विनिर्माण के क्षेत्र में, परिशुद्धता और दक्षता सर्वोपरि है. यहीं पर 5 अक्ष मशीनिंग कदम उठाती है, जटिल भागों को तैयार करने के तरीके में क्रांतिकारी बदलाव. लेकिन वास्तव में क्या है 5 अक्ष मशीनिंग, और यह पारंपरिक मशीनिंग विधियों से किस प्रकार भिन्न है? इस व्यापक मार्गदर्शिका में, हम की दुनिया में उतरेंगे 5 अक्ष मशीनिंग, इसके मूल सिद्धांतों की खोज, अनुप्रयोग, फ़ायदे, और भी बहुत कुछ.
मशीनिंग की मूल बातें समझना
इससे पहले कि हम इसकी पेचीदगियों में उतरें 5 अक्ष मशीनिंग, आइए समझकर एक नींव रखें मशीनिंग की मूल बातें. मशीनिंग सामग्री को आकार देने की प्रक्रिया है, आम तौर पर धातु, सटीक हिस्से या घटक बनाने के लिए. पारंपरिक मशीनिंग विधियाँ, जैसे कि 3 अक्ष मशीनिंग, इसमें ऐसे उपकरण शामिल होते हैं जो सामग्री को काटने के लिए तीन रैखिक अक्षों के साथ चलते हैं. ये विधियां प्रभावी हैं लेकिन जब जटिल आकार और रूपरेखा बनाने की बात आती है तो इनकी सीमाएं होती हैं.
क्या है 5 एक्सिस मशीनिंग?
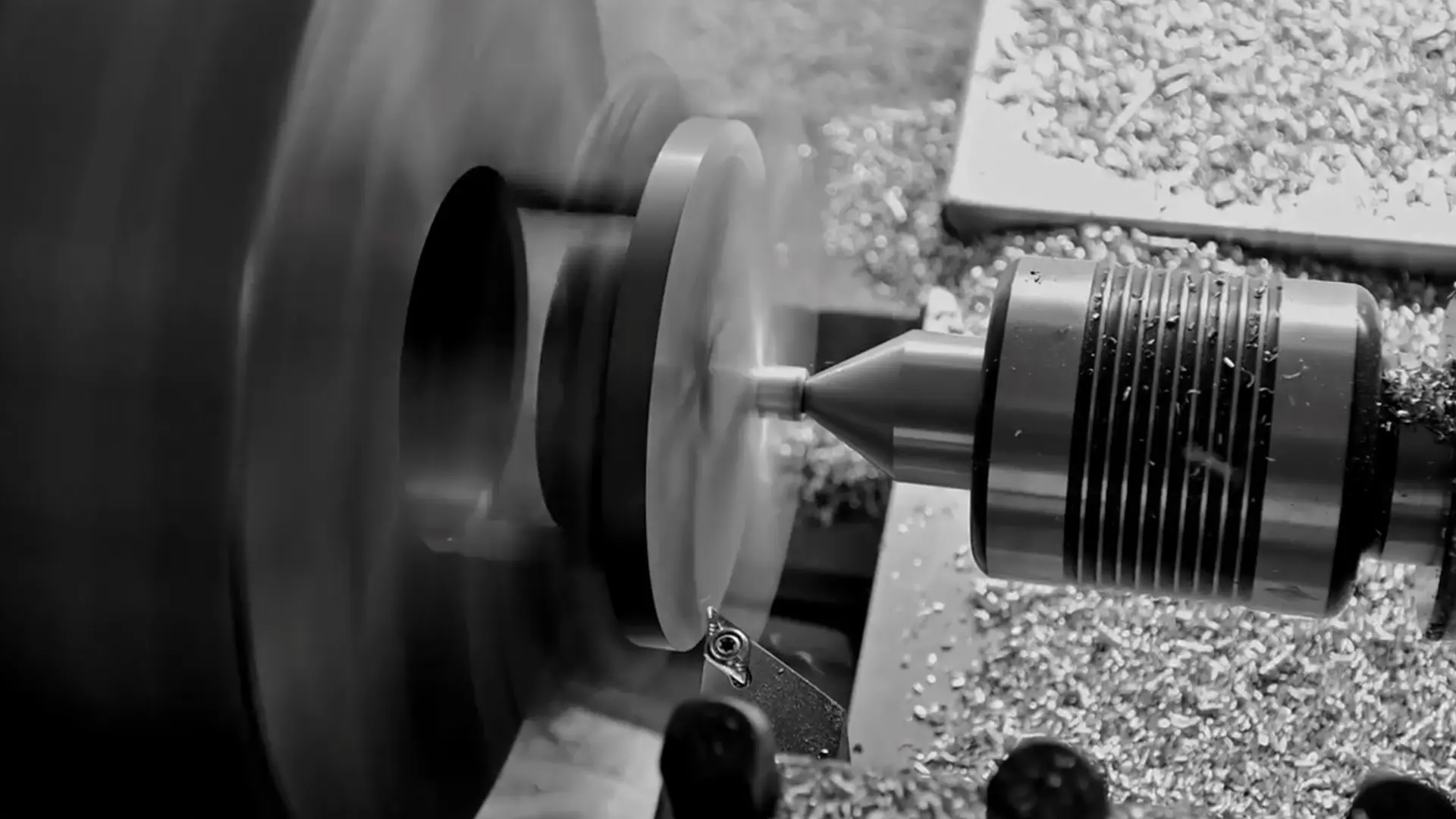
