La fundición a presión es un proceso fascinante que desempeña un papel fundamental en la fabricación moderna.. Es como la columna vertebral de la industria., asegurándose silenciosamente de que todo, desde piezas de automóviles hasta productos electrónicos, esté a la altura. ¿Alguna vez te has preguntado cómo pueden crear tantas piezas complejas tan rápido?? Bien, La fundición a presión es la salsa secreta.. Profundicemos en los aspectos prácticos de esta técnica y sopesemos las ventajas y desventajas de la fundición a presión..
¿Qué es la fundición a presión??
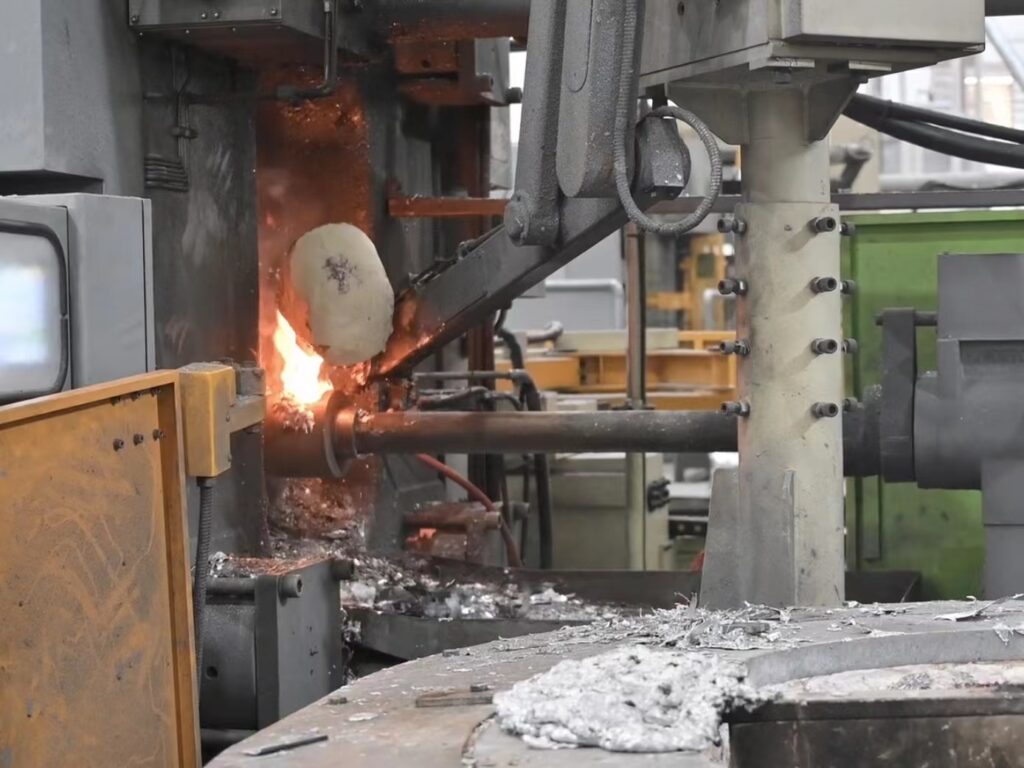
La fundición a presión es un proceso de fabricación que implica forzar el metal fundido dentro de una cavidad del molde bajo alta presión.. Piense en ello como inyectar un metal líquido caliente en un cortador de galletas, pero para piezas industriales.. Este método es conocido por producir formas complejas con una precisión notable..
Tipos de fundición a presión
La fundición a presión viene en dos versiones principales.: camara caliente y camara fria. En fundición a presión en cámara caliente, El metal se funde en una cámara conectada al molde.. Es rápido e ideal para metales con puntos de fusión bajos como el zinc.. Fundición a presión en cámara fría, por otro lado, Implica fundir el metal por separado antes de transferirlo a la cámara.. Esta es su opción para metales como el aluminio que tienen puntos de fusión más altos..
