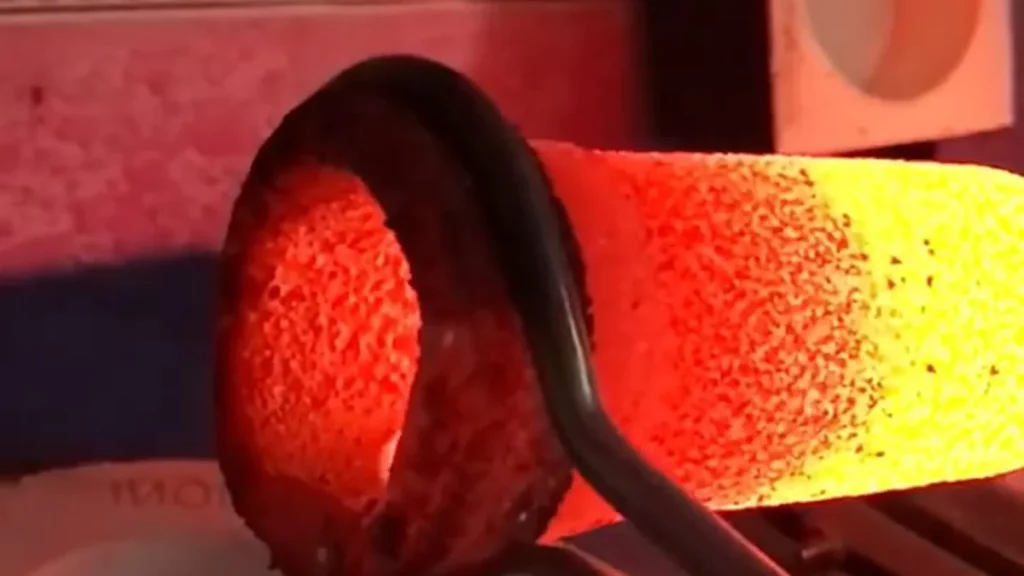
Fuente de imagen: pexels
Fundición a presión de aluminio y fundición en arena., Cada método da forma a nuestro mundo de maneras únicas., desde los coches que conducimos hasta los dispositivos sin los que no podemos vivir.
Pero, ¿qué diferencia a estos procesos?? ¿Por qué elegir uno sobre el otro??
en esta publicación, Nos sumergiremos en el núcleo fundido de la fundición a presión vs.. moldeo en arena. Exploraremos sus fortalezas, debilidades, y las industrias que han revolucionado. Si eres ingeniero, dueño de un negocio, o simplemente curiosidad por saber cómo se hacen las cosas, Esta comparación arrojará luz sobre el arte oculto en los objetos cotidianos..
Descripción general de los métodos de fundición
Fundición a presión de aluminio
Descripción del proceso
- El metal fundido se introduce en moldes de acero reutilizables bajo alta presión..
- los moldes, conocido como muere, están diseñados para crear formas intrincadas de forma precisa y consistente.
- Las piezas producidas tienen características bien definidas y pueden exhibir superficies lisas o texturizadas..
Materiales usados
- Aluminio: Comúnmente utilizado debido a su peso ligero y excelentes propiedades térmicas..
- Otras aleaciones: Zinc, magnesio, y las aleaciones a base de cobre también se utilizan para aplicaciones específicas..
Ventajas
- Precisión: Ofrece alta precisión dimensional y repetibilidad para piezas complejas..
- Acabado de la superficie: Proporciona una gama de acabados atractivos adecuados para diversas industrias..
- Eficiencia: Permite la producción de piezas con requisitos mínimos de posprocesamiento..
Desventajas
- Costo inicial: Requiere inversión en herramientas y configuración para la creación de matrices..
- Tamaño limitado: No es ideal para piezas grandes debido a limitaciones del molde..
Moldeo en arena
Descripción del proceso
- Implica verter metal fundido directamente en moldes de arena sin alta presión..