5 अक्ष मशीनिंग दो अतिरिक्त रोटरी अक्षों को शामिल करके सटीक इंजीनियरिंग को अगले स्तर पर ले जाता है, काटने के औजारों को गति की पांच अलग-अलग अक्षों पर चलने में सक्षम बनाना. भिन्न 3 अक्ष मशीनिंग, जहां काटने का उपकरण केवल तीन दिशाओं में ही चल सकता है (उतार व चढ़ाव, बाएँ और दाएँ, आगे और पीछे), 5 अक्ष मशीनिंग उपकरण को दो अतिरिक्त अक्षों के साथ घूमने की अनुमति देती है, आमतौर पर ए और बी अक्ष के रूप में जाना जाता है. यह बहुदिशात्मक आंदोलन अद्वितीय लचीलापन प्रदान करता है, सटीकता और दक्षता के साथ अत्यधिक जटिल और जटिल ज्यामिति बनाना संभव बनाता है.
कैसे हुआ 5 एक्सिस मशीनिंग कार्य?
समझना 5 अक्ष मशीनिंग, प्रत्येक अक्ष के साथ गति को समझना आवश्यक है:
- X- अक्ष: बाएँ से दाएँ क्षैतिज गति
- शाफ़्ट: आगे से पीछे तक क्षैतिज गति
- जेड एक्सिस: ऊर्ध्वाधर गति ऊपर और नीचे
- एक अक्ष: एक्स-अक्ष के चारों ओर घूर्णी गति
- ख अक्ष: Y-अक्ष के चारों ओर घूर्णी गति
- डिज़ाइन और प्रोग्रामिंग:
- एक सीएडी (कंप्यूटर एडेड डिजाइन) भाग का मॉडल बनाया गया है.
- कैम (कंप्यूटर सहायतायुक्त विनिर्माण) सॉफ़्टवेयर का उपयोग टूल पथ उत्पन्न करने के लिए किया जाता है.
- सॉफ़्टवेयर वांछित ज्यामिति प्राप्त करने के लिए काटने के उपकरण के लिए इष्टतम आंदोलनों और कोणों की गणना करता है.
- मशीन सेटअप:
- कच्चा माल (workpiece) मशीन टेबल या फिक्स्चर पर सुरक्षित है.
