¿Alguna vez se ha preguntado cómo se hacen esas intrincadas piezas de metal en su automóvil o electrodomésticos?? Uno de los métodos más geniales utilizados es la fundición de died de gravedad. Es un proceso fascinante que combina la ciencia, arte, e ingeniería para crear componentes de metal de alta calidad. Vamos a sumergirnos en el lanzamiento del mundo de la gravedad y ver qué lo hace funcionar.
Conceptos básicos de la gravedad de la fundición
¿Qué es la fundición a presión por gravedad??
Fundición a presión por gravedad, Simplemente poner, es un método para verter metal fundido en un molde usando gravedad. No se aplica presión externa; El metal llena el molde debido a su peso. Esta técnica es excelente para crear robusta, piezas de alta calidad con excelente precisión dimensional.
Cómo difiere de otros métodos de fundición de troquel?
A diferencia de otros métodos como la fundición a presión de presión, donde el metal se ve obligado a entrar al molde a alta presión, La fundición de la muerte por gravedad se basa solo en la gravedad. Esto significa menos complicaciones de maquinaria y presión., resultando en un proceso más simple y a menudo más rentable. Pero, ¿Cómo funciona todo??
Proceso de fundición de died de gravedad
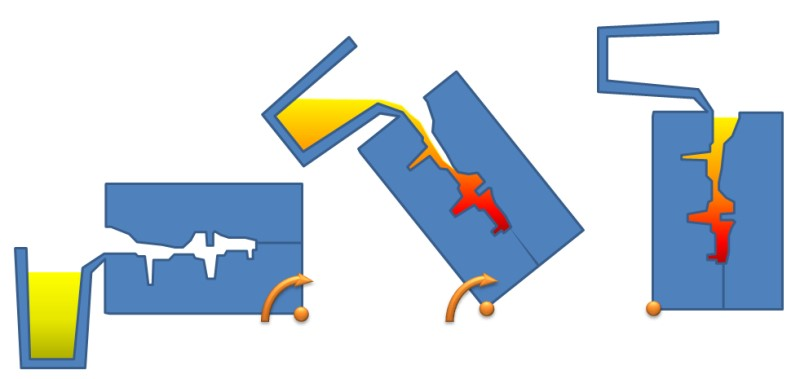
Preparación
Antes de que se derrita cualquier metal, La preparación es clave.
#1: Diseño y creación de moldes: El viaje comienza con el diseño y la creación del molde.. Estos moldes generalmente están hechos de acero o hierro fundido para resistir las altas temperaturas del metal fundido. La precisión en el diseño de moho asegura que el producto final cumpla con las especificaciones exactas.
#2: Selección de materiales: Próximo, El material correcto debe ser elegido. Aluminio y zinc son opciones populares debido a sus excelentes propiedades y resistencia de fundición.
Proceso de fundición
Ahora, en el corazón del proceso!
#3: Derretirse y vertiendo: El metal seleccionado se derrite en un horno hasta que alcanza un estado líquido. Este metal fundido se vierte cuidadosamente en el molde precalentado. La gravedad hace su trabajo aquí, permitiendo que el metal fluya y llene cada rincón y grieta del molde.
#4: Enfriamiento y solidificación: Una vez que se llena el molde, Se deja para enfriar. Mientras se enfría, El metal se solidifica, Tomando la forma del molde. Este proceso de enfriamiento es crucial para garantizar la integridad estructural de la parte del reparto.
Procedimientos posteriores a la clasificación
Después de que el metal se haya solidificado, El proceso aún no ha terminado.
#5: Eliminar el casting del molde: La parte solidificada se elimina cuidadosamente del molde. Esto puede implicar abrir el molde o separar las piezas de molde temporales.
#6: Acabado e inspección: Finalmente, el casting se limpia, Cualquier exceso de material se recorta, y sufre inspección para garantizar que cumpla con los estándares de calidad. Esto podría incluir mecanizado, pulido, u otras técnicas de acabado para lograr las especificaciones deseadas.