Ventajas de la fundición a presión
La fundición a presión no es popular sin motivo alguno. Tiene un gran impacto con una gran cantidad de beneficios que lo convierten en un método de referencia en diversas industrias..
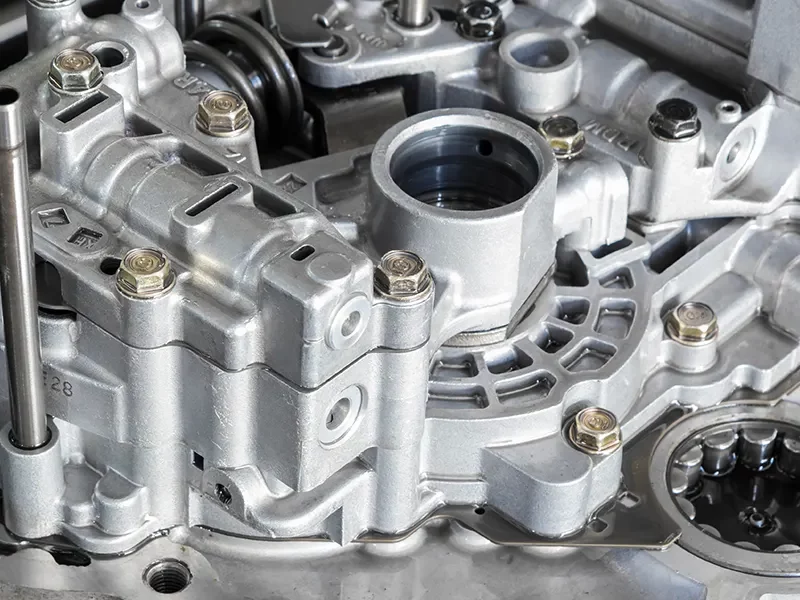
Alta eficiencia y productividad
Una de las mayores ventajas de fundición a presión es lo rápido y eficiente que es. Los ciclos de producción son rápidos., produciendo piezas a un ritmo impresionante. Más, con la configuración correcta, Puedes automatizar gran parte del proceso., lo que significa que obtienes resultados consistentes sin mucho trabajo manual.
Calidad y precisión superiores
La fundición a presión es como el artista de precisión de la fabricación.. Puede lograr tolerancias estrictas y detalles complejos que serían difíciles de replicar con otros métodos.. La precisión dimensional es de primer nivel., y obtienes un acabado superficial suave nada más sacarlo del molde, reduciendo la necesidad de posprocesamiento.
Versatilidad en el diseño
Tengo un diseño complejo en mente? La fundición a presión probablemente pueda manejarlo.. Este proceso destaca en la creación de piezas con geometrías intrincadas y paredes delgadas.. Es como tener una varita mágica que convierte tus planos detallados en realidad sin sudar..
Ahorro de materiales y reducción de residuos
En el mundo del die-casting, no desperdicies, no quiero. El proceso es eficiente con los materiales., produciendo un mínimo de chatarra. Y cualquier chatarra que se genere a menudo se puede reciclar., lo que lo convierte en una opción más sostenible en comparación con otros métodos de fabricación.
Desventajas de la fundición a presión
Por supuesto, ningún método es perfecto, y la fundición a presión tiene sus inconvenientes que debes considerar.
Alto costo inicial
La configuración para la fundición a presión puede ser costosa. Los troqueles y el equipo no son baratos., y necesitarás producir una cantidad significativa de piezas para que sea económicamente viable. Esta alta inversión inicial puede ser una barrera para las operaciones a pequeña escala..
Limitaciones de materiales
Si bien la fundición a presión es versátil, no es una solución única para todos. Estás algo limitado por los metales que puedes usar.. Generalmente, Es más adecuado para metales no ferrosos como el aluminio., zinc, y magnesio. Si necesitas piezas fabricadas en acero o hierro, tendrás que buscar en otra parte.