- सटीकता सुनिश्चित करने के लिए उपकरण और मशीन को कैलिब्रेट किया जाता है.
- यंत्र रीति:
- सीएनसी नियंत्रक सीएएम प्रोग्राम की व्याख्या करता है और मशीन के मोटर्स को सटीक कमांड भेजता है.
- काटने का उपकरण X के अनुदिश चलता है, वाई, और Z अक्ष A और B अक्षों के चारों ओर एक साथ घूमते हुए.
- यह समन्वित गति उपकरण को वस्तुतः किसी भी कोण से वर्कपीस तक पहुंचने की अनुमति देती है, जटिल आकृतियों और विशेषताओं को एक ही सेटअप में मशीनीकृत करने में सक्षम बनाना.
के अनुप्रयोग 5 एक्सिस मशीनिंग
की बहुमुखी प्रतिभा 5 एक्सिस मशीनिंग विभिन्न उद्योगों में अपने अनुप्रयोग का विस्तार करती है. यहां बताया गया है कि यह किस प्रकार विनिर्माण प्रक्रियाओं में क्रांति ला रहा है:
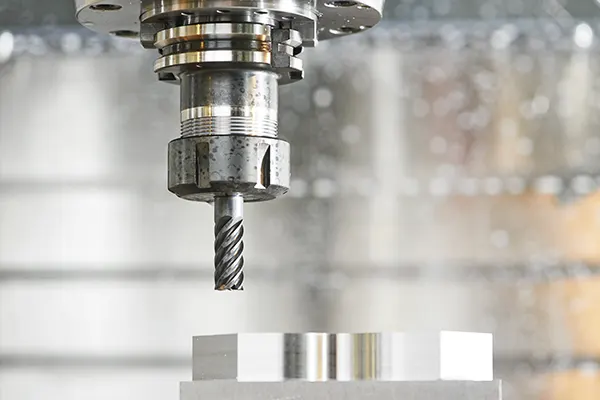
एयरोस्पेस उद्योग
एयरोस्पेस इंजीनियरिंग में, जहां घटक अत्यधिक सटीकता और जटिलता की मांग करते हैं, 5 अक्ष मशीनिंग अपरिहार्य है. टरबाइन ब्लेड से लेकर विमान के संरचनात्मक घटकों तक, 5 एक्सिस मशीनें एयरोस्पेस क्षेत्र के कठोर मानकों को पूरा करने के लिए आवश्यक सटीकता और जटिलता प्रदान करती हैं.
ऑटोमोटिव विनिर्माण
The मोटर वाहन उद्योग से अत्यधिक लाभ होता है 5 अक्ष मशीनिंग, विशेषकर इंजन घटकों के उत्पादन में, संचरण भाग, और जटिल बॉडी पैनल. साथ 5 अक्ष मशीनें, निर्माता बेहतर सतह फिनिश और सख्त सहनशीलता प्राप्त कर सकते हैं, वाहनों में इष्टतम प्रदर्शन और विश्वसनीयता सुनिश्चित करना.
चिकित्सा क्षेत्र
चिकित्सा क्षेत्र में, जहां अनुकूलित प्रत्यारोपण और प्रोस्थेटिक्स के लिए जटिल डिजाइन की आवश्यकता होती है, 5 अक्ष मशीनिंग अद्वितीय परिशुद्धता और बहुमुखी प्रतिभा प्रदान करती है. चाहे वह आर्थोपेडिक प्रत्यारोपण हो, दंत प्रोस्थेटिक्स, या शल्य चिकित्सा उपकरण, 5 एक्सिस मशीनिंग असाधारण सटीकता के साथ जटिल चिकित्सा उपकरणों के उत्पादन को सक्षम बनाती है.
उपकरण और डाई बनाना
5 एक्सिस मशीनिंग टूल और डाई बनाने में गेम-चेंजर है, जहां जटिल सांचे और डाई सटीक ज्यामिति की मांग करते हैं. रोजगार देकर 5 अक्ष मशीनें, उपकरण निर्माता जटिल रूपरेखा और बारीक विवरण के साथ सांचे और डाई बना सकते हैं, विनिर्माण उद्योग के सटीक मानकों को पूरा करना.
