Alguna vez se preguntó cómo se hacen esas piezas de fundición de aluminio y zinc en sus dispositivos y electrodomésticos? Estás mirando la magia del casting! Este proceso permite la creación de componentes de metal complejos y precisos utilizados en todo. Die Casting Auto Parts a la cocina. Pero elegir el metal adecuado para su proyecto puede ser un raspador de cabeza. Ingrese zinc y aluminio, Dos pesos pesados en el mundo de fundición de diedes de metal, cada uno con su propio conjunto de fortalezas. Así que abrochate, Porque estamos a punto de sumergirnos en la batalla de los metales.
¿Qué es la fundición a presión??
Pensar en fundición a presión Como una magia de moldeo de metal. Un metal fundido (como zinc o aluminio) se inyecta en un dado con precisión elaborado, Algo así como verter la masa en un molde para pastel. El metal se enfría, solidifica, y voila - tienes una parte terminada, Listo para rockear y rodar. Es un rápido, eficiente, y método versátil para producir componentes de metal de alta calidad.
Fundición a presión de zinc
El zinc es el campeón desvalido del mundo del casting de Die, a menudo pasado por alto pero lleno de beneficios. Vamos a entrar en la esgrafía:
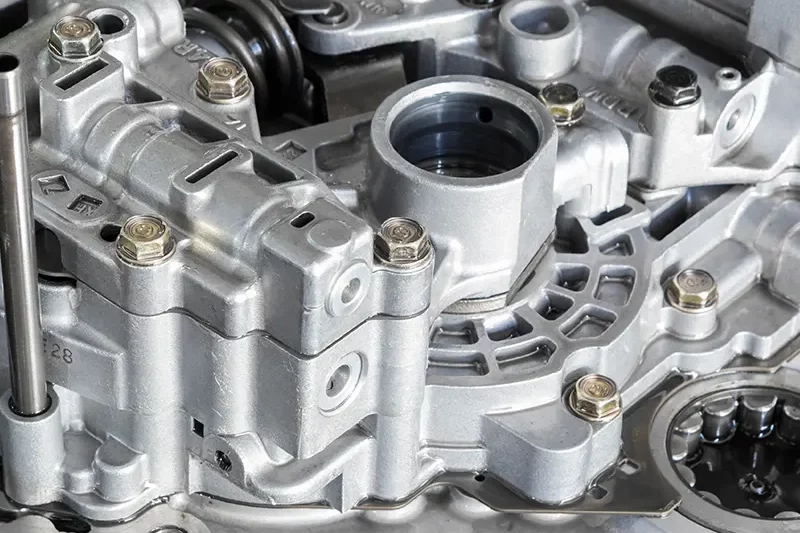
Propiedades del zinc
El zinc es un metal conocido por su versatilidad, Justo como ese amigo que puede sacudir un traje y aún conquistar una pista de baile. Es relativamente suave, fácil de trabajar con, y tiene una capacidad única para amortiguar las vibraciones de sonido. Más, El zinc tiene un punto de fusión bajo, convirtiéndolo en una elección económica para el casting.
Ventajas de usar zinc
¿Por qué deberías elegir zinc para tu próximo proyecto de casting?? Aquí está el Lowdown:
- Rentabilidad: El zinc es un metal económico, haciéndolo una opción atractiva para las empresas que buscan guardar algo de masa.
- Durabilidad y resistencia: No dejes que su suavidad te engañe, El zinc es sorprendentemente duro. Es duradero y puede manejar su peso, una excelente opción para los componentes que necesitan resistir el desgaste y la desgarro.
- Precisión y detalle: La capacidad de Zinc para capturar detalles intrincados es un cambio de juego. Quiere crear una parte con líneas finas y formas complejas? El zinc puede manejarlo como un profesional.
Aplicaciones de la fundición de died de zinc
Casting de zinc die, con su combinación única de propiedades, se ha convertido en un componente vital en una amplia gama de industrias. Es como el camaleón de los metales, adaptándose a la perfección a diversas aplicaciones. Piensa en tu vida cotidiana: Ese elegante, botella de desinfectante de manos ergonómica que llevas, la robusta manija de la puerta que usas todos los días, Incluso esas elegantes piezas de automóviles que agregan un toque de elegancia a su vehículo, lo más probable es, Zinc está trabajando en silencio detrás de escena.
Es un metal que no tiene miedo de ensuciarse las manos, Desde la creación de componentes intrincados para la industria automotriz hasta la elaboración de piezas delicadas para electrónica. La versatilidad del zinc brilla en su capacidad para crear artículos funcionales y decorativos, convirtiéndolo en una opción popular para todo, desde el hardware de construcción hasta los accesorios decorativos.
Fundición a presión de aluminio
Vamos a cambiar de marcha y ver aluminio, el metal favorito para muchas aplicaciones de fundición.
