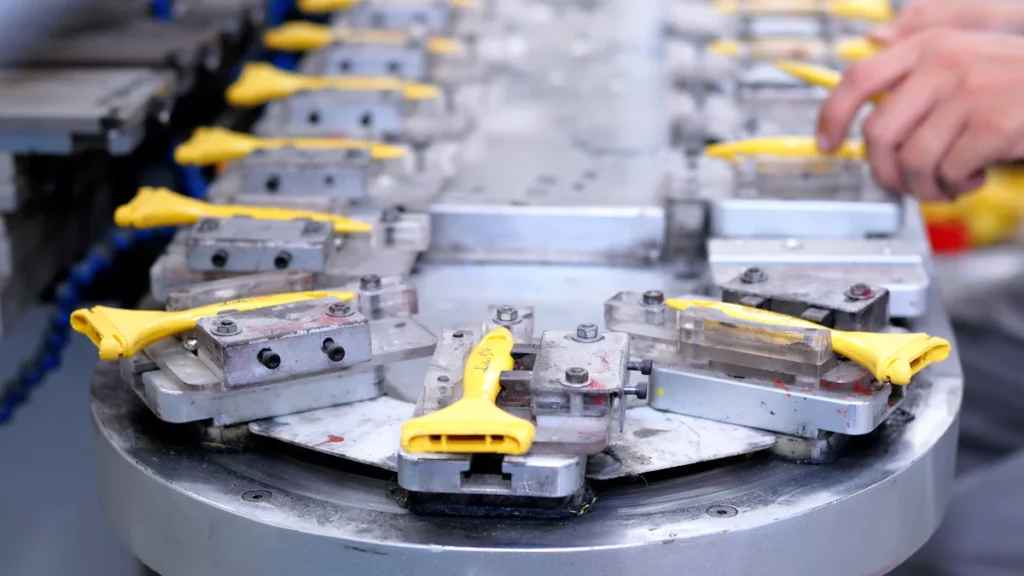
छवि स्रोत: pexels
डाई कास्टिंग में, सामग्री चयन सफलता की आधारशिला है, सीधे आपके अंतिम उत्पाद की गुणवत्ता और स्थायित्व को प्रभावित करना.
यह ब्लॉग डाई कास्टिंग सामग्री के विविध परिदृश्य को नेविगेट करने के लिए आपके वन-स्टॉप गाइड के रूप में कार्य करता है. हम उनके अद्वितीय गुणों का पता लगाएंगे, आदर्श अनुप्रयोग, और अपनी पसंद बनाते समय विचार करने वाले कारक.
इसलिए, बकसुआ और मरने वाली कास्टिंग उद्योग को शक्ति देने वाली सामग्रियों के पीछे रहस्यों को अनलॉक करने के लिए तैयार हो जाओ!
आम डाई कास्टिंग सामग्री
आइए जिंक मिश्र धातुओं के अद्वितीय गुणों और अनुप्रयोगों का पता लगाएं, मैग्नीशियम मिश्र धातु, और एल्यूमीनियम मिश्र धातु.
जस्ता मिश्र धातु
- व्यापक रूप से छोटे डाई कास्टिंग या पतले वर्गों की आवश्यकता वाले लोगों के लिए उपयोग किया जाता है.
- अनुभाग मोटाई में महत्वपूर्ण भिन्नता की अनुमति देने वाली बेहतर कास्टेबिलिटी.
- अन्य सामान्य धातु मिश्र धातुओं की तुलना में करीब सहिष्णुता बनाए रखता है.
मैग्नीशियम मिश्र धातु
- उनके उच्च शक्ति-से-वजन अनुपात के लिए जाना जाता है, जैसे az91d, AM60B, और AS41B.
- जंग और पहनने के लिए अच्छा प्रतिरोध प्रदान करता है, उन्हें विशिष्ट अनुप्रयोगों के लिए आदर्श बनाना.
एल्यूमीनियम मिश्र धातु
- बहुमुखी गुणों के साथ प्राथमिक और अत्यधिक किफायती डाई-कास्टिंग सामग्री.
- एयरोस्पेस के लिए उपयुक्त उल्लेखनीय शक्ति-से-वजन अनुपात, ऑटोमोटिव, और उपभोक्ता सामान अनुप्रयोग.
तांबे के मिश्र धातु
कॉपर मिश्र उत्कृष्ट थर्मल और विद्युत चालकता प्रदान करते हैं, के लिए उन्हें आदर्श बना रहा है विशिष्ट अनुप्रयोग. इन मिश्र धातुओं को उनके संक्षारण प्रतिरोध और स्थायित्व के लिए जाना जाता है, विभिन्न वातावरणों में दीर्घायु सुनिश्चित करना.
