처음부터 무언가를 만드는 것에 대해 생각할 때, 멋진 가제트이든 세련된 가구이든, 두 용어를 우연히 발견 할 수 있습니다: 캐스팅 및 성형. 두 프로세스 모두 제조에 필수적입니다, 그러나 그들은 고유 한 분위기와 용도를 가지고 있습니다. 그래서, 주조와 성형의 차이점은 무엇입니까?? 다이빙합시다!
캐스팅의 기본
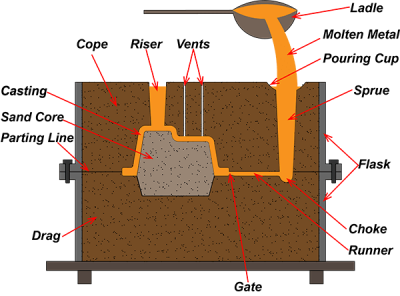
주조 공정의 유형
주조 액체 물질을 곰팡이에 붓고 굳어짐에 관한 것입니다.. 케이크를 만드는 것과 같습니다. 재료를 혼란스럽게하십시오 (또는 재료), 팬에 붓습니다 (곰팡이), 설정을 기다릴 때까지 기다립니다. 다음은 몇 가지 인기있는 캐스팅 방법입니다:
- 모래 주조: 이것은 모래가 패턴 주위에 포장되는 고전적인 방법입니다., 곰팡이 생성. 더 큰 품목에 좋고 상대적으로 저렴합니다.
- 투자 주조: 잃어버린 웨스 캐스팅에 대해 들어 본 적이 있습니다? 이 기술은 세라믹에서 코팅 된 왁스 모델을 사용합니다.. 왁스가 녹을 때, 복잡한 디자인을 위해 완벽한 곰팡이가 남아 있습니다!
- 다이 캐스팅: 이것을 패스트 푸드 버전의 캐스팅으로 생각하십시오. 용융 금속은 고압 하에서 금형에 주입됩니다., 대량 생산에 이상적.
- 원심주조: 이 프로세스는 금형을 돌립니다, 곰팡이 벽에 재료를 강제로 허용. 파이프와 원통형 모양을 만드는 것이 좋습니다.
캐스팅의 장점
캐스팅은 눈에 띄는 제조 공정으로 만드는 몇 가지 주요 이점을 자랑합니다.:
1. 복잡한 모양을 만들 수있는 능력: 캐스팅은 복잡한 디자인과 세부 사항을 생산하는 데 탁월합니다. 복잡한 지오메트리가있는 조각이 필요한 경우, 이 방법은 쉽게 처리 할 수 있습니다.
2. 재료의 다양성: 광범위한 재료를 수용합니다, 포함:
- 궤조: 알류미늄, 청동, 철, 그리고 더.
- 플라스틱: 주조 기술에 따라 다양한 유형.
- 유리: 일부 방법은 유리 캐스팅을 처리 할 수도 있습니다.
3. 다른 응용 프로그램에 대한 적응성: 작은 장식 품목 또는 대규모 기능 구성 요소가 필요한지 여부, 캐스팅은 다양한 크기와 모양을 생성하도록 조정할 수 있습니다..
4. 정밀도와 정확성: 주조 과정은 높은 정밀도를 허용합니다, 최종 제품이 원래 디자인과 밀접하게 일치하는지 확인.
5. 대규모 생산에 대한 비용 효율성: 초기 설정은 더 비쌀 수 있습니다, 많은 양의 동일한 품목을 생산할 때 캐스팅은 비용 효율적입니다..
성형의 기본
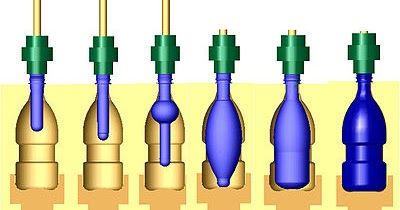
성형 공정의 유형
조형, 반면에, 재료를 특정 형태로 형성하는 것입니다. 플레이 도와 함께 제작하는 것으로 생각하십시오. 원하는대로 압박하고 모양을 만들 수 있습니다! 다음은 몇 가지 일반적인 성형 방법입니다:
- 주입 성형: 녹은 플라스틱이 곰팡이에 주입되는 곳입니다.. 컨테이너 및 장난감과 같은 일상적인 품목을 만드는 데 매우 인기가 있습니다..