Materiales utilizados en la fundición de troqueles de gravedad
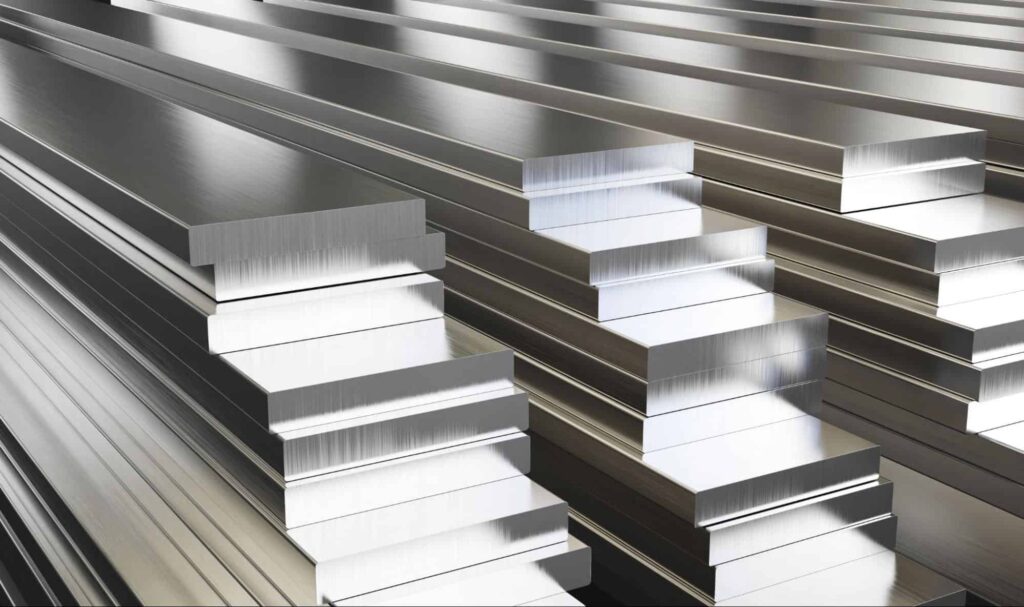
Metales comúnmente utilizados
Diferentes metales aportan diferentes fortalezas a la mesa:
- Aluminio: Ligero, resistente a la corrosión, y excelente para elenco detallado. A menudo se usa en las industrias automotrices y aeroespaciales..
- Zinc: Conocido por su fuerza y durabilidad, El zinc es perfecto para piezas que necesitan resistir el desgaste.
Aleaciones populares en la gravedad matan
El uso de aleaciones puede mejorar las propiedades como la resistencia, ductilidad, y resistencia a la corrosión. Por ejemplo, La combinación de aluminio con silicio puede mejorar la fluidez y reducir la contracción durante el enfriamiento.
Ventajas de la gravedad de la fundición
Calidad y precisión
- Producción de alta calidad: La fundición de died de gravedad produce piezas con superficies lisas y excelente precisión dimensional. Esta alta calidad significa menos trabajo de postprocesamiento.
- Precisión y consistencia: Los moldes se aseguran de que cada parte sea idéntica, que es crucial para las industrias donde la precisión es clave.
Rentabilidad
- Beneficios de costos: En comparación con métodos como la fundición a presión de presión, La fundición a la muerte por gravedad es a menudo más barata debido a la simplicidad del proceso y el equipo.
- Ahorros a largo plazo: Los moldes duraderos utilizados en la fundición de troqueles de gravedad pueden producir miles de piezas antes de necesitar reemplazo, ahorrar costos a largo plazo.
Versatilidad
- Gama de aplicaciones: De automotriz a aeroespacial, La fundición de la died de gravedad es lo suficientemente versátil para una amplia gama de industrias.
- Opciones de personalización: El proceso permite modificaciones en el diseño de moho, haciendo posible crear piezas personalizadas adaptadas a necesidades específicas.
Desventajas de la gravedad del lanzamiento
Costos iniciales de configuración
- Alta inversión inicial: Configurar el moho y el equipo iniciales puede ser costoso, Aunque estos costos se compensan en largas ejecuciones de producción.
- Costos de creación de moho: Diseñar y fabricar moldes precisos es un costo inicial significativo.
Limitaciones de materiales
- Limitado a ciertos metales y aleaciones: No todos los metales son adecuados para la fundición de died de gravedad, que puede limitar las opciones de material.
- Desafíos con materiales específicos: Algunos metales pueden no fluir tan bien o pueden requerir temperaturas más altas., complicando el proceso.
Volumen de producción
- Idoneidad para diferentes volúmenes de producción: La fundición de troqueles de gravedad es excelente para carreras de producción media a grande, pero puede que no sea rentable para volúmenes muy bajos o muy altos.