- Permite la creación de formas netas dentro de un nivel de tolerancia de un cuarto de pulgada..
- Ofrece versatilidad en la producción de piezas con diferentes complejidades..
Materiales usados
- Moldes de arena: Moldes rentables que se adaptan a una amplia gama de tamaños y formas de piezas.
- Aleaciones de metales: Adecuado para fundir una variedad de metales como el hierro., acero, aluminio, y bronce.
Ventajas
- Versatilidad: Se adapta a piezas más grandes con más flexibilidad en los cambios de diseño..
- Herramientas rentables: Requiere menos inversión inicial en comparación con los métodos de fundición a presión..
Desventajas
- Acabado de la superficie: Da como resultado texturas más rugosas en comparación con los acabados de fundición a presión..
- Precisión dimensional: Puede requerir procesos posteriores a la fundición adicionales para ajustes de precisión..
Comparación detallada
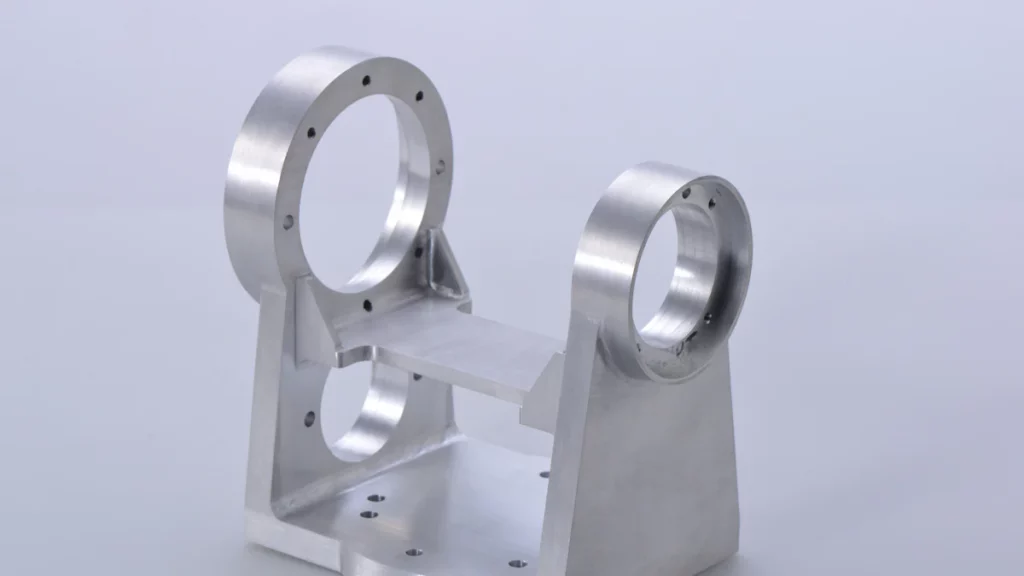
Fuente de imagen: desempaquetar
Velocidad y volumen de producción
Velocidad de fundición a presión de aluminio vs.. velocidad de fundición en arena
- La fundición a presión de aluminio destaca por su rápida producción, logrando altas velocidades debido a sus procesos automatizados.
- Moldeo en arena, aunque versatil, opera a un ritmo más lento ya que implica trabajo manual en diseño de molde.
Idoneidad para diferentes volúmenes de producción.
- Fundición a presión de aluminio:
- Ideal para tiradas de producción de gran volumen que requieren exactitud dimensional precisa.
- Adecuado para componentes con diseños complejos y exigencias de calidad consistentes.
- Moldeo en arena:
- Más adecuado para volúmenes de producción bajos a medianos de piezas más grandes..
- Ofrece flexibilidad para adaptarse a diferentes tamaños de piezas sin ajustes significativos de herramientas..
Complejidad y tamaño de la pieza
Capacidades y limitaciones de cada método.
- Fundición a presión de aluminio: Destaca en la producción de formas complejas con tolerancias estrictas sin la necesidad de un extenso mecanizado posterior a la fundición..