- 블로우 몰딩: 이 기술은 병과 같은 중공 품목에 사용됩니다. 공기는 가열 된 플라스틱 튜브로 날아갑니다, 금형으로 확장됩니다.
- 회전 성형: 여기, 곰팡이는 분말로 채워져 회전합니다. 가열 될 때, 파우더는 곰팡이 내부를 녹이고 코팅합니다., 강력하고 중공 제품 생성.
- 열적 성형: 플라스틱 시트는 유연 할 때까지 가열됩니다, 그런 다음 곰팡이 위에 형성됩니다. 이것은 포장재와 트레이에 일반적입니다.
성형의 장점
성형은 몇 가지 중요한 이점을 제공합니다, 특히 생산 효율성 및 자원 관리 분야에서:
- 생산 속도: 성형은 다량의 동일한 제품을 빠르게 생산하는 데 탁월합니다., 대량 생산에 적합합니다.
- 일관성: 프로세스는 각 항목이 품질과 외관이 균일하도록합니다., 변동성을 줄이고 제품 신뢰성 향상.
- 재료 효율성: 성형은 일반적으로 캐스팅보다 덜 재료를 사용합니다, 돈을 절약 할뿐만 아니라 폐기물을 줄입니다.
- 비용 효율성: 재료 사용량 감소와 빠른 생산량은 전체 비용 감소로 해석됩니다., 특히 높은 볼륨을 제조 할 때.
- 환경 적 이점: 폐기물을 최소화하고 재료를보다 효율적으로 활용함으로써, 성형은보다 지속 가능한 제조 관행에 기여합니다.
주조와 성형의 주요 차이점
사용 된 재료
그래서, 재료의 주조 및 성형 차이는 무엇입니까?? 주조에는 일반적으로 금속 또는 특정 플라스틱이 포함됩니다, 성형하는 동안 주로 플라스틱을 다룹니다. 쿠키와 브라우니 중에서 선택하는 것과 같습니다.!
프로세스 개요
프로세스는 실제 차이가있는 곳입니다. 캐스팅에서, 당신은 액체를 냉각하여 고체를 형성하고 있습니다. 성형으로, 당신은 종종 재료를 가열하고 재구성하는 것입니다. 우리 모두가 사용하는 아름다운 제품을 만드는 온도의 춤입니다..
응용
캐스팅과 성형 모두 산업 전반에 걸쳐 사용됩니다. 자동차 부품에서 주방 용품에 이르기까지, 응용 프로그램은 광대합니다. 하지만, 캐스팅은 종종 무거운 부품의 이동입니다, 성형은 경량에 선호됩니다, 대량 생산 품목.
비용 비교
초기 설치 비용
곰팡이 생성으로 인해 캐스팅이 초기 설정이 더 높을 수 있습니다., 특히 복잡한 디자인의 경우. 조형, 대량 생산을 위해 설치하기 위해 종종 저렴하지만, 저용량이 적은 러닝의 경우 비용이 많이들 수 있습니다. 구독 서비스 비용을 지불하는 것과 같습니다. 더 많이 사용하면 더 많이 절약 할 수 있습니다.!
생산 비용
생산 비용 측면에서, 성형은 일반적으로 높은 볼륨으로 승리합니다. 효율적이며 덜 재료를 사용합니다. 주조, 독특한 작품에 좋습니다, 수백 개의 같은 아이템을 만들면 비싸 질 수 있습니다..
환경 고려 사항
폐기물 생성
두 프로세스 모두 폐기물을 생성합니다, 그러나 성형은 일반적으로 스크랩 재료가 적습니다. 캐스팅과 함께, 처분이 필요한 남은 금속이나 모래가있을 수 있습니다..
에너지 소비
에너지 사용은 다양합니다, ~도. 녹는 과정으로 인해 캐스팅은 에너지 집약적 일 수 있습니다, 성형은 일단 설정되면 에너지 효율성이 높을 수 있습니다. 마라톤을 실행하는 것을 스프린팅과 비교하는 것과 같습니다; 둘 다 에너지를 사용합니다, 그러나 하나는 더 많은 지구력이 필요합니다!
