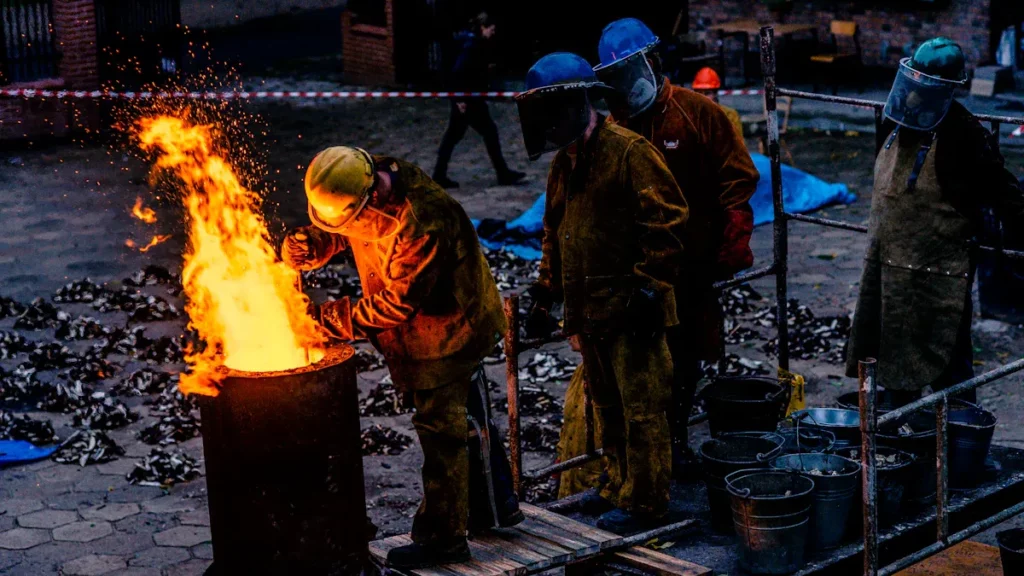
छवि स्रोत: unsplash
डाई कास्टिंग उच्च परिशुद्धता के साथ जटिल धातु घटकों के उत्पादन के लिए एक महत्वपूर्ण विनिर्माण प्रक्रिया के रूप में कार्य करता है. सामग्री चयन दक्षता का निर्धारण करने में महत्वपूर्ण भूमिका निभाता है, टिकाऊपन, और डाई-कास्ट उत्पादों की लागत-प्रभावशीलता. की बहस में मैग्नीशियम बनाम. एल्युमिनियम डाई कास्टिंग, दोनों सामग्री उनके अद्वितीय भौतिक और यांत्रिक गुणों के कारण लोकप्रिय विकल्पों के रूप में खड़ी हैं. मैग्नीशियम एक प्रदान करता है असाधारण शक्ति-से-भार अनुपात, जबकि एल्यूमीनियम बेहतर संक्षारण प्रतिरोध और तापीय चालकता प्रदान करता है. The इन धातुओं की विशिष्ट विशेषताएँ मोटर वाहन जैसे उद्योगों के लिए उन्हें अपरिहार्य बनाएं, एयरोस्पेस, और इलेक्ट्रॉनिक्स.
मैग्नीशियम बनाम. एल्युमिनियम डाई कास्टिंग: एक अवलोकन
डाई कास्टिंग में मैग्नीशियम
मैग्नीशियम के सामान्य गुण
मैग्नीशियम डाई कास्टिंग में उपयोग किए जाने वाले सबसे हल्के संरचनात्मक धातुओं में से एक के रूप में खड़ा है. मैग्नीशियम का घनत्व लगभग है 1.74 g/cm g, यह एल्यूमीनियम की तुलना में एक तिहाई हल्का है. मैग्नीशियम मिश्र उत्कृष्टता का प्रदर्शन करते हैं, पतली-दीवारों वाले और जटिल ज्यामिति के उत्पादन के लिए अनुमति. मैग्नीशियम का पिघलने बिंदु लगभग 650 डिग्री सेल्सियस है, जो कास्टिंग प्रक्रिया के दौरान तेजी से हीटिंग और कूलिंग साइकिल की सुविधा देता है. मैग्नीशियम प्रस्ताव उच्च मशीन, पोस्ट-कास्टिंग संचालन में सटीकता को सक्षम करना.