सामान्य अनुप्रयोगों में विद्युत घटक शामिल हैं, नलसाजी स्थावर द्रव्य, और उच्च तापमान के तहत उनके असाधारण प्रदर्शन के कारण हीट एक्सचेंजर्स. इसके अतिरिक्त, ये मिश्र धातु अच्छी मशीनबिलिटी प्रदान करते हैं, जटिल डिजाइनों और सटीक खत्म के लिए अनुमति.
सीसा और टिन मिश्र धातु
लीड और टिन मिश्र कम पिघलने वाले बिंदुओं की पेशकश करते हैं, जटिल डिजाइनों के लिए आसान कास्टिंग प्रक्रियाओं की सुविधा. इन मिश्र धातुओं का उपयोग आमतौर पर बीयरिंग के उत्पादन में किया जाता है, टांका लगाने की सामग्री, और उनके घनत्व और मॉलबिलिटी के कारण विकिरण परिरक्षण.
उनके स्व-चिकनाई गुण उन्हें उन अनुप्रयोगों के लिए उपयुक्त बनाते हैं जहां घर्षण में कमी महत्वपूर्ण है. लीड के उपयोग के आसपास पर्यावरणीय चिंताओं के बावजूद, इन मिश्र धातुओं को उनकी अनूठी विशेषताओं के लिए महत्व दिया जाता है.
डाई कास्टिंग सामग्री के गुण
ताकत
तांबे के मिश्र धातु, उदाहरण के लिए, उच्च शक्ति और कठोरता का प्रदर्शन, उन्हें विभिन्न अनुप्रयोगों के लिए आदर्श बनाना जिनके लिए मजबूत घटकों की आवश्यकता होती है. ये मिश्र असाधारण आयामी स्थिरता प्रदान करते हैं, यह सुनिश्चित करना कि डाई-कास्ट भागों को चुनौतीपूर्ण परिस्थितियों में भी अपनी संरचनात्मक अखंडता बनाए रखें.
इसके विपरीत, सीसा और टिन मिश्र धातु उनके उच्च घनत्व के लिए जाने जाते हैं, जो उनकी उल्लेखनीय ताकत में योगदान देता है. यह विशेषता इन मिश्र धातुओं को बेहद करीबी आयामी सटीकता प्रदान करने में सक्षम बनाती है, उन अनुप्रयोगों के लिए आवश्यक जहां सटीकता सर्वोपरि है. उनके घनत्व के बावजूद, लीड और टिन मिश्र जंग के अद्वितीय रूपों की पेशकश करते हैं, उन्हें विशेष मरने वाली कास्टिंग आवश्यकताओं के लिए उपयुक्त बनाना.
सहनशीलता
तांबे के मिश्र धातु उनके उत्कृष्ट संक्षारण प्रतिरोध के लिए प्रसिद्ध हैं, कठोर वातावरण में दीर्घायु और विश्वसनीयता सुनिश्चित करना. ये मिश्र धातु प्रदर्शन या संरचनात्मक अखंडता से समझौता किए बिना समय की कसौटी का सामना कर सकते हैं.
उसी प्रकार, सीसा और टिन मिश्र धातु के रूप में उनके प्रतिरोध के कारण प्रभावशाली स्थायित्व का दावा करते हैं. समय के साथ आयामी सटीकता बनाए रखने की उनकी क्षमता उन्हें उन अनुप्रयोगों के लिए मूल्यवान विकल्प बनाती है जहां दीर्घकालिक प्रदर्शन आवश्यक है.
मशीन की
कॉपर-आधारित मिश्र जैसे कि पीतल और कांस्य अच्छे मशीनबिलिटी गुण प्रदान करते हैं, डाई-कास्ट भागों के कुशल आकार और परिष्करण के लिए अनुमति. इन मिश्र धातुओं की मशीनबिलिटी गुणवत्ता पर समझौता किए बिना तेजी से उत्पादन चक्रों को सक्षम करके उत्पादकता को बढ़ाती है.
लीड और टिन मिश्र भी अनुकूल मशीनबिलिटी विशेषताओं का प्रदर्शन करते हैं, उन्हें उन अनुप्रयोगों के लिए उपयुक्त बनाना जिनके लिए जटिल विवरण या जटिल ज्यामिति की आवश्यकता होती है. निर्माता कम से कम पोस्ट-प्रोसेसिंग आवश्यकताओं के साथ सटीक परिणाम प्राप्त करने के लिए इन मिश्र धातुओं की मशीनीकरण पर भरोसा कर सकते हैं.
डाई कास्टिंग में जिंक

छवि स्रोत: unsplash
जस्ता के गुण
ताकत और स्थायित्व
जस्ता मिश्र असाधारण प्रदान करता है ताकत और टिकाऊपन अन्य डाई कास्टिंग सामग्री की तुलना में. जिंक द्वारा प्रदान की जाने वाली उच्च परिशुद्धता और लंबे समय तक उपकरण इसे विभिन्न अनुप्रयोगों के लिए एक पसंदीदा विकल्प बनाते हैं. चुनौतीपूर्ण परिस्थितियों का सामना करने की इसकी क्षमता डाई-कास्ट भागों की दीर्घायु सुनिश्चित करती है, इसे विनिर्माण प्रक्रियाओं के लिए एक आदर्श सामग्री बनाना.