- Eficiencia a diferentes escalas: El método es menos eficiente para piezas muy grandes o muy pequeñas debido a las limitaciones en el diseño de moho y el flujo de metal..
Aplicaciones de la fundición de troqueles de gravedad
Industria automotriz
- Componentes del motor: El lanzamiento de la muerte por gravedad es perfecto para fortalecer, piezas precisas del motor.
- Piezas estructurales: El método produce componentes estructurales duraderos y livianos.
Industria aeroespacial
- Piezas de aeronaves: La precisión y la fuerza lo hacen ideal para componentes críticos de aeronaves.
- Componentes especializados: La fundición de died de gravedad puede producir piezas con geometrías complejas necesarias en aeroespacial.
Bienes de consumo
- Electrónica y electrodomésticos: Muchas piezas duraderas y detalladas en electrónica y artículos domésticos se hacen utilizando fundición de troquel de gravedad.
- Artículos para el hogar: De las manijas a los marcos, Muchos artículos cotidianos se benefician de este método de casting.
Aplicaciones industriales
- Partes de maquinaria: Las piezas de maquinaria resistentes y confiables a menudo se producen de esta manera.
- Herramientas y equipos: La fundición de troqueles de gravedad proporciona la durabilidad necesaria para las herramientas y equipos industriales.
Comparación con otros métodos de casting
Moldeo en arena
- Diferencias y similitudes: La fundición de arena usa moldes de arena, haciéndolo más flexible pero menos preciso. Es ideal para grandes partes, pero no para detalles finos..
- Pros y contras: La fundición de arena es más barata para carreras cortas y grandes partes, Pero la fundición de died de gravedad ofrece una mejor precisión y acabado superficial.
Casting de presión a presión
- Diferencias y similitudes: La fundición a presión, usa alta presión para forzar el metal en moldes, ofreciendo una excelente precisión pero a costos más altos.
- Pros y contras: La fundición a presión a presión es ideal para la producción de alto volumen de piezas pequeñas a medianas, Mientras que la fundición de troqueles de gravedad es más rentable para las carreras medianas.
Fundición a la cera perdida
- Diferencias y similitudes: La fundición de inversión utiliza patrones de cera y moldes de cerámica, proporcionando alta precisión y acabados suaves, Pero a un costo más alto.
- Pros y contras: El casting de inversión es perfecto para pequeño, partes intrincadas, Mientras que los saldos de fundición a gravedad se costan y precisión para una gama más amplia de piezas.
Conclusión
Gravity Die Casting es una potencia en el mundo de la fabricación, ofreciendo una mezcla de calidad, precisión, y rentabilidad. Si estás en el automóvil, aeroespacial, o industria de bienes de consumo, Comprender este proceso puede ayudarlo a tomar mejores decisiones de fabricación. Con sus ventajas únicas y algunas limitaciones, Está claro que la fundición de troqueles de gravedad ocupa un lugar significativo en la fabricación moderna.
Preguntas frecuentes
- ¿Cuál es la principal diferencia entre la fundición de la muerte por gravedad y el lanzamiento de troqueles de presión?? La fundición de died de gravedad se basa en la gravedad para llenar el molde, Mientras que la fundición a la presión de presión usa alta presión. Esta diferencia afecta los tipos de piezas que cada método es el más adecuado para.
- ¿Se puede utilizar la fundición de died de gravedad para formas complejas?? Sí, La fundición de died de gravedad puede producir formas complejas, especialmente cuando se usa moldes bien diseñados, Aunque los diseños muy intrincados pueden ser más adecuados para otros métodos.
- ¿Cuáles son los metales más comunes utilizados en la fundición de troqueles de gravedad?? El aluminio y el zinc son los más comunes, Gracias a sus excelentes propiedades y resistencia de casting.
- ¿Cómo la fundición de muerte por gravedad garantiza una alta precisión?? La precisión proviene de los moldes detallados y el proceso de enfriamiento controlado, que garantiza una calidad constante y precisión dimensional.
- ¿Cuáles son los beneficios ambientales de la fundición de troqueles de gravedad?? La fundición de died de gravedad puede ser más amigable con el medio ambiente debido a un menor consumo de energía en comparación con los métodos de alta presión y la capacidad de reciclar y reutilizar materiales y moldes.