मैग्नीशियम का उपयोग करने के लाभ
मैग्नीशियम डाई कास्टिंग प्रदान करता है कई लाभ उद्योगों की आवश्यकता के लिए हल्के घटक. मैग्नीशियम मिश्र धातुओं का असाधारण शक्ति-से-वजन अनुपात ऑटोमोटिव और एयरोस्पेस जैसे अनुप्रयोगों में प्रदर्शन को बढ़ाता है. तेजी से चक्र समय कास्टिंग के दौरान उत्पादन दक्षता में सुधार, विनिर्माण लीड समय को कम करना. मैग्नीशियम बेहतर ऊर्जा अवशोषण गुण प्रदर्शित करता है, यह प्रभाव-प्रतिरोधी भागों के लिए उपयुक्त है. उच्च कठोरता और पहनने के प्रतिरोध की मांग वातावरण में इसकी उपयोगिता में योगदान करते हैं. मैग्नीशियम उन्नत इंजीनियरिंग प्लास्टिक की तुलना में बेहतर आयामी स्थिरता भी प्रदान करता है.
डाई कास्टिंग में मैग्नीशियम की सीमाएँ
मैग्नीशियम डाई कास्टिंग प्रक्रिया के दौरान कुछ चुनौतियां प्रस्तुत करता है. मैग्नीशियम की ज्वलनशीलता को विनिर्माण के दौरान आग के जोखिमों को कम करने के लिए विशेष हैंडलिंग की आवश्यकता होती है. मैग्नीशियम भाग अक्सर अतिरिक्त पोस्ट-प्रोडक्शन प्रोसेसिंग की मांग करते हैं, समग्र लागत बढ़ रही है. मैग्नीशियम का संक्षारण प्रतिरोध एल्यूमीनियम की तुलना में कम है, कठोर वातावरण में अनुप्रयोगों के लिए सुरक्षात्मक कोटिंग्स की आवश्यकता. मैग्नीशियम की कम तन्यता ताकत उच्च-तनाव अनुप्रयोगों में इसके उपयोग को सीमित करती है. मैग्नीशियम कच्चे माल आम तौर पर एल्यूमीनियम की तुलना में अधिक महंगे होते हैं, लागत-प्रभावशीलता को प्रभावित करना.
डाई कास्टिंग में एल्यूमीनियम
एल्यूमीनियम के सामान्य गुण
एल्यूमीनियम एक बहुमुखी धातु है जिसका उपयोग व्यापक रूप से अपने अनुकूल गुणों के कारण डाई कास्टिंग में किया जाता है. एल्यूमीनियम का घनत्व लगभग है 2.7 g/cm g, हल्के डिजाइन और यांत्रिक शक्ति के बीच संतुलन की पेशकश. एल्यूमीनियम का पिघलने बिंदु 580 डिग्री सेल्सियस से 670 डिग्री सेल्सियस तक होता है, मिश्र धातु रचना पर निर्भर करता है. एल्यूमीनियम मिश्र धातु उत्कृष्ट संक्षारण प्रतिरोध प्रदर्शित करता है, उन्हें बाहरी और समुद्री अनुप्रयोगों के लिए आदर्श बनाना. सुपीरियर थर्मल और विद्युत चालकता आगे विभिन्न उद्योगों में एल्यूमीनियम की कार्यक्षमता को बढ़ाती है.
एल्यूमीनियम का उपयोग करने के लाभ
एल्यूमीनियम डाई कास्टिंग निर्माताओं के लिए कई फायदे देता है. एल्यूमीनियम मिश्र धातुओं की उच्च तन्यता ताकत तनाव के तहत स्थायित्व और स्थिरता सुनिश्चित करती है. एल्यूमीनियम का संक्षारण प्रतिरोध नमी या रसायनों के संपर्क में आने वाले घटकों के जीवनकाल का विस्तार करता है. एल्यूमीनियम की सुपीरियर थर्मल चालकता इलेक्ट्रॉनिक्स हाउसिंग जैसे अनुप्रयोगों में गर्मी अपव्यय का समर्थन करती है. मैग्नीशियम की तुलना में कम लागत पर एल्यूमीनियम की उपलब्धता बड़े पैमाने पर उत्पादन के लिए एक किफायती विकल्प बनाती है. एल्यूमीनियम डाई कास्टिंग भी सतह खत्म की एक विस्तृत श्रृंखला को समायोजित करता है, सौंदर्यशास्त्र अपील को बढ़ाना.