डाई कास्टिंग में जस्ता का उपयोग
लघु भाग
जस्ता का उपयोग आमतौर पर उत्पादन में किया जाता है लघु भाग इसकी उत्कृष्ट कास्टेबिलिटी और आयामी स्थिरता के कारण. जस्ता मिश्र धातुओं की बहुमुखी प्रतिभा सटीक विवरण के साथ जटिल डिजाइनों के निर्माण के लिए अनुमति देती है, यह विभिन्न उद्योगों में छोटे घटकों के लिए एक विश्वसनीय विकल्प है.
उपभोक्ता इलेक्ट्रॉनिक्स
के दायरे में उपभोक्ता इलेक्ट्रॉनिक्स, जस्ता हल्के अभी तक टिकाऊ भागों के उत्पादन में एक महत्वपूर्ण भूमिका निभाता है. जिंक का संक्षारण प्रतिरोध और सौंदर्य अपील यह इलेक्ट्रॉनिक उपकरणों के लिए उपयुक्त है जो कार्यक्षमता और दृश्य अपील दोनों की आवश्यकता है. स्मार्टफोन घटकों से लेकर घरेलू गैजेट तक, जिंक एक बहुमुखी सामग्री है जो उपभोक्ता इलेक्ट्रॉनिक्स के प्रदर्शन और सौंदर्यशास्त्र को बढ़ाती है.
लाभ और सीमाएँ
- लाभ: जिंक डाई कास्टिंग को पतला बनाया जा सकता है, अधिक जटिल, और एल्यूमीनियम और मैग्नीशियम की तुलना में अधिक जटिल. इससे हल्के भागों में परिणाम होता है, भौतिक लागत और ऊर्जा की खपत में बचत के लिए अग्रणी.
- सीमाएँ: जबकि जस्ता उच्च परिशुद्धता और स्थायित्व प्रदान करता है, यह अत्यधिक ताकत या उच्च परिचालन तापमान की आवश्यकता वाले अनुप्रयोगों के लिए उपयुक्त नहीं हो सकता है.
डाई कास्टिंग में एल्यूमीनियम
एल्युमीनियम के गुण
बहुमुखी प्रतिभा
अल्युमीनियम, इसके लिए जाना जाता है हल्के गुण, डाई कास्टिंग अनुप्रयोगों में असाधारण बहुमुखी प्रतिभा प्रदान करता है. विभिन्न आकारों और आकारों में आसानी से ढाला जाने की इसकी क्षमता डिजाइन में लचीलेपन की मांग करने वाले निर्माताओं के लिए एक पसंदीदा विकल्प बनाती है.
एल्यूमीनियम की बहुमुखी प्रतिभा विभिन्न परिष्करण तकनीकों के साथ इसकी संगतता तक फैली हुई है, विशिष्ट आवश्यकताओं को पूरा करने के लिए अनुकूलित सतह उपचार के लिए अनुमति.
उच्च संचालन तापमान
डाई कास्टिंग में एल्यूमीनियम के प्रमुख लाभों में से एक संरचनात्मक अखंडता से समझौता किए बिना उच्च परिचालन तापमान का सामना करने की इसकी क्षमता है. यह संपत्ति उन अनुप्रयोगों के लिए एल्यूमीनियम आदर्श बनाती है जहां घटक ऊंचे गर्मी के स्तर के संपर्क में हैं, जैसे कि ऑटोमोटिव इंजन या एयरोस्पेस सिस्टम.
डाई कास्टिंग में एल्यूमीनियम का उपयोग
स्वचालित भाग
ऑटोमोटिव उद्योग बड़े पैमाने पर अपने हल्के प्रकृति और ताकत के कारण विभिन्न घटकों के लिए एल्यूमीनियम डाई कास्टिंग का उपयोग करता है. इंजन ब्लॉक से लेकर ट्रांसमिशन हाउसिंग तक, एल्यूमीनियम भागों में सुधार ईंधन दक्षता और समग्र वाहन प्रदर्शन में योगदान है. एल्यूमीनियम का संक्षारण प्रतिरोध आगे मोटर वाहन भागों के स्थायित्व को बढ़ाता है, सड़क पर दीर्घायु और विश्वसनीयता सुनिश्चित करना.
वायु -घटक
एयरोस्पेस सेक्टर में, एल्यूमीनियम विमान और अंतरिक्ष यान के लिए हल्के अभी तक मजबूत घटकों के उत्पादन में एक महत्वपूर्ण भूमिका निभाता है. एल्यूमीनियम मिश्र धातुओं का उच्च शक्ति-से-वजन अनुपात उन्हें एयरोस्पेस अनुप्रयोगों के लिए अच्छी तरह से अनुकूल बनाता है जहां संरचनात्मक अखंडता से समझौता किए बिना वजन कम करना आवश्यक है. धड़ भागों से लेकर आंतरिक घटकों तक, एल्यूमीनियम डाई कास्टिंग उड़ान प्रदर्शन और ईंधन दक्षता को बढ़ाने में योगदान करते हैं.