- Moldeo en arena: Más adecuado para componentes grandes con requisitos de precisión menos estrictos, permitiendo variaciones de diseño más indulgentes.
Tamaños de piezas típicos para fundición a presión y fundición en arena.
- fundición a presión: Se especializa en piezas de tamaño pequeño a mediano que exigen precisión y paredes delgadas..
- Moldeo en arena: Acomoda piezas más grandes con paredes más gruesas, ideal para aplicaciones que priorizan la rentabilidad sobre la precisión dimensional.
Acabado superficial y precisión dimensional
Tolerancias alcanzables
- Fundición a presión de aluminio:
- Mantiene tolerancias estrechas incluso en geometrías intrincadas., reduciendo la necesidad de operaciones secundarias.
- Moldeo en arena:
- Las tolerancias son generalmente más flexibles debido a la naturaleza del proceso., a menudo requieren pasos de acabado adicionales para ajustes de precisión.
Comparaciones de calidad de superficie
- Las piezas fundidas a presión presentan acabados más suaves con detalles más finos en comparación con las piezas fundidas en arena conocidas por sus texturas más rugosas..
Opciones de materiales
Aleaciones adecuadas para fundición a presión.
- Aluminio: Ampliamente utilizado en fundición a presión por sus propiedades livianas y excelente conductividad térmica..
- Zinc: Ideal para piezas complejas debido a su bajo punto de fusión y alta ductilidad..
- Magnesio: Ofrece una excepcional relación resistencia-peso., adecuado para componentes ligeros.
- Aleaciones a base de cobre: Proporcionan mayor resistencia a la corrosión y conductividad térmica..
Aleaciones adecuadas para fundición en arena.
- Hierro: Comúnmente utilizado en fundición en arena por su rentabilidad y maquinabilidad..
- Acero: Ofrece versatilidad en la producción de una amplia gama de tamaños de piezas con diferentes complejidades..
- Aluminio: Adecuado para fundición en arena debido a su bajo punto de fusión y buena fluidez..
- Bronce: Proporciona una excelente resistencia al desgaste, haciéndolo ideal para aplicaciones que requieren durabilidad.
Costos de herramientas y configuración
Inversión inicial para troqueles vs.. moldes de arena
- fundición a presión:
- Requiere una importante inversión inicial en moldes de acero adaptados a diseños de piezas específicos.
- Los costos iniciales de herramientas pueden ser más altos, pero compensados por los beneficios a largo plazo de la producción en masa..
- Moldeo en arena:
- Implica costos iniciales más bajos ya que los moldes de arena son más asequibles que los troqueles de acero..
- Se minimizan los gastos de herramientas., lo que lo convierte en una opción rentable para tiradas de producción más pequeñas.
Consideraciones de costos a largo plazo
- fundición a presión:
- Ahorros a largo plazo obtenidos gracias a capacidades de producción de gran volumen y un desperdicio mínimo de material..
- Los requisitos de mecanizado reducidos contribuyen a la rentabilidad general en ciclos de producción extendidos..
- Moldeo en arena:
- Ofrece soluciones económicas para volúmenes de producción bajos a medianos con menos costos de mantenimiento de herramientas..
- La flexibilidad en los cambios de diseño reduce los gastos adicionales asociados con la modificación de las configuraciones del molde..
Flexibilidad de diseño
Capacidad para realizar cambios de diseño.
- La fundición a presión permite modificaciones complejas del diseño sin necesidad de realizar ajustes extensos en las herramientas., Garantizar una rápida adaptabilidad a los requisitos cambiantes..
- La fundición en arena proporciona flexibilidad para alterar las geometrías de las piezas durante el proceso de fabricación del molde., acomodar variaciones de diseño de manera eficiente.
Capacidades de creación de prototipos
- fundición a presión:
- Permite la creación rápida de prototipos de piezas complejas con precisión dimensional precisa., facilitar fases de prueba eficientes.