डाई कास्टिंग में एल्यूमीनियम की सीमाएँ
एल्यूमीनियम डाई कास्टिंग में कुछ बाधाएं हैं जिन पर विचार की आवश्यकता है. मैग्नीशियम की तुलना में एल्यूमीनियम का उच्च घनत्व भारी घटकों में होता है, जो वजन-संवेदनशील अनुप्रयोगों के अनुरूप नहीं हो सकता है. कास्टिंग के दौरान लंबे समय तक समय एल्यूमीनियम की उच्च गर्मी क्षमता के कारण उत्पन्न होता है, उत्पादन दरों को धीमा करना. एल्यूमीनियम मैग्नीशियम की तुलना में कम मशीनबिलिटी प्रदर्शित करता है, पोस्ट-कास्टिंग संचालन की जटिलता में वृद्धि. एल्यूमीनियम मिश्र धातुओं की कम शक्ति-से-वजन अनुपात चरम हल्की दक्षता की मांग करने वाले अनुप्रयोगों में उनके प्रदर्शन को सीमित करता है.
भौतिक और यांत्रिक गुण तुलना
भार और घनत्व
मैग्नीशियम का हल्का लाभ
मैग्नीशियम में एक महत्वपूर्ण लाभ प्रदान करता है भार-संवेदनशील अनुप्रयोग इसके कम घनत्व के कारण. मैग्नीशियम का घनत्व लगभग है 1.74 g/cm g, इसके बारे में बना रहा है 33% हल्का एल्यूमीनियम से. यह हल्का प्रकृति घटकों के समग्र द्रव्यमान को कम करती है, जो मोटर वाहन और एयरोस्पेस उद्योगों में ईंधन दक्षता को बढ़ाता है. मैग्नीशियम विनिर्माण प्रक्रियाओं के दौरान आसान हैंडलिंग को भी सक्षम बनाता है. कम वजन उच्च गतिशीलता या पोर्टेबिलिटी की आवश्यकता वाले अनुप्रयोगों में बेहतर प्रदर्शन में योगदान देता है.
एल्यूमीनियम का वजन और शक्ति संतुलन
एल्यूमीनियम हल्के गुणों और यांत्रिक शक्ति के बीच एक संतुलन प्रदान करता है. एल्यूमीनियम का घनत्व आसपास है 2.7 g/cm g, जो मैग्नीशियम से अधिक है लेकिन अन्य धातुओं की तुलना में अभी भी अपेक्षाकृत कम है. यह संतुलन एल्यूमीनियम को उन अनुप्रयोगों के लिए उपयुक्त बनाता है जहां वजन में कमी और संरचनात्मक अखंडता दोनों महत्वपूर्ण हैं. मध्यम वजन की पेशकश करते समय ताकत बनाए रखने की एल्यूमीनियम की क्षमता बड़े पैमाने पर इसके उपयोग का समर्थन करती है, पतली दीवार, और जटिल भागों. एल्यूमीनियम की बहुमुखी प्रतिभा विभिन्न उद्योगों में इसकी व्यापक गोद लेने के लिए सुनिश्चित करती है.
ताकत और स्थायित्व
मैग्नीशियम की तन्य शक्ति
मैग्नीशियम एल्यूमीनियम की तुलना में कम तन्य शक्ति प्रदर्शित करता है, जो उच्च-तनाव वातावरण में इसके आवेदन को सीमित करता है. मैग्नीशियम मिश्र धातुओं की तन्यता ताकत आमतौर पर होती है 150 एमपीए को 240 एमपीए, विशिष्ट मिश्र धातु रचना पर निर्भर करता है. इस सीमा के बावजूद, मैग्नीशियम उत्कृष्ट लोच और ऊर्जा अवशोषण गुणों को प्रदर्शित करता है. ये विशेषताएं प्रभाव प्रतिरोध की आवश्यकता वाले घटकों के लिए मैग्नीशियम आदर्श बनाती हैं. मैग्नीशियम की निचली ताकत अक्सर स्थायित्व सुनिश्चित करने के लिए अतिरिक्त डिजाइन विचारों की आवश्यकता होती है.
एल्यूमीनियम की तन्य शक्ति
एल्यूमीनियम तन्य शक्ति में मैग्नीशियम को पार करता है, उन मूल्यों की पेशकश जो से होती है 200 एमपीए से अधिक 400 एमपीए, मिश्र धातु पर निर्भर करता है. यह उच्च तन्यता ताकत एल्यूमीनियम घटकों को विरूपण के बिना अधिक भार और तनाव का सामना करने की अनुमति देती है. एल्यूमीनियम भी बेहतर थकान प्रतिरोध प्रदर्शित करता है, जो बार -बार यांत्रिक तनाव के अधीन अनुप्रयोगों में इसके प्रदर्शन को बढ़ाता है. शक्ति और स्थायित्व का संयोजन एल्यूमीनियम को एयरोस्पेस और समुद्री उद्योगों जैसे वातावरण की मांग के लिए एक पसंदीदा विकल्प बनाता है.