लाभ और सीमाएँ
- लाभ: डाई कास्टिंग में एल्यूमीनियम का उपयोग करने का प्राथमिक लाभ इसकी असाधारण शक्ति-से-वजन अनुपात है, इसे हल्के अभी तक टिकाऊ घटकों की आवश्यकता वाले अनुप्रयोगों के लिए एक आदर्श विकल्प बनाना. इसके अतिरिक्त, एल्यूमीनियम का संक्षारण प्रतिरोध और थर्मल चालकता विभिन्न उद्योगों में मूल्य जोड़ें.
- सीमाएँ: इसके कई लाभों के बावजूद, एल्यूमीनियम में सीमाएं होती हैं जब यह कुछ अनुप्रयोगों की बात आती है जो उच्च तन्यता ताकत की मांग करते हैं या इसके ऑपरेटिंग तापमान रेंज से परे चरम स्थितियों के लिए प्रतिरोध की मांग करते हैं. विशिष्ट डाई कास्टिंग परियोजनाओं के लिए सामग्री का चयन करते समय निर्माताओं को इन सीमाओं पर सावधानीपूर्वक विचार करना चाहिए.
अल्युमीनियम मग डाई कास्टिंग में उपयोग करता है
एडीसी12
यह बहुमुखी एल्यूमीनियम मिश्र धातु अपने उत्कृष्ट के लिए एक लोकप्रिय विकल्प है कास्टेबिलिटी, मतलब यह आसानी से नए साँचे में बहता है, और अच्छा मशीन की, सटीक परिष्करण स्पर्श के लिए अनुमति. यह विभिन्न अनुप्रयोगों के लिए एक अच्छी तरह से गोल विकल्प है.
एडीसी10
ADC10 के बीच एक संतुलन है कास्टेबिलिटी और यांत्रिक शक्ति. यह एक अच्छा विकल्प है जब आपको एक ऐसी सामग्री की आवश्यकता होती है जो कास्टिंग प्रक्रिया के दौरान काम करने में आसान होने के दौरान कुछ दबाव को संभाल सके.
ए360
A360 इसके असाधारण के साथ चमकता है संक्षारण प्रतिरोध. यह कठोर बाहरी वातावरण के संपर्क में आने वाले उत्पादों के लिए एक आदर्श विकल्प बनाता है, निर्माण सामग्री या समुद्री घटकों की तरह.
ए 380
यह एल्यूमीनियम मिश्र धातु प्राथमिकता देता है दबाव की जकड़न. यह उन अनुप्रयोगों में उत्कृष्टता प्राप्त करता है जहां घटकों को तरल या गैसों को सुरक्षित रूप से रखने की आवश्यकता होती है, जैसे इंजन ब्लॉक या दबाव वाहिकाओं.
डाई कास्टिंग में मैग्नीशियम
मैग्नीशियम के गुण
हल्के वजन
मैग्नीशियम अपने असाधारण हल्के गुणों के लिए डाई कास्टिंग में खड़ा है, यह उन अनुप्रयोगों के लिए एक पसंदीदा विकल्प बनाना जहां वजन में कमी महत्वपूर्ण है. मैग्नीशियम मिश्र धातुओं का कम घनत्व ताकत या स्थायित्व पर समझौता किए बिना हल्के घटकों के उत्पादन में योगदान देता है. यह विशेषता मोटर वाहन और एयरोस्पेस जैसे उद्योगों में विशेष रूप से लाभप्रद है, जहां ईंधन दक्षता और प्रदर्शन सर्वोपरि हैं.
बेरहमी
इसके हल्के स्वभाव के अलावा, मैग्नीशियम मिश्र भी उनकी प्रभावशाली क्रूरता के लिए मूल्यवान हैं. मैग्नीशियम की अंतर्निहित शक्ति उन अनुप्रयोगों के लिए उपयुक्त बनाती है जिनके लिए मजबूत और प्रभाव प्रतिरोधी भागों की आवश्यकता होती है. चाहे मोटर वाहन संरचनात्मक घटकों या उपभोक्ता इलेक्ट्रॉनिक्स बाड़ों में उपयोग किया जाता है, मैग्नीशियम की क्रूरता डाई-कास्ट उत्पादों की दीर्घायु और विश्वसनीयता सुनिश्चित करती है.