- Moldeo en arena:
- Admite el desarrollo de prototipos de componentes más grandes con diversas geometrías, permitiendo mejoras iterativas en el diseño.
Espesor de pared
Espesor mínimo alcanzable para cada método
En fundición a presión de aluminio, El espesor mínimo de la pared puede alcanzar tan solo 1 mm., permitiendo diseños intrincados con detalles precisos. Este método destaca en la producción de piezas de paredes delgadas que mantienen la integridad estructural.. Por otro lado, La fundición en arena generalmente requiere paredes más gruesas., con un espesor mínimo de alrededor de 3 mm debido a la naturaleza del proceso. El mayor espesor de pared en la fundición en arena proporciona más flexibilidad durante la producción y permite un proceso posterior a la fundición indulgente para corregir cualquier imprecisión de manera eficiente..
Implicaciones para el peso y la resistencia de la pieza.
Al considerar la fundición a presión de aluminio frente a la fundición en arena, El espesor de la pared impacta directamente en el peso y la resistencia de las piezas finales.. Las paredes más delgadas logradas mediante la fundición a presión de aluminio dan como resultado componentes más livianos sin comprometer la durabilidad.. A diferencia de, Las piezas fundidas en arena con paredes más gruesas tienden a ser más pesadas pero ofrecen mayor resistencia., haciéndolos adecuados para aplicaciones que requieren estructuras robustas.
Requisitos de posprocesamiento
Necesidades de acabado para piezas fundidas a presión.
Las piezas de fundición a presión de aluminio a menudo requieren un posprocesamiento mínimo debido a su alta precisión dimensional y acabados superficiales suaves.. Sin embargo, Es posible que se necesiten algunos toques finales para mejorar la estética o la funcionalidad.. Las técnicas comunes de posprocesamiento incluyen el desbarbado., granallado, y recubrimiento en polvo para refinar la apariencia y el rendimiento de los componentes fundidos a presión.
Necesidades de acabado para piezas fundidas en arena.
En fundición de arena, El posprocesamiento juega un papel crucial en el refinamiento de las texturas rugosas inherentes a este método.. Las piezas fundidas en arena suelen someterse a extensos procesos de acabado, como el rectificado., lijado, o mecanizado para lograr las cualidades superficiales y precisiones dimensionales deseadas. También se pueden aplicar tratamientos adicionales como pintura o enchapado para mejorar el aspecto general y la funcionalidad de los componentes moldeados en arena..
Consideraciones ambientales
Eficiencia energética
Al comparar la fundición a presión de aluminio con la fundición en arena desde una perspectiva medioambiental, La eficiencia energética es un factor clave.. La fundición a presión de aluminio implica fundir metal a altas temperaturas utilizando importantes recursos energéticos.. A diferencia de, La fundición en arena consume menos energía ya que no requiere procesos de calentamiento intensos.. El menor consumo de energía en la fundición en arena contribuye a reducir el impacto ambiental y los costos operativos..
Desperdicio de materiales y reciclabilidad
Tanto la fundición a presión de aluminio como la fundición en arena generan materiales de desecho durante la producción.; sin embargo, su reciclabilidad difiere significativamente. Los desechos de fundición se pueden reciclar fácilmente para convertirlos en nuevos componentes sin comprometer la calidad o el rendimiento.. Por otro lado, Los moldes de arena utilizados en la fundición en arena tienen una reciclabilidad limitada debido a problemas de contaminación por exposición al metal fundido.. Las prácticas adecuadas de gestión de residuos son esenciales para minimizar el impacto ambiental y maximizar la eficiencia de los recursos..