थर्मल और विद्युत चालकता
मैग्नीशियम की चालकता गुण
मैग्नीशियम मध्यम थर्मल और विद्युत चालकता प्रदान करता है, जो विशिष्ट अनुप्रयोगों में इसके उपयोग का समर्थन करता है. मैग्नीशियम की तापीय चालकता लगभग है 156 डब्ल्यू/एम · के, जो हल्के घटकों में कुशल गर्मी अपव्यय की सुविधा देता है. मैग्नीशियम की चालकता गुण इलेक्ट्रॉनिक्स हाउसिंग में विशेष रूप से फायदेमंद हैं जहां वजन में कमी और थर्मल प्रबंधन आवश्यक हैं. मैग्नीशियम के निचले पिघलने बिंदु, लगभग 650 डिग्री सेल्सियस, डाई कास्टिंग के दौरान तेजी से शीतलन समय में योगदान देता है, उत्पादन दक्षता में सुधार.
एल्यूमीनियम की चालकता गुण
एल्यूमीनियम मैग्नीशियम की तुलना में बेहतर थर्मल और विद्युत चालकता प्रदान करता है. एल्यूमीनियम की तापीय चालकता लगभग है 237 डब्ल्यू/एम · के, गर्मी को विघटित करने में यह अत्यधिक प्रभावी है. यह संपत्ति हीट एक्सचेंजर्स और इलेक्ट्रॉनिक घटकों जैसे अनुप्रयोगों के लिए महत्वपूर्ण है. एल्यूमीनियम की उत्कृष्ट विद्युत चालकता बिजली संचरण और वितरण प्रणालियों में इसकी उपयोगिता को और बढ़ाती है. एल्यूमीनियम की उच्च चालकता कुशल गर्मी और ऊर्जा हस्तांतरण की आवश्यकता वाले वातावरण में इष्टतम प्रदर्शन सुनिश्चित करती है.
अनुप्रयोग और उद्योग के उपयोग के मामले
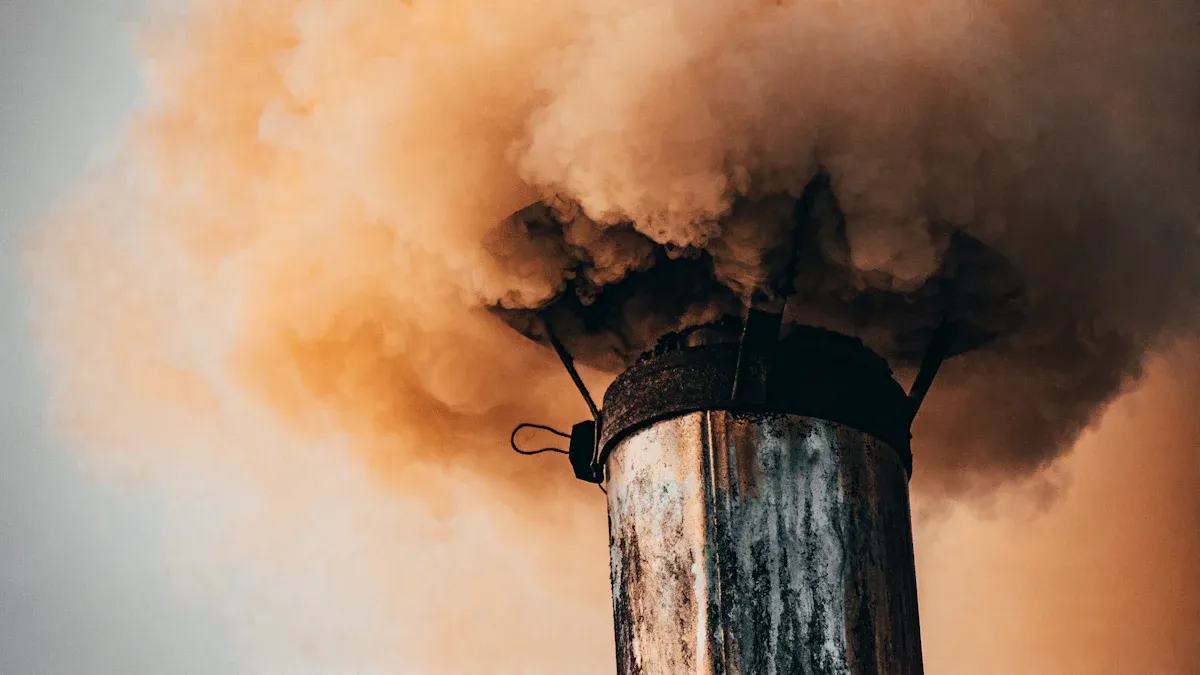
मोटर वाहन उद्योग
मोटर वाहन घटकों में मैग्नीशियम
मैग्नीशियम डाई कास्टिंग हल्के घटकों के उत्पादन को सक्षम करके मोटर वाहन उद्योग में एक महत्वपूर्ण भूमिका निभाता है. मैग्नीशियम भाग लगभग हैं 33% हल्का एल्यूमीनियम भागों की तुलना में, जो वाहनों के समग्र वजन को काफी कम कर देता है. यह वजन कम करने से ईंधन दक्षता में सुधार होता है और वाहन हैंडलिंग को बढ़ाता है. मोटर वाहन निर्माता उपयोग करते हैं मैग्नीशियम मिश्र धातु विभिन्न घटकों के लिए, सीट फ्रेम सहित, चालन चक्र, दरवाजे का हैंडल, और दर्पण कोष्ठक. उच्च ताकत-से-भार अनुपात मैग्नीशियम एक हल्के डिजाइन को बनाए रखते हुए स्थायित्व सुनिश्चित करता है. मैग्नीशियम मिश्र धातुओं का उपयोग भी समर्थन करता है इलेक्ट्रिक वाहनों का विकास हल्के विकल्प के साथ भारी घटकों को बदलकर.