डाई कास्टिंग में मैग्नीशियम का उपयोग
मोटर वाहन उद्योग
मोटर वाहन उद्योग बड़े पैमाने पर अपने हल्के अभी तक टिकाऊ विशेषताओं के कारण विभिन्न घटकों के लिए मैग्नीशियम मिश्र धातुओं का उपयोग करता है. इंजन भागों से लेकर ट्रांसमिशन हाउसिंग तक, मैग्नीशियम ईंधन दक्षता और समग्र वाहन प्रदर्शन को बढ़ाने में महत्वपूर्ण भूमिका निभाता है. मैग्नीशियम का संक्षारण प्रतिरोध आगे मोटर वाहन घटकों की दीर्घायु और विश्वसनीयता में योगदान देता है.
उपभोक्ता इलेक्ट्रॉनिक्स
उपभोक्ता इलेक्ट्रॉनिक्स के दायरे में, मैग्नीशियम मिश्र चिकना और हल्के उपकरणों के उत्पादन में अनुप्रयोगों का पता लगाते हैं. हल्के गुणों और संरचनात्मक अखंडता का संयोजन मैग्नीशियम को स्मार्टफोन के लिए एक आदर्श विकल्प बनाता है, लैपटॉप, और अन्य इलेक्ट्रॉनिक गैजेट्स. निर्माता अभिनव डिजाइन बनाने में मैग्नीशियम की बहुमुखी प्रतिभा से लाभान्वित होते हैं जो सौंदर्यशास्त्र और कार्यक्षमता दोनों को प्राथमिकता देते हैं.
लाभ और सीमाएँ
- लाभ: मैग्नीशियम हल्के का एक अनूठा संयोजन प्रदान करता है, ताकत, और क्रूरता, यह विभिन्न उद्योगों के लिए एक बहुमुखी सामग्री बना रहा है. इसकी उत्कृष्ट मशीनबिलिटी सटीक विवरण के साथ जटिल डिजाइनों के लिए अनुमति देती है, विविध विनिर्माण आवश्यकताओं के लिए खानपान.
- सीमाएँ: इसके कई फायदों के बावजूद, मैग्नीशियम कुछ वातावरणों में जंग प्रतिरोध के संदर्भ में चुनौतियों का सामना कर सकता है. इसके अतिरिक्त, मैग्नीशियम की उच्च प्रतिक्रियाशीलता को इष्टतम परिणाम सुनिश्चित करने के लिए डाई कास्टिंग प्रक्रिया के दौरान सावधानीपूर्वक हैंडलिंग की आवश्यकता होती है.
डाई कास्टिंग में कॉपर मिश्र धातु
गुण और विशेषताएँ
- उच्च चालकता: तांबे के मिश्र धातु उनके असाधारण विद्युत और थर्मल चालकता के लिए प्रसिद्ध हैं, उन्हें उन अनुप्रयोगों के लिए आदर्श बनाना जिनके लिए कुशल गर्मी हस्तांतरण और विद्युत चालन की आवश्यकता होती है.
- संक्षारण प्रतिरोध: के निहित गुण तांबे के मिश्र धातु जंग के लिए उत्कृष्ट प्रतिरोध प्रदान करें, विभिन्न वातावरणों में दीर्घायु और स्थायित्व सुनिश्चित करना.
- सहनशीलता: संरचनात्मक अखंडता पर ध्यान देने के साथ, तांबे के मिश्र धातु उच्च स्थायित्व प्रदान करें, उन्हें उन अनुप्रयोगों के लिए उपयुक्त बनाना जहां मजबूत घटक आवश्यक हैं.
सामान्य अनुप्रयोग
- विद्युत घटक: तांबे के मिश्र धातु उनकी बेहतर चालकता के कारण वायरिंग और कनेक्टर्स जैसे विद्युत घटकों के उत्पादन में व्यापक उपयोग का पता लगाएं.
- नलसाजी स्थावर द्रव्य: का संक्षारण प्रतिरोध तांबे के मिश्र धातु उन्हें प्लंबिंग जुड़नार के लिए एक पसंदीदा विकल्प बनाता है, विश्वसनीयता और दीर्घायु सुनिश्चित करना.
- हीट एक्सचेंजर्स: उनकी उत्कृष्ट तापीय चालकता के कारण, तांबे के मिश्र धातु आमतौर पर कुशल गर्मी हस्तांतरण के लिए हीट एक्सचेंजर्स में नियोजित होते हैं.
लाभ और सीमाएँ
- लाभ:
- तांबे के मिश्र धातु असाधारण थर्मल और विद्युत चालकता प्रदान करें, गर्मी हस्तांतरण और विद्युत अनुप्रयोगों में दक्षता प्रदान करना.
- का संक्षारण प्रतिरोध तांबे के मिश्र धातु विभिन्न वातावरणों में दीर्घायु और विश्वसनीयता सुनिश्चित करता है.
- ये मिश्र धातु अच्छी मशीनबिलिटी प्रदर्शित करते हैं, सटीक फिनिश के साथ जटिल डिजाइनों के लिए अनुमति.
