Вы боретесь с нестабильным качеством, медленное производство, или высокие затраты на литье алюминия под давлением? Эти проблемы могут серьезно повлиять на успех вашего проекта..
Бянь Литье под давлением, с более чем десятилетним опытом работы в Фошане, Китай, специализируется на решении этих задач. Наши передовые конструкции пресс-форм и эффективные методы производства предназначены для повышения точности., ускорить производство, и сократить расходы.
Можем ли мы изменить ситуацию для вас?? Узнайте, как Bian Diecast может помочь решить ваши проблемы с кастингом и вывести ваши проекты на новый уровень..
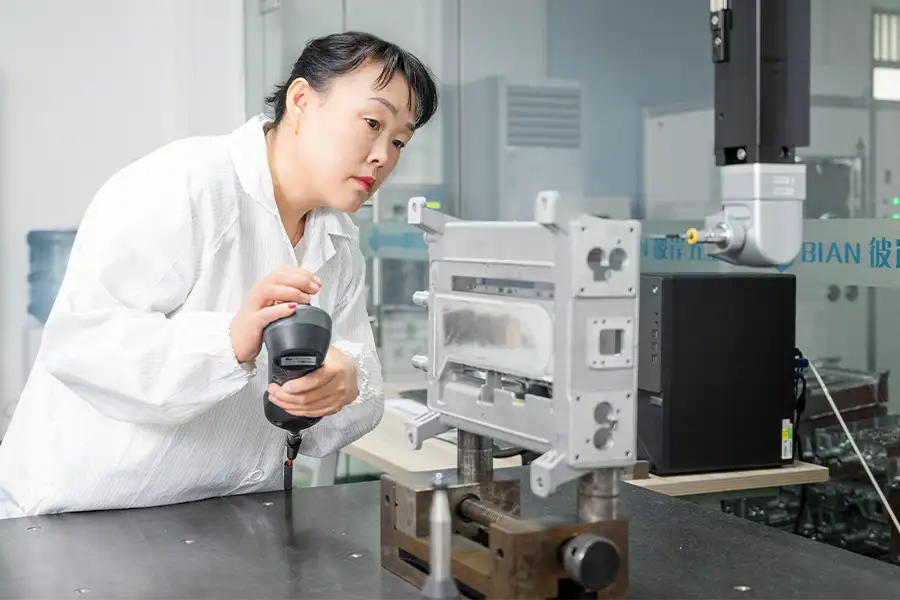
Что такое литье алюминия под высоким давлением?
Литье алюминия под давлением это процесс изготовления металлических деталей. Существует шесть основных этапов изготовления отлитой под давлением детали или компонента.:
- Дизайн пресс-формы
- Подготовка к литью
- Инъекция
- Охлаждение и затвердевание
- Демонтаж/удаление
- Механическая обработка с ЧПУ/обработка поверхности
Первый, готовим стальную форму по форме нужной детали. Затем, алюминий нагревается до жидкого состояния и впрыскивается в форму.
Мы используем высокое давление впрыска, чтобы гарантировать, что алюминий заполнит каждую деталь формы.. Алюминий быстро охлаждается и затвердевает внутри формы..
После охлаждения, форма открыта, и алюминиевая часть снимается. Следующий, обрезаем лишний алюминий и проверяем качество детали.
Окончательно, При необходимости могут быть применены дополнительные обработки, такие как покраска или покрытие.. Весь этот процесс эффективно производит детали сложной формы и высокой точности..
Проще говоря, Литье алюминия под давлением — это метод изготовления металлических деталей путем впрыскивания расплавленных алюминиевых сплавов в стальные формы..
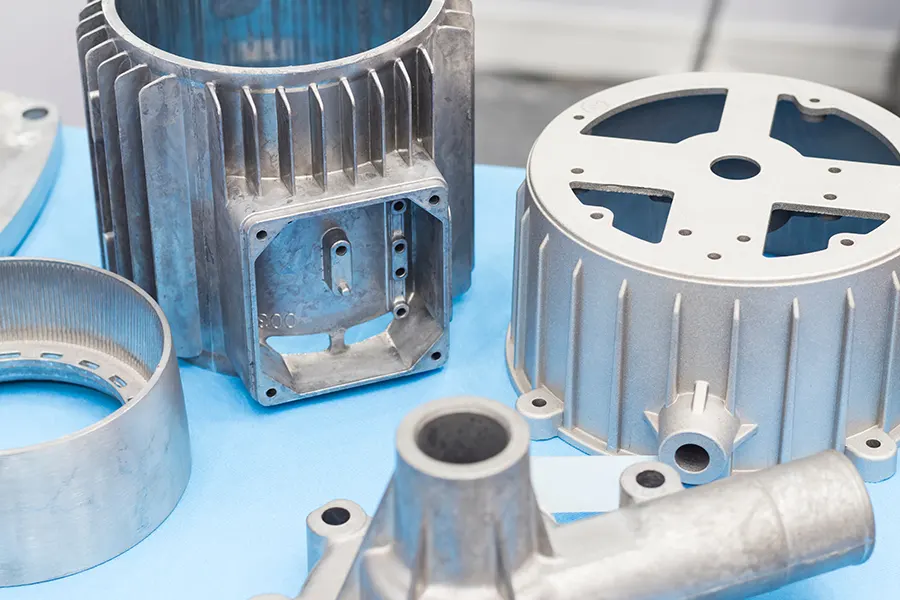
Значение конструкции пресс-формы при литье алюминия под давлением
Каждый шаг важен, но важность конструкции формы для литья под давлением алюминия невозможно переоценить. Потому что это напрямую влияет на качество., эффективность производства, и стоимость литых алюминиевых деталей.