मोटर वाहन घटकों में एल्यूमीनियम
एल्यूमीनियम ताकत और हल्के गुणों के संतुलन के कारण मोटर वाहन निर्माण में एक आधारशिला सामग्री बनी हुई है. एल्यूमीनियम डाई कास्टिंग वाहन के प्रदर्शन और सुरक्षा को बढ़ाने वाले मजबूत घटक प्रदान करता है. सामान्य अनुप्रयोगों में इंजन ब्लॉक शामिल हैं, पारेषण आवास, और निलंबन भागों. एल्यूमीनियम का बेहतर संक्षारण प्रतिरोध नमी या कठोर वातावरण के संपर्क में आने वाले घटकों के लिए दीर्घायु सुनिश्चित करता है. इंजन और ब्रेकिंग सिस्टम के लिए गर्मी अपव्यय में एल्यूमीनियम एड्स की थर्मल चालकता. एल्यूमीनियम की लागत-प्रभावशीलता इसे बड़े पैमाने पर मोटर वाहन उत्पादन के लिए एक आकर्षक विकल्प बनाती है. निर्माता वजन दक्षता से समझौता किए बिना इष्टतम संरचनात्मक अखंडता प्राप्त करने के लिए एल्यूमीनियम मिश्र धातुओं पर भरोसा करते हैं.
एयरोस्पेस उद्योग
एयरोस्पेस में मैग्नीशियम की भूमिका
मैग्नीशियम मिश्र धातुओं को एयरोस्पेस इंजीनियरिंग में प्रगति में योगदान देता है जो अद्वितीय वजन बचत की पेशकश करता है. एयरोस्पेस उद्योग ईंधन दक्षता और पेलोड क्षमता में सुधार के लिए हल्के सामग्री को प्राथमिकता देता है. मैग्नीशियम डाई कास्ट पार्ट्स, जैसे सीट राइजर, कंसोल कोष्ठक, और क्लच ब्रैकेट, समग्र विमान के वजन को कम करते हुए महत्वपूर्ण अनुप्रयोगों के लिए आवश्यक ताकत प्रदान करें. मैग्नीशियम के ऊर्जा अवशोषण गुण प्रभाव-प्रवण क्षेत्रों में सुरक्षा को बढ़ाते हैं. उच्च तापमान मैग्नीशियम मिश्र धातुओं के विकास ने चरम स्थितियों के अधीन एयरोस्पेस घटकों में इसके उपयोग का विस्तार किया है. मैग्नीशियम की मशीनीता एयरोस्पेस डिजाइनों में आवश्यक जटिल ज्यामिति के उत्पादन में सटीकता के लिए अनुमति देती है.