- सीमाएँ:
- जबकि तांबे के मिश्र धातु कई फायदे प्रदान करें, वे अपनी सीमा से परे अत्यधिक शक्ति या उच्च परिचालन तापमान की आवश्यकता वाले अनुप्रयोगों के लिए उपयुक्त नहीं हो सकते हैं.
सीसा और टिन मिश्र धातु विस्तार से
गुण और विशेषताएँ
- सीसा और टिन मिश्र धातु उनके कम पिघलने वाले बिंदुओं के लिए प्रसिद्ध हैं, उन्हें जटिल डिजाइन और विस्तृत कास्टिंग के लिए आदर्श बनाना.
- ये मिश्र धातुएं कास्टिंग प्रक्रिया के दौरान उत्कृष्ट तरलता प्रदर्शित करती हैं, जटिल सुविधाओं के साथ मोल्ड की सटीक प्रतिकृति सुनिश्चित करना.
- की मॉलबिलिटी सीसा और टिन मिश्र धातु आसान आकार और अनुकूलन के लिए अनुमति देता है, डिजाइन आवश्यकताओं की एक विस्तृत श्रृंखला के लिए खानपान.
सामान्य अनुप्रयोग
- बीयरिंग: सीसा और टिन मिश्र धातु आमतौर पर उनके आत्म-चिकनाई गुणों के कारण उत्पादन में उपयोग किया जाता है, घर्षण को कम करना और पहनना.
- टांका लगाने की सामग्री: इन मिश्र धातुओं के कम पिघलने वाले बिंदु उन्हें इलेक्ट्रॉनिक्स और नलसाजी में टांका लगाने के लिए उपयुक्त बनाते हैं.
- विकिरण परिरक्षण: उनके घनत्व के कारण, सीसा और टिन मिश्र धातु विकिरण परिरक्षण अनुप्रयोगों में प्रभावी हैं जहां सुरक्षा सर्वोपरि है.
लाभ और सीमाएँ
- लाभ:
- कास्टिंग में आसानी: इन मिश्र धातुओं के कम पिघलने वाले बिंदु जटिल डिजाइनों के लिए आसान कास्टिंग प्रक्रियाओं की सुविधा प्रदान करते हैं.
- स्व स्नेहन: उनके आत्म-चिकनाई गुण उन्हें कम घर्षण की आवश्यकता वाले अनुप्रयोगों के लिए आदर्श बनाते हैं.
- बढ़ने की योग्यता: लीड और टिन मिश्र धातुओं की निंदनीय प्रकृति डाई कास्टिंग में बहुमुखी आकार देने वाले विकल्पों के लिए अनुमति देती है.
- सीमाएँ:
- पर्यावरणीय चिंता: पर्यावरणीय नियम अपने संभावित खतरों के कारण सीसा के उपयोग को प्रतिबंधित करते हैं.
- सीमित शक्ति: ये मिश्र चरम परिस्थितियों में उच्च तन्यता शक्ति या स्थायित्व की आवश्यकता वाले अनुप्रयोगों के लिए उपयुक्त नहीं हो सकते हैं.
डाई कास्टिंग में उभरती हुई सामग्री
नए मिश्र धातु विकास
- डाई कास्टिंग सामग्री में नवाचार विनिर्माण प्रक्रियाओं में प्रगति को आगे बढ़ाते हैं. निर्माता खोज रहे हैं नए मिश्र धातु विकास डाई-कास्ट घटकों के प्रदर्शन और दक्षता को बढ़ाने के लिए. ये मिश्र विशिष्ट अनुप्रयोगों के लिए इष्टतम गुण सुनिश्चित करने के लिए कठोर परीक्षण से गुजरते हैं, बेहतर शक्ति की पेशकश, टिकाऊपन, और संक्षारण प्रतिरोध.
- समग्र सामग्रियों की शुरूआत ने अद्वितीय विशेषताओं के साथ हाइब्रिड मिश्र धातुओं को बनाने के लिए कई तत्वों को मिलाकर डाई कास्टिंग उद्योग में क्रांति ला दी है. समग्र सामग्री हल्के डिजाइन जैसे गुणों का संतुलन प्रदान करती है, बढ़ाया यांत्रिक शक्ति, और तापीय चालकता में वृद्धि हुई. यह अभिनव दृष्टिकोण उद्योगों में विविध अनुप्रयोगों के लिए दरवाजे खोलता है, मोटर वाहन इंजीनियरिंग से लेकर इलेक्ट्रॉनिक उपकरणों तक. समग्र सामग्री का लाभ उठाकर, निर्माता डाई कास्टिंग प्रौद्योगिकियों में बेहतर उत्पाद की गुणवत्ता और नवाचार प्राप्त कर सकते हैं.