캐스팅 대. 조형: 선택할 방법?
각 방법의 세부 사항으로 다이빙하기 전에, 프로젝트 요구 사항을 평가하는 것이 필수적입니다. 다음 질문을 스스로에게 물어보십시오:
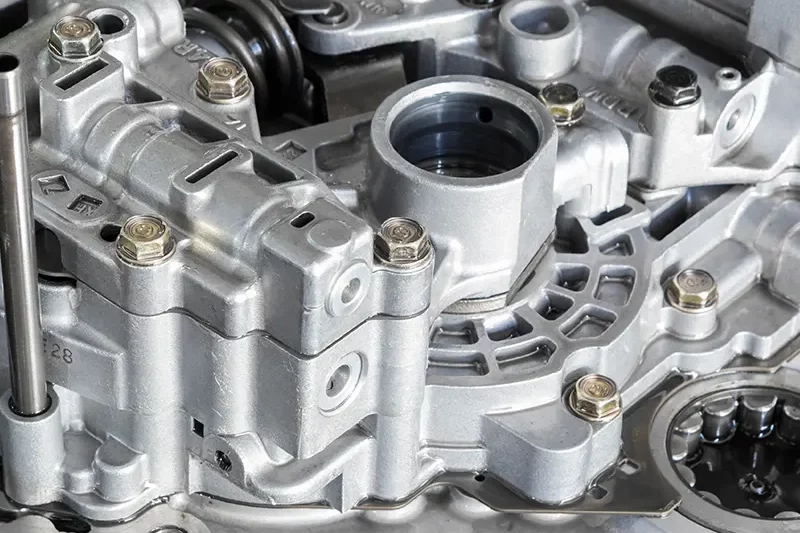
1. 어떤 자료가 필요합니까??
주조는 종종 금속과 특정 플라스틱에 선호됩니다, 성형은 일반적으로 다양한 플라스틱의 경우 더 좋습니다.. 프로젝트에 금속 구성 요소가 포함 된 경우, 캐스팅은가는 길 일 수 있습니다.
2. 원하는 모양과 세부 사항은 무엇입니까??
복잡한 디자인이나 복잡한 형상이 필요합니까?? 그렇다면, 캐스팅은 필요한 정밀도를 제공 할 수 있습니다. 성형은 더 간단한 모양에 탁월하지만 세부 사항으로 어려움을 겪을 수 있습니다..
3. 얼마나 많은 유닛이 필요합니까??
작은 배치 또는 대량 생산을 찾고 있습니까?? 성형은 다량의 양을 빠르고 일관되게 생산하는 데 탁월합니다, 대량 요구에 대한 선택으로 선택합니다.
결론
요약하면, 주조와 성형은 비슷해 보일 수 있습니다, 그들은 각각 뚜렷한 방법을 가지고 있습니다, 재료, 및 응용 프로그램. 성형과 캐스팅의 차이를 이해하면 제조에 대한 정보에 근거한 결정을 내릴 수 있습니다.. 복잡한 금속 디자인이 필요하든 대량 생산 된 플라스틱 품목, 올바른 프로세스를 아는 것은 모든 차이를 만들 수 있습니다.
자주 묻는 질문
1. 캐스팅에 일반적으로 사용되는 재료?
캐스팅에는 종종 알루미늄과 같은 금속이 포함됩니다, 철, 그리고 청동, 그러나 일부 플라스틱과 유리도 캐스트 될 수 있습니다.
2. 주조 과정은 일반적으로 얼마나 걸립니까??
시간은 방법에 따라 크게 다를 수 있습니다, 그러나 일반적으로 냉각 시간으로 인해 성형보다 시간이 오래 걸립니다..
3. 성형의 한계는 무엇입니까??
성형은 복잡한 디자인에 덜 효과적 일 수 있으며 일반적으로 플라스틱과 같은 특정 재료로 제한됩니다..
4. 주조 및 성형을 상호 교환 적으로 사용할 수 있습니다?
좀 빠지는. 프로세스와 응용 프로그램이 다릅니다, 따라서 특정 요구에 따라 선택하는 것이 중요합니다..
5. 주로 캐스팅 및 성형을 사용하는 산업?