एयरोस्पेस में एल्यूमीनियम की भूमिका
एल्यूमीनियम लंबे समय से एयरोस्पेस अनुप्रयोगों में एक पसंदीदा सामग्री है जो अपनी उत्कृष्ट शक्ति और संक्षारण प्रतिरोध के कारण है. एल्यूमीनियम डाई कास्टिंग धड़ पैनल जैसे टिकाऊ घटकों के उत्पादन को सक्षम बनाता है, विंग संरचना, और लैंडिंग गियर भागों. एल्यूमीनियम की उच्च तन्यता ताकत यांत्रिक तनाव के तहत स्थिरता सुनिश्चित करती है. एल्यूमीनियम की बेहतर तापीय चालकता विमान प्रणालियों में गर्मी का प्रबंधन करने में मदद करती है, जैसे इंजन और एवियोनिक्स. एल्यूमीनियम मिश्र धातुओं की हल्की प्रकृति एयरोस्पेस उद्योग के ईंधन दक्षता और कम उत्सर्जन पर ध्यान केंद्रित करती है. एल्यूमीनियम की बहुमुखी प्रतिभा इसे संरचनात्मक और गैर-संरचनात्मक एयरोस्पेस दोनों घटकों के लिए उपयुक्त बनाती है.
उपभोक्ता इलेक्ट्रॉनिक्स
इलेक्ट्रॉनिक्स आवासों में मैग्नीशियम
मैग्नीशियम डाई कास्टिंग उपभोक्ता इलेक्ट्रॉनिक्स के लिए अद्वितीय लाभ प्रदान करता है, विशेष रूप से हल्के और टिकाऊ आवासों के उत्पादन में. मैग्नीशियम का कम घनत्व उपकरणों के वजन को कम करता है, पोर्टेबिलिटी और उपयोगकर्ता अनुभव को बढ़ाना. इलेक्ट्रॉनिक घटकों के लिए गर्मी अपव्यय में मैग्नीशियम एड्स की थर्मल चालकता, इष्टतम प्रदर्शन सुनिश्चित करना. मैग्नीशियम की उच्च सहिष्णुता प्राप्त करने की क्षमता कॉम्पैक्ट उपकरणों में जटिल डिजाइनों के लिए अनुमति देती है. सामान्य अनुप्रयोगों में लैपटॉप केसिंग शामिल हैं, कैमरा निकाय, और मोबाइल फोन फ्रेम. शक्ति और हल्के गुणों का संयोजन मैग्नीशियम को आधुनिक इलेक्ट्रॉनिक्स के लिए एक आदर्श विकल्प बनाता है.
इलेक्ट्रॉनिक्स आवासों में एल्यूमीनियम
एल्यूमीनियम इसकी उत्कृष्ट तापीय चालकता और संक्षारण प्रतिरोध के कारण इलेक्ट्रॉनिक्स हाउसिंग के लिए एक लोकप्रिय सामग्री बनी हुई है. एल्यूमीनियम डाई कास्टिंग स्मार्टफोन जैसे उपकरणों के लिए मजबूत और सौंदर्यवादी रूप से मनभावन केसिंग का उत्पादन करता है, गोलियां, और ऑडियो उपकरण. एल्यूमीनियम की उच्च तन्यता ताकत शारीरिक क्षति के खिलाफ आंतरिक घटकों के लिए सुरक्षा सुनिश्चित करती है. विभिन्न सतह खत्म को समायोजित करने की एल्यूमीनियम की क्षमता उपभोक्ता इलेक्ट्रॉनिक्स की दृश्य अपील को बढ़ाती है. एल्यूमीनियम की लागत-प्रभावशीलता बड़े पैमाने पर उत्पादन में इसके व्यापक उपयोग का समर्थन करती है. निर्माता इलेक्ट्रॉनिक उपकरणों के लिए टिकाऊ और कुशल समाधान देने के लिए एल्यूमीनियम मिश्र धातुओं पर भरोसा करते हैं.