Complejidad y mantenimiento
La naturaleza compleja de la fundición a presión significa que las herramientas y los troqueles pueden desgastarse con el tiempo., que requiere un mantenimiento regular. Este mantenimiento es crucial para mantener la precisión y calidad de las piezas., pero puede aumentar el costo general y la complejidad de la operación..
Limitaciones de tamaño
La fundición a presión es fantástica para piezas pequeñas y medianas., pero no es ideal para componentes más grandes. El tamaño y el peso de las piezas que puede producir están limitados por la capacidad de la máquina de fundición a presión y los moldes..
Aplicaciones de la fundición a presión
Dada su variedad de beneficios, No sorprende que la fundición a presión llegue a numerosas industrias..
Industria automotriz
La fundición a presión es un caballo de batalla en el sector automoción, produciendo de todo, desde bloques de motor hasta carcasas de transmisión. Su capacidad para crear duraderos, Las piezas livianas lo hacen invaluable para mejorar la eficiencia del combustible y el rendimiento..
Electrónica de Consumo
¿Alguna vez te has preguntado cómo tus dispositivos se mantienen tan elegantes y compactos?? La fundición a presión es un actor clave aquí, Elaboración de componentes que sean ligeros y resistentes., perfecto para los últimos teléfonos inteligentes, portátiles, y otros dispositivos electronicos.
Aeroespacial y Defensa
En industrias donde la precisión y la confiabilidad son primordiales, La fundición a presión brilla. Se utiliza para fabricar componentes que pueden soportar condiciones extremas., haciéndolo ideal para aplicaciones aeroespaciales y de defensa.
Electrodomésticos
Desde utensilios de cocina hasta herramientas eléctricas, La fundición a presión está detrás de escena., Garantizar que estos productos sean robustos y fiables.. La capacidad de producir piezas con formas complejas significa que los diseñadores tienen la libertad de innovar sin verse frenados por las limitaciones de fabricación..
Fundición a presión vs.. Otros métodos de fundición
Al decidir sobre un método de fundición, Es crucial comprender las distinciones entre la fundición a presión y otras técnicas comunes.. Cada método tiene sus propias fortalezas y debilidades., haciéndolos adecuados para diferentes aplicaciones.
Fundición a presión vs.. Moldeo en arena
Moldeo en arena, una de las técnicas de fundición más antiguas, crea moldes a partir de arena y se compara con la fundición a presión de la siguiente manera:
- La fundición a presión ofrece una precisión dimensional superior y un acabado superficial más suave., mientras que la fundición en arena a menudo requiere mecanizado adicional.
- La fundición a presión es más rápida debido a su inyección a alta presión., a diferencia del proceso más lento del molde de arena.
- La fundición en arena maneja una variedad más amplia de metales., incluyendo aleaciones ferrosas, Mientras que la fundición a presión se limita a metales no ferrosos como el aluminio., zinc, y magnesio.
- Aunque la fundición a presión tiene costos de instalación iniciales más altos, Se vuelve más rentable para grandes tiradas de producción., mientras que la fundición en arena es más adecuada para lotes más pequeños o componentes más grandes debido a su menor inversión inicial.
Fundición a presión vs.. Fundición a la cera perdida
Fundición a la cera perdida, o fundición a la cera perdida, crea un molde a partir de un modelo de cera recubierto con cerámica. En comparación con la fundición a presión:
- La fundición a la cera perdida puede lograr detalles más finos y diseños más complejos., haciéndolo ideal para geometrías complejas.
- La fundición a presión suele ofrecer un acabado superficial más suave., mientras que la fundición a la cera perdida a menudo necesita un acabado adicional.
- La fundición a presión es más eficiente para la producción de gran volumen con tiempos de ciclo rápidos, Mientras que la fundición a la cera perdida es más lenta y mejor para volúmenes bajos y medios..