सामग्री चयन प्रक्रिया
सही सामग्री चुनने के लिए कदम
- अपनी परियोजना की विशिष्ट आवश्यकताओं की पहचान करें, ताकत जैसे कारकों को ध्यान में रखते हुए, टिकाऊपन, और चालकता. वांछित विशेषताओं को समझना आपको सबसे उपयुक्त डाई कास्टिंग सामग्री का चयन करने में मार्गदर्शन करेगा.
- डाई कास्टिंग के लिए उपलब्ध विभिन्न सामग्रियों के गुणों का मूल्यांकन करें, उनकी अनूठी ताकत और सीमाओं पर ध्यान केंद्रित करना. जंग प्रतिरोध जैसे कारकों की तुलना करें, मशीन की, और आपके आवेदन के लिए इष्टतम विकल्प निर्धारित करने के लिए थर्मल चालकता.
- उन पर्यावरणीय परिस्थितियों पर विचार करें जिनमें अंतिम उत्पाद संचालित होगा. सुनिश्चित करें कि चयनित सामग्री तापमान भिन्नता का सामना कर सकती है, रसायनों के संपर्क में, और प्रदर्शन से समझौता किए बिना अन्य बाहरी कारक.
- अपने डिजाइन विनिर्देशों के साथ चुनी गई सामग्री की संगतता को मान्य करने के लिए प्रोटोटाइप और परीक्षण का संचालन करें. प्रोटोटाइप आपको यह आकलन करने की अनुमति देता है कि सामग्री पूर्ण-पैमाने पर उत्पादन से पहले संरचनात्मक आवश्यकताओं और कार्यात्मक अपेक्षाओं को कितनी अच्छी तरह पूरा करती है.
प्रोटोटाइप और परीक्षण का महत्व
- प्रोटोटाइप मूल्यांकन के लिए एक मूर्त मॉडल प्रदान करके अपने डिजाइन और सामग्री चयन प्रक्रिया को परिष्कृत करने में एक महत्वपूर्ण भूमिका निभाता है. यह आपको किसी भी संभावित मुद्दों की पहचान करने और प्रदर्शन को अनुकूलित करने के लिए आवश्यक समायोजन करने की अनुमति देता है.
- परीक्षण वास्तविक दुनिया की शर्तों के तहत डाई-कास्ट घटकों की कार्यक्षमता और स्थायित्व को मान्य करता है. कठोर परीक्षणों के लिए प्रोटोटाइप के अधीन, आप यह सुनिश्चित कर सकते हैं कि चुनी गई सामग्री गुणवत्ता मानकों और नियामक आवश्यकताओं को पूरा करती है.
- पुनरावृत्ति प्रोटोटाइप परीक्षण के परिणामों के आधार पर निरंतर सुधार को सक्षम करता है, बढ़ी हुई उत्पाद प्रदर्शन और विश्वसनीयता के लिए अग्रणी. एक पुनरावृत्ति दृष्टिकोण के माध्यम से, आप डाई कास्टिंग प्रक्रियाओं में अधिकतम दक्षता के लिए सामग्री चयन को ठीक कर सकते हैं.
एक व्यवस्थित दृष्टिकोण का पालन करके जिसमें गहन मूल्यांकन शामिल है, प्रोटोटाइप, और परीक्षण, आप अपने अंतिम उत्पादों में इष्टतम प्रदर्शन और गुणवत्ता सुनिश्चित करते हुए डाई कास्टिंग परियोजनाओं के लिए सामग्री चयन प्रक्रिया को सुव्यवस्थित कर सकते हैं.
डाई कास्टिंग प्रक्रिया पर सामग्री की पसंद का प्रभाव
मशीन चयन पर प्रभाव
- डाई कास्टिंग परियोजनाओं में सही सामग्री के लिए चयन करने से टूलींग लागतों को काफी प्रभावित किया जा सकता है, repeatability, और भाग स्थायित्व.
- एल्यूमीनियम डाई कास्टिंग मिश्र धातु उत्कृष्ट संक्षारण प्रतिरोध प्रदान करते हैं, तापमान लचीलापन, और थर्मल और विद्युत चालकता. ये गुण एल्यूमीनियम मिश्र धातुओं को जटिल और ठीक-ठाक भागों के लिए एक उपयुक्त विकल्प बनाते हैं.
- डाई कास्टिंग के लिए चुनी गई सामग्री को उच्च तापमान का सामना करना होगा, दबाव, और अंत-उपयोग अनुप्रयोगों की मांगें.
डाई डिजाइन पर प्रभाव
- सामग्री की पसंद कास्टिंग प्रक्रिया में उपयोग किए गए मरने के डिजाइन को निर्धारित करने में एक महत्वपूर्ण भूमिका निभाती है.
- विभिन्न सामग्रियों में अलग -अलग विशेषताएं होती हैं जो प्रभावित करती हैं कि वे कितनी अच्छी तरह से सांचों को भरते हैं और शीतलन के दौरान संरचनात्मक अखंडता बनाए रखते हैं.