लागत और पर्यावरणीय विचार
कच्चे माल की लागत
मैग्नीशियम के लिए मूल्य रुझान
मैग्नीशियम एक प्रदर्शित करता है प्रति किलोग्राम उच्च लागत इसके जटिल निष्कर्षण और शोधन प्रक्रियाओं के कारण एल्यूमीनियम की तुलना में. मैग्नीशियम की कीमत आमतौर पर चारों ओर घूमती है $2.00 प्रति किलोग्राम. यह लागत सीमित प्राकृतिक भंडार से सोर्सिंग मैग्नीशियम और इसके उत्पादन के लिए आवश्यक ऊर्जा-गहन तरीकों से जुड़ी चुनौतियों को दर्शाती है. पोस्ट-प्रोडक्शन प्रोसेसिंग आगे बढ़ती है मैग्नीशियम का समग्र व्यय मेटल सांचों में ढालना, यह निर्माताओं के लिए एक प्रीमियम विकल्प है.
एल्यूमीनियम के लिए मूल्य रुझान
एल्यूमीनियम एक अधिक किफायती विकल्प प्रदान करता है, लगभग प्रति किलोग्राम औसत लागत के साथ औसत $2.50. एल्यूमीनियम की व्यापक उपलब्धता इसकी सामर्थ्य में योगदान देती है. एल्यूमीनियम के लिए निष्कर्षण और शोधन प्रक्रियाएं कम जटिल हैं, जो उत्पादन लागत को कम करता है. एल्यूमीनियम का कम कच्चा माल खर्च इसे उच्च-मात्रा विनिर्माण के लिए एक पसंदीदा विकल्प बनाता है, विशेष रूप से उन उद्योगों में जहां बजट की कमी एक महत्वपूर्ण भूमिका निभाती है.
पर्यावरणीय प्रभाव
मैग्नीशियम की स्थिरता
मैग्नीशियम इसकी कम रीसाइक्लिंग दर के कारण अद्वितीय स्थिरता चुनौतियां प्रस्तुत करता है. ऊपर 50% उपभोक्ता मैग्नीशियम स्क्रैप गैर-कार्यात्मक रीसाइक्लिंग या निपटान के लिए खो जाता है. यह अक्षमता डाई कास्टिंग में मैग्नीशियम के पर्यावरणीय लाभों को सीमित करती है. तथापि, मैग्नीशियम में एक महत्वपूर्ण भूमिका निभाता है टिकाऊ विनिर्माण को बढ़ावा देना जब एल्यूमीनियम मिश्र धातुओं में उपयोग किया जाता है. एल्यूमीनियम मिश्र में मैग्नीशियम का एकीकरण सामग्री दक्षता को बढ़ाता है और कचरे को कम करता है, एक अधिक परिपत्र अर्थव्यवस्था को बढ़ावा देना.
एल्यूमीनियम की स्थिरता
एल्यूमीनियम इसकी उच्च रीसाइक्लिंग दर और लंबे जीवनचक्र के कारण बेहतर स्थिरता प्रदर्शित करता है. गुणवत्ता के महत्वपूर्ण नुकसान के बिना एल्यूमीनियम को रीसायकल करने की क्षमता कुंवारी सामग्री की मांग को कम करती है. यह विशेषता एल्यूमीनियम डाई कास्टिंग के पर्यावरणीय पदचिह्न को कम करती है. एल्यूमीनियम के स्थायित्व और संक्षारण प्रतिरोध भी घटकों के जीवनकाल का विस्तार करते हैं, समय के साथ कम संसाधन की खपत में योगदान देना. ये विशेषताएँ कई अनुप्रयोगों में एल्यूमीनियम को अधिक पर्यावरण के अनुकूल विकल्प बनाती हैं.
अपनी डाई कास्टिंग जरूरतों के लिए सही सामग्री चुनना
विचार करने के लिए कारक
अनुप्रयोग-विशिष्ट आवश्यकताएँ
सामग्री चयन सीधे उत्पाद प्रदर्शन और कार्यक्षमता को प्रभावित करता है. मैग्नीशियम मिश्र धातुओं में उच्च शक्ति-से-वजन अनुपात के साथ हल्के घटकों की आवश्यकता वाले अनुप्रयोगों में एक्सेल. एल्यूमीनियम मिश्र धातु नमी या रसायनों के संपर्क में आने वाले वातावरण के लिए बेहतर स्थायित्व और संक्षारण प्रतिरोध प्रदान करते हैं. मैग्नीशियम उत्कृष्ट मशीनीकरण के कारण जटिल डिजाइनों का समर्थन करता है, जबकि एल्यूमीनियम मजबूत यांत्रिक गुणों के साथ बड़ी संरचनाओं को समायोजित करता है. थर्मल चालकता आवश्यकताएं गर्मी अपव्यय अनुप्रयोगों में एल्यूमीनियम का पक्ष लेते हैं, जबकि मैग्नीशियम ने तेजी से उत्पादन चक्रों को प्राथमिकता देते हुए डिजाइन किया है.