Хорошо спроектированная форма обеспечивает точные и гладкие детали, равномерно заполняя каждую деталь.. Плохая конструкция может привести к появлению дефектов, таких как пузыри и неравномерное наполнение..
Оптимизация конструкции пресс-формы повышает эффективность производства за счет усовершенствования систем литников и охлаждения., сокращение времени цикла, и минимизация дефектов. Это также продлевает срок службы формы., сокращение расходов на техническое обслуживание.
В итоге, Хорошая конструкция пресс-формы обеспечивает высокое качество деталей и эффективное производство., что делает его необходимым для успешного литья алюминия под давлением.
История проектирования пресс-форм для литья под давлением алюминия
История проектирования форм для литья под давлением алюминия показывает, как технологии развивались с течением времени..
Это началось с основные формы из песка и камня, используемые в древние времена. Во время промышленной революции, конструкция пресс-форм улучшена за счет механизированного производства и использования более прочных материалов, таких как сталь. В начале 20 века, компьютерное проектирование (САПР) программное обеспечение произвело революцию в этой области, делает проектирование пресс-форм намного более точным и эффективным. Сегодня, При проектировании пресс-форм используются передовые методы моделирования и 3D-печать для доработки и тестирования прототипов.. Заглядывая в будущее, новые технологии, такие как Интернет вещей (Интернет вещей) и искусственный интеллект (ИИ) призваны способствовать дальнейшему повышению точности и эффективности.
Общий, эти достижения значительно улучшили производственные процессы и качество продукции..
Как оптимизировать процесс проектирования алюминиевой формы для литья под давлением
Оптимизировать процесс проектирования пресс-форм для литья под давлением алюминия., вы можете сосредоточиться на улучшении нескольких ключевых областей:
1. Понять требования:
Текущий подход: Обычно, выполнен базовый анализ требований.
Оптимизация: Начните с детального анализа и заранее соберите всю необходимую информацию.. Используйте 3D-моделирование и симуляцию, чтобы проверить свои идеи и выявить проблемы, прежде чем приступить к реальному производству..
2. Этап проектирования:
Текущий подход: Дизайны создаются и проверяются вручную..
Оптимизация: Используйте программное обеспечение CAD и CAE для проектирования и тестирования пресс-форм.. Смоделируйте, как пресс-форма будет работать с различными настройками литников и охлаждения, чтобы заранее устранить потенциальные проблемы..
3. Производство:
Текущий подход: Формы часто изготавливаются ручными методами., который может потребовать нескольких настроек.
Оптимизация: Переход на станки с ЧПУ для точного изготовления пресс-форм. Рассмотрите возможность использования 3D-печати для прототипов, чтобы быстро протестировать и усовершенствовать конструкции перед окончательным производством..
4. Тестирование и проверка:
Текущий подход: Пробные запуски используются для проверки и настройки пресс-форм..
Оптимизация: Проводите больше виртуальных испытаний на этапе проектирования, чтобы сократить количество физических испытаний.. Тщательно проверьте работоспособность пресс-формы с помощью испытаний под давлением и охлаждением, чтобы убедиться, что она соответствует стандартам..
5. Производство и обслуживание:
Текущий подход: Следуйте стандартным процедурам технического обслуживания.
Оптимизация: Создайте подробный график технического обслуживания и используйте датчики для мониторинга состояния пресс-формы в режиме реального времени.. Анализируйте данные, чтобы спрогнозировать, когда потребуется техническое обслуживание., минимизация времени простоя и продление срока службы пресс-формы.
Сосредоточив внимание на этих шагах, вы можете сделать процесс проектирования пресс-формы более точным, эффективный, и экономически эффективный, что приводит к повышению качества продукции и более бесперебойному производству.