- La fundición a la cera perdida es más versátil con una gama más amplia de metales., incluyendo aleaciones de alto punto de fusión como el acero inoxidable, mientras que la fundición a presión se limita a metales no ferrosos.
Cómo elegir un fabricante de fundición a presión
Seleccionando el fabricación de fundición a presión adecuadar es crucial para garantizar la calidad y eficiencia de su producción.. Aquí hay algunos factores clave y preguntas que guiarán su decisión..
- Experiencia y conocimientos: Busque fabricantes con una trayectoria comprobada en fundición a presión, particularmente con experiencia en la producción de piezas similares a la suya. Su experiencia puede afectar significativamente la calidad y confiabilidad del producto final..
- Capacidades y tecnología: Evaluar las capacidades de producción del fabricante., incluyendo los tipos de metales que pueden fundir, el tamaño y la complejidad de las piezas que pueden manejar, y las tecnologías que utilizan. Moderno, Un equipo bien mantenido y tecnologías avanzadas pueden mejorar la eficiencia y la calidad..
- Seguro de calidad: Garantizar que el fabricante cuente con procesos sólidos de control de calidad.. Certificaciones como ISO 9001 Puede indicar un compromiso de mantener altos estándares.. Pregunte sobre sus métodos de inspección y cómo manejan los defectos e inconsistencias..
- Plazos de entrega y flexibilidad: Considere los plazos de entrega del fabricante y su capacidad para adaptarse a los cambios en los programas de producción.. Un fabricante fiable debería poder cumplir sus plazos y adaptarse a sus necesidades sin comprometer la calidad..
- Costo y valor: Si bien el costo es un factor importante, es importante equilibrarlo con el valor ofrecido. Evaluar el paquete general, incluyendo calidad, servicio, y apoyo, en lugar de solo el precio por unidad.
Conclusión
La fundición a presión es una potencia en el mundo de la fabricación., ofreciendo una combinación única de eficiencia, precisión, y versatilidad. Si bien conlleva algunos desafíos, los beneficios a menudo superan los inconvenientes, especialmente en escenarios de producción de alto volumen. A medida que avanza la tecnología, El futuro de la fundición a presión parece más brillante que nunca., prometiendo aún más innovaciones y mejoras.
Preguntas frecuentes sobre fundición a presión
1. ¿Cuál es la vida útil de un molde de fundición a presión??
La vida útil de un molde de fundición a presión puede variar significativamente dependiendo de factores como el tipo de metal que se funde y la complejidad del molde.. Generalmente, Los moldes pueden durar desde decenas de miles hasta cientos de miles de ciclos..
2. ¿Se puede utilizar la fundición a presión para tiradas de producción pequeñas??
Si bien la fundición a presión suele ser más rentable para grandes tiradas de producción debido a los altos costos iniciales, se puede utilizar para tiradas más pequeñas si las piezas son particularmente complejas o si hay otros factores que lo justifiquen.
3. ¿Cómo se compara la fundición a presión con otros métodos de fundición??
La fundición a presión ofrece una precisión superior, tiempos de producción más rápidos, y mejores acabados superficiales en comparación con muchos otros métodos de fundición. Sin embargo, también requiere una mayor inversión inicial y es menos flexible en cuanto a los metales que se pueden utilizar.
4. ¿Cuáles son los defectos comunes en la fundición a presión??
Los defectos comunes incluyen porosidad., que son pequeños huecos en la parte fundida, errores en los que el metal no llena completamente el molde, y imperfecciones superficiales. El control y mantenimiento adecuados del proceso pueden minimizar estos problemas..
5. ¿Cómo se elige el metal adecuado para la fundición a presión??
La elección del metal depende de los requisitos de la aplicación.. El aluminio es ligero y resistente., El zinc ofrece alta precisión y facilidad de fundición., y el magnesio es ligero y fácil de mecanizar. Cada metal tiene su propio conjunto de propiedades que lo hacen apto para diferentes usos..