के फायदे 5 एक्सिस मशीनिंग
का गोद लेना 5 एक्सिस मशीनिंग से असंख्य लाभ मिलते हैं, यह परिशुद्धता और दक्षता चाहने वाले निर्माताओं के लिए एक पसंदीदा विकल्प बन गया है:
उन्नत परिशुद्धता
एक साथ कई अक्षों पर पैंतरेबाज़ी करने की क्षमता के साथ, 5 अक्ष मशीनिंग अद्वितीय परिशुद्धता सुनिश्चित करती है, अत्यधिक सटीकता के साथ जटिल ज्यामिति के निर्माण की अनुमति देना.
कम सेटअप समय
पारंपरिक मशीनिंग विधियों के विपरीत, जिसमें विभिन्न कोणों तक पहुंचने के लिए कई सेटअप की आवश्यकता होती है, 5 एक्सिस मशीनिंग एक ही सेटअप में जटिल कटौती को पूरा करती है, सेटअप समय को उल्लेखनीय रूप से कम करना और दक्षता बढ़ाना.
बढ़ी हुई दक्षता
वर्कपीस को पुनः स्थापित करने की आवश्यकता को समाप्त करके, 5 एक्सिस मशीनिंग विनिर्माण प्रक्रिया को सुव्यवस्थित करती है, इससे दक्षता में सुधार और उत्पादन चक्र में तेजी आएगी.
अनुकूलित सतह फिनिश
की बहुदिशात्मक गति 5 एक्सिस मशीनें चिकनी कटौती और बेहतर सतह फिनिश प्रदान करती हैं, जिसके परिणामस्वरूप उत्कृष्ट सौंदर्य अपील और कार्यात्मक प्रदर्शन के साथ बेहतर गुणवत्ता वाले हिस्से प्राप्त होते हैं.
विस्तारित डिज़ाइन स्वतंत्रता
5 एक्सिस मशीनिंग डिजाइनरों को जटिल आकार और रूपरेखा बनाने की अद्वितीय स्वतंत्रता प्रदान करती है, नवाचार की सीमाओं को आगे बढ़ाना और उत्पाद डिजाइन में नई संभावनाओं के द्वार खोलना.
चुनौतियाँ और विचार
जबकि 5 एक्सिस मशीनिंग कई लाभ प्रदान करती है, यह चुनौतियों और विचारों के सेट के साथ भी आता है:
जटिल प्रोग्रामिंग
की पूरी क्षमता का उपयोग करना 5 एक्सिस मशीनिंग के लिए जटिल टूलपाथ उत्पन्न करने और कटिंग रणनीतियों को अनुकूलित करने के लिए उन्नत प्रोग्रामिंग कौशल की आवश्यकता होती है, विशेष प्रशिक्षण और विशेषज्ञता की आवश्यकता.
मशीन की लागत और रखरखाव
में निवेश करना 5 एक्सिस मशीनिंग तकनीक में महत्वपूर्ण अग्रिम लागत शामिल होती है, और इन परिष्कृत मशीनों के रखरखाव के लिए नियमित रखरखाव और कुशल तकनीशियनों की आवश्यकता होती है, कुल परिचालन व्यय में वृद्धि.
वर्कपीस अभिगम्यता
इसकी बहुमुखी प्रतिभा के बावजूद, 5 अक्ष मशीनिंग को जटिल वर्कपीस के कुछ क्षेत्रों तक पहुँचने में सीमाओं का सामना करना पड़ सकता है, संपूर्ण मशीनिंग कवरेज सुनिश्चित करने के लिए रचनात्मक समाधान और विशेष फिक्स्चर तकनीकों की आवश्यकता होती है.