- विशिष्ट गुणों के साथ सामग्री का चयन करना सुनिश्चित करता है कि डाई डिज़ाइन अंतिम उत्पाद के वांछित परिणामों के साथ संरेखित करता है.
पोस्ट-प्रोसेसिंग के लिए निहितार्थ
- डाई कास्टिंग के लिए चुनी गई सामग्री में पोस्ट-प्रोसेसिंग प्रक्रियाओं जैसे परिष्करण के लिए निहितार्थ हैं, मशीनिंग, या सतह उपचार.
- अच्छी मशीनबिलिटी वाली सामग्री को वांछित सतह खत्म करने के लिए कम पोस्ट-प्रोसेसिंग की आवश्यकता हो सकती है.
- शुरू में सामग्री के गुणों को ध्यान में रखते हुए प्रसंस्करण के बाद के प्रयासों को सुव्यवस्थित कर सकते हैं और उत्पादन में समग्र दक्षता बढ़ा सकते हैं.
डाई कास्टिंग सामग्री के अनुप्रयोग
मोटर वाहन उद्योग
एल्यूमीनियम मिश्र धातुओं का उपयोग मोटर वाहन उद्योग में उनके हल्के गुणों और असाधारण शक्ति-से-वजन अनुपात के लिए किया जाता है. एल्यूमीनियम मिश्र धातुओं का संक्षारण प्रतिरोध उन्हें विभिन्न मोटर वाहन घटकों के लिए आदर्श बनाता है, इंजन भागों और ट्रांसमिशन हाउसिंग सहित. एल्यूमीनियम डाई कास्टिंग को शामिल करके, निर्माता ईंधन दक्षता और समग्र वाहन प्रदर्शन को बढ़ा सकते हैं. एल्यूमीनियम मिश्र धातुओं का स्थायित्व और दीर्घायु सड़क पर विश्वसनीय प्रदर्शन सुनिश्चित करता है, मोटर वाहन इंजीनियरिंग परियोजनाओं की सफलता में योगदान.
उपभोक्ता इलेक्ट्रॉनिक्स
उपभोक्ता इलेक्ट्रॉनिक्स के दायरे में, मैग्नीशियम मिश्र चिकना और हल्के उपकरणों के उत्पादन में महत्वपूर्ण भूमिका निभाते हैं. मैग्नीशियम के हल्के गुणों और संरचनात्मक अखंडता का संयोजन इसे स्मार्टफोन के लिए एक आदर्श विकल्प बनाता है, लैपटॉप, और अन्य इलेक्ट्रॉनिक गैजेट्स. निर्माता अभिनव डिजाइन बनाने में मैग्नीशियम की बहुमुखी प्रतिभा से लाभान्वित होते हैं जो सौंदर्यशास्त्र और कार्यक्षमता दोनों को प्राथमिकता देते हैं. इसकी प्रभावशाली क्रूरता और स्थायित्व के साथ, मैग्नीशियम उपभोक्ता इलेक्ट्रॉनिक्स की गतिशील दुनिया में डाई-कास्ट उत्पादों की दीर्घायु और विश्वसनीयता सुनिश्चित करता है.
एयरोस्पेस उद्योग
एयरोस्पेस सेक्टर विमान और अंतरिक्ष यान के लिए आवश्यक हल्के अभी तक मजबूत घटक के उत्पादन के लिए एल्यूमीनियम डाई कास्टिंग पर निर्भर करता है. एल्यूमीनियम मिश्र धातुओं का उच्च शक्ति-से-वजन अनुपात उन्हें एयरोस्पेस अनुप्रयोगों के लिए अच्छी तरह से अनुकूल बनाता है जहां संरचनात्मक अखंडता से समझौता किए बिना वजन कम करना महत्वपूर्ण है. धड़ भागों से लेकर आंतरिक घटकों तक, एल्यूमीनियम डाई कास्टिंग उड़ान प्रदर्शन को बढ़ाने में योगदान करते हैं, ईंधन दक्षता, और एयरोस्पेस उद्योग में समग्र सुरक्षा मानक.
निष्कर्ष
विभिन्न गुणों और डाई कास्टिंग सामग्री के अनुप्रयोगों की एक समझ के साथ, आप इस बहुमुखी विनिर्माण प्रक्रिया की क्षमता को अनलॉक करने के लिए अपने रास्ते पर हैं. याद करना, सही कास्टिंग धातु का चयन केवल अंतिम उत्पाद के बारे में नहीं है; यह सीधे लागत-प्रभावशीलता को प्रभावित करता है, गुणवत्ता, और डाई कास्टिंग प्रक्रिया की समग्र दक्षता ही.
आगे देख रहा, भविष्य के रुझान विभिन्न क्षेत्रों में डाई कास्टिंग की बढ़ती मांग का संकेत देते हैं, उभरती हुई सामग्री और उद्योग के विकास के बारे में सूचित रहने के महत्व पर जोर देना.