Особенности проектирования пресс-форм для литья алюминия под давлением
При проектировании алюминиевых экструзионных форм, управление дизайном пресс-формы включает в себя несколько важных соображений для обеспечения оптимальной производительности и качества.. Вот разбивка ключевых факторов:
Определение требований
Прежде всего, крайне важно определить размеры изделия, допуски, и требования к производительности. Четко указав эти параметры, вы гарантируете, что пресс-форма будет эффективно отвечать требованиям конечного использования.
Выбор материала
Следующий, выбор материала жизненно важно, что означает выбор подходящего алюминиевого сплава. Выбор сплава влияет на процесс экструзии и прочность конечного продукта., коррозионная стойкость, и теплопроводность. Таким образом, важно выбрать материал, который соответствует потребностям продукта.
Дизайн штампа
Дизайн профиля
Переходим к дизайну штампов, создать профиль, соответствующий желаемой форме поперечного сечения экструзии. Это гарантирует плавное и равномерное прохождение материала через матрицу..
Система охлаждения
Кроме того, интегрировать эффективную систему охлаждения. Правильное охлаждение помогает поддерживать температуру матрицы., обеспечение стабильного качества продукции и точных размеров.
Размер заготовки и температура
Более того, выбрать подходящий размер заготовки и температуру для процесса экструзии. Этот выбор имеет решающее значение для достижения равномерного потока материала и оптимальных свойств экструзии..
Анализ потока
Впоследствии, провести анализ потока, чтобы предсказать, как расплавленный алюминий будет вести себя во время экструзии. Этот анализ помогает выявить потенциальные проблемы., например, блокировка матрицы или неравномерный поток, возможность внесения необходимых корректировок в конструкцию.
Вентиляция
Более того, включить достаточную вентиляцию в конструкцию формы. Правильная вентиляция необходима для выпуска газов и предотвращения дефектов, таких как пустоты или включения., обеспечение плавного прохождения материала через матрицу.
Оснастка и производство
Кроме того, убедиться, что конструкция пресс-формы пригодна для производства. Учитывайте возможности вашего инструментального оборудования и точность, необходимую для функций штампа, чтобы избежать каких-либо производственных проблем..
Прототип и тестирование
Как только дизайн будет завершен, создать прототип матрицы и провести пробную экструзию. Тестирование — важнейший шаг для оценки производительности матрицы и выявления любых конструктивных недостатков перед началом полномасштабного производства..
Обслуживание и долговечность
Окончательно, спроектируйте форму с учетом технического обслуживания. Включает функции, облегчающие чистку и замену деталей., и выбирайте прочные материалы, которые могут выдерживать высокое давление и температуру процесса экструзии..
Bian Diecast и конструкция алюминиевых форм для литья под давлением
Bian Diecast - это ведущая компания по литью алюминия под давлением базируется в районе Наньхай, Фошань город, Китай. Более десяти лет в отрасли, мы предоставляем первоклассные услуги, включая проектирование пресс-форм, литье под давлением, обработка с ЧПУ, и отделка поверхности.
Наше современное оборудование и квалифицированная команда нацелены на предоставление высококачественных решений для различных отраслей промышленности., например, автомобильный, осветительные приборы, электроника, мебель, и строительство.
Проектирование пресс-форм для литья под давлением алюминия в компании Bian Diecast ориентировано на создание практичных и экономичных форм.. Мы используем наш превосходный дизайн для обеспечения технологичности (ДФМ) методы, гарантирующие, что наши формы соответствуют точной форме вашей детали и работают эффективно.
- Что такое ДФМ?
ДФМ, или Проектирование для производства, это концепция, используемая в инженерии и дизайне продукции.. Это означает разработку продукта таким образом, чтобы его производство было проще и дешевле.. Так, DFM предполагает создание дизайна продукта с учетом того, как продукт будет производиться..
В целях оптимизации процесса производства алюминиевых отливок под давлением, будут поставлены следующие цели:
- Конструкция, позволяющая использовать наименьшее количество необходимого алюминия..
- Убедитесь, что детали выходят из штампа плавно..
- Оптимизируйте охлаждение, чтобы ускорить процесс затвердевания..
- Создавайте детали, требующие минимальной обработки после литья..
- Убедитесь, что конечный продукт работает так, как необходимо при его применении..
Заключение
Литье алюминия под давлением – это создание точных металлических деталей., и правильная конструкция пресс-формы имеет решающее значение. Хорошая конструкция пресс-формы повышает точность, ускоряет производство, и сокращает расходы.
В Bian Diecast, у нас более десяти лет опыта в изготовлении высококачественных форм и услуг по литью. Наши передовые инструменты и методы гарантируют идеальное качество ваших деталей..
Хотите улучшить процесс кастинга? Обратитесь к Bian Diecast сегодня и узнайте, как мы можем помочь воплотить ваши идеи в жизнь!