उपकरण हस्तक्षेप
की जटिल प्रकृति 5 अक्ष मशीनिंग से उपकरण के हस्तक्षेप का खतरा रहता है, उपकरण कहां है, धारक, या स्पिंडल वर्कपीस या फिक्सचर से टकरा सकता है, ऐसी घटनाओं को कम करने के लिए सावधानीपूर्वक योजना और अनुकरण की आवश्यकता है.
निष्कर्ष
आधुनिक विनिर्माण के गतिशील परिदृश्य में, 5 एक्सिस मशीनिंग सटीक इंजीनियरिंग के शिखर के रूप में सामने आती है, तेजी से जटिल और जटिल भागों की मांगों को पूरा करने के लिए अद्वितीय क्षमताएं प्रदान करना. डिज़ाइन नवाचार की सीमाओं को आगे बढ़ाने की अपनी क्षमता के साथ, दक्षता बढ़ाएँ, और बेहतर गुणवत्ता वाले घटक प्रदान करते हैं, 5 एक्सिस मशीनिंग विभिन्न उद्योगों में विनिर्माण के भविष्य को फिर से परिभाषित करना जारी रखती है. सहयोग करें बियान डाई कास्ट, हम शीर्ष स्तरीय पेशकश करते हैं 5 अक्ष सीएनसी मशीनिंग सेवाएँ जो जटिल घटकों के निर्माण में उच्चतम गुणवत्ता और दक्षता सुनिश्चित करते हैं.
पर अक्सर पूछे जाने वाले प्रश्न 5 एक्सिस मशीनिंग
1. वे कौन से प्राथमिक उद्योग हैं जिनसे लाभ होता है? 5 अक्ष मशीनिंग?
5 एक्सिस मशीनिंग का एयरोस्पेस में व्यापक अनुप्रयोग होता है, ऑटोमोटिव, चिकित्सा, और उपकरण और डाई बनाने वाले उद्योग, दूसरों के बीच में.
2. कैसे हुआ 5 अक्ष मशीनिंग पारंपरिक मशीनिंग विधियों से भिन्न है?
पारंपरिक मशीनिंग विधियों के विपरीत जो तीन रैखिक अक्षों के साथ काम करती हैं, 5 अक्ष मशीनिंग दो अतिरिक्त रोटरी अक्ष जोड़ती है, बहुदिशात्मक काटने की क्षमताओं को सक्षम करना.
3. इसके प्रमुख फायदे क्या हैं 5 अक्ष मशीनिंग?
के कुछ प्रमुख फायदे 5 अक्ष मशीनिंग में उन्नत परिशुद्धता शामिल है, सेटअप समय कम हो गया, बढ़ी हुई दक्षता, अनुकूलित सतह फ़िनिश, और डिज़ाइन की स्वतंत्रता का विस्तार किया.
4. मुख्य चुनौतियाँ किससे जुड़ी हैं? 5 अक्ष मशीनिंग?
में चुनौतियाँ 5 अक्ष मशीनिंग में जटिल प्रोग्रामिंग शामिल है, उच्च मशीन लागत और रखरखाव, वर्कपीस की पहुंच, और उपकरण हस्तक्षेप का जोखिम.
5. डब्ल्यूटोपी एक है 5 अक्ष मिलिंग मशीन?
ए 5 एक्सिस मिलिंग मशीन एक प्रकार की सीएनसी है (कंप्यूटर संख्यात्मक नियंत्रण) वह मशीन जो काटने के औजारों को एक साथ पांच अलग-अलग अक्षों पर घुमा सकती है. पारंपरिक के विपरीत 3 अक्ष मशीनें, जो एक्स के साथ चलते हैं, वाई, और Z रैखिक अक्ष, ए 5 एक्सिस मिलिंग मशीन में दो अतिरिक्त रोटरी कुल्हाड़ियाँ भी शामिल हैं (आमतौर पर ए और बी अक्ष के रूप में जाना जाता है).