बजट बाधाएं
लागत दक्षता भौतिक विकल्प में एक महत्वपूर्ण भूमिका निभाती है. मैग्नीशियम इक्म्स उच्च कच्चे माल की लागत जटिल निष्कर्षण और शोधन प्रक्रियाओं के कारण. एल्यूमीनियम व्यापक उपलब्धता और कम प्रसंस्करण व्यय के कारण बड़े पैमाने पर उत्पादन के लिए अधिक किफायती विकल्प प्रदान करता है. पोस्ट-प्रोडक्शन की लागत भी काफी भिन्न होती है. मैग्नीशियम को जंग प्रतिरोध के लिए अतिरिक्त सुरक्षात्मक कोटिंग्स की आवश्यकता होती है, समग्र खर्चों में वृद्धि. एल्यूमीनियम प्रदान करता है लागत-प्रभावी समाधान न्यूनतम पोस्ट-प्रोसेसिंग जरूरतों के साथ, इसे बजट-संवेदनशील परियोजनाओं के लिए आदर्श बना रहा है.
व्यावहारिक सिफारिशें
मैग्नीशियम का चयन कब करें
मैग्नीशियम डाई कास्टिंग वजन-संवेदनशील अनुप्रयोगों में इष्टतम परिणाम प्रदान करता है. ऑटोमोटिव और एयरोस्पेस उद्योग मैग्नीशियम के हल्के गुणों से लाभान्वित होते हैं, ईंधन दक्षता और पेलोड क्षमता बढ़ाना. इलेक्ट्रॉनिक्स निर्माता कॉम्पैक्ट हाउसिंग के लिए मैग्नीशियम का उपयोग करते हैं जो गर्मी विघटन के साथ पोर्टेबिलिटी को जोड़ते हैं. उच्च मशीनबिलिटी मैग्नीशियम को सटीक घटकों के लिए उपयुक्त बनाती है, जिसमें जटिल ज्यामितीय की आवश्यकता होती है. उत्पादन के दौरान तेजी से चक्र का समय दक्षता में सुधार होता है, तंग विनिर्माण कार्यक्रम के साथ सहायक उद्योग.
जब एल्यूमीनियम चुनें
एल्यूमीनियम डाई कास्टिंग अनुप्रयोगों की मांग के लिए लाभ प्रदान करता है ताकत और स्थायित्व. एयरोस्पेस और समुद्री उद्योग यांत्रिक तनाव और संक्षारक वातावरण के संपर्क में आने वाले घटकों के लिए एल्यूमीनियम पर भरोसा करते हैं. इलेक्ट्रॉनिक्स निर्माता बेहतर तापीय चालकता और सौंदर्य फिनिश की आवश्यकता वाले आवासों के लिए एल्यूमीनियम पसंद करते हैं. एल्यूमीनियम की सामर्थ्य और बहुमुखी प्रतिभा से बड़े पैमाने पर उत्पादन लाभ. एल्यूमीनियम मिश्र धातु विभिन्न डिजाइन आवश्यकताओं को समायोजित करते हैं, लागत-प्रभावशीलता से समझौता किए बिना संरचनात्मक अखंडता सुनिश्चित करना.
मैग्नीशियम बनाम. एल्युमिनियम डाई कास्टिंग पर प्रकाश डाला गया विशिष्ट लाभ विभिन्न अनुप्रयोगों के लिए. मैग्नीशियम बेजोड़ वजन बचत प्रदान करता है, श्रेष्ठता, और तेजी से उत्पादन चक्र. एल्यूमीनियम उच्च तन्य शक्ति प्रदान करता है, बेहतर संक्षारण प्रतिरोध, और उत्कृष्ट तापीय चालकता. सामग्री चयन विशिष्ट उद्योग की जरूरतों पर निर्भर करता है, जैसे कि हल्के दक्षता या तनाव के तहत स्थायित्व. डाई-कास्टिंग विशेषज्ञों के साथ परामर्श प्रदर्शन और लागत-प्रभावशीलता के लिए इष्टतम विकल्प सुनिश्चित करता है. दोनों सामग्री मोटर वाहन में प्रगति को आकार देने के लिए जारी है, एयरोस्पेस, और इलेक्ट्रॉनिक्स विनिर्माण.