Aplicaciones e idoneidad
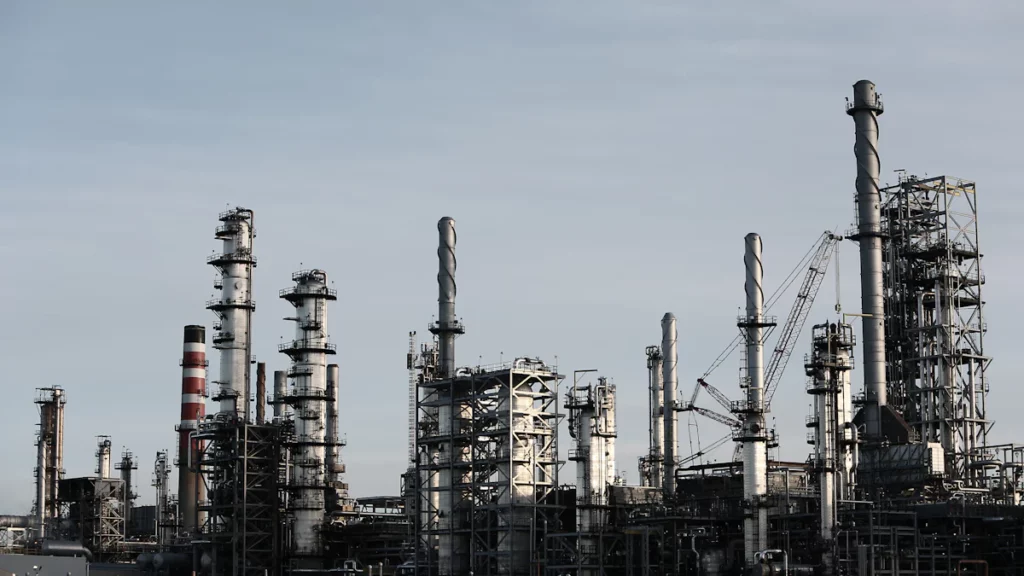
Fuente de imagen: pexels
Fundición a presión de aluminio
Aplicaciones ideales
- Fabricación de componentes complejos con geometrías precisas.
- Producir piezas ligeras con excelentes propiedades térmicas.
- Creación de prototipos automotrices de alta calidad para pruebas y validación..
Idoneidad para piezas de precisión
- Garantizar la precisión dimensional en componentes críticos.
- Lograr estándares de calidad consistentes para aplicaciones aeroespaciales.
- Proporcionando soluciones confiables para la fabricación de equipos médicos..
Moldeo en arena
Aplicaciones ideales
- Fabricación de componentes de maquinaria industrial a gran escala..
- Elaboración de esculturas artísticas y piezas ornamentales..
- Desarrollar elementos arquitectónicos rentables para proyectos de construcción..
Idoneidad para piezas grandes
- Abastecimiento a la producción de piezas de motores marinos de gran tamaño..
- Construcción de componentes duraderos para equipos agrícolas..
- Construcción de elementos estructurales para proyectos de desarrollo de infraestructura..
El estudio sobre Fabricación Aditiva para Fundición Rápida en Arena destaca la investigación mecánica y microestructural de prototipos automotrices de aleación de aluminio, enfatizando la importancia de mantener los niveles de ductilidad durante las fases de creación de prototipos para mejorar las propiedades de los componentes de manera efectiva. Los esfuerzos de investigación futuros tienen como objetivo optimizar aún más los procesos de fabricación y al mismo tiempo mejorar las características mecánicas para satisfacer las demandas cambiantes de la industria de manera eficiente. (Rieles, 2024).
Conclusión
Al comparar la fundición a presión de aluminio y la fundición en arena, las diferencias clave residen en la velocidad de producción, complejidad de la pieza, y opciones de materiales. La fundición a presión de aluminio destaca por su precisión y acabado superficial, ideal para componentes complejos. Por otro lado, La fundición en arena ofrece versatilidad para piezas más grandes con herramientas rentables.. Según las necesidades de su aplicación, elija fundición a presión para geometrías precisas y fundición en arena para componentes de gran escala. Considere la importancia histórica de los orígenes de la fundición en arena en la antigua China y los rápidos avances en la fabricación aditiva de prototipos de aluminio para tomar una decisión informada sobre el método de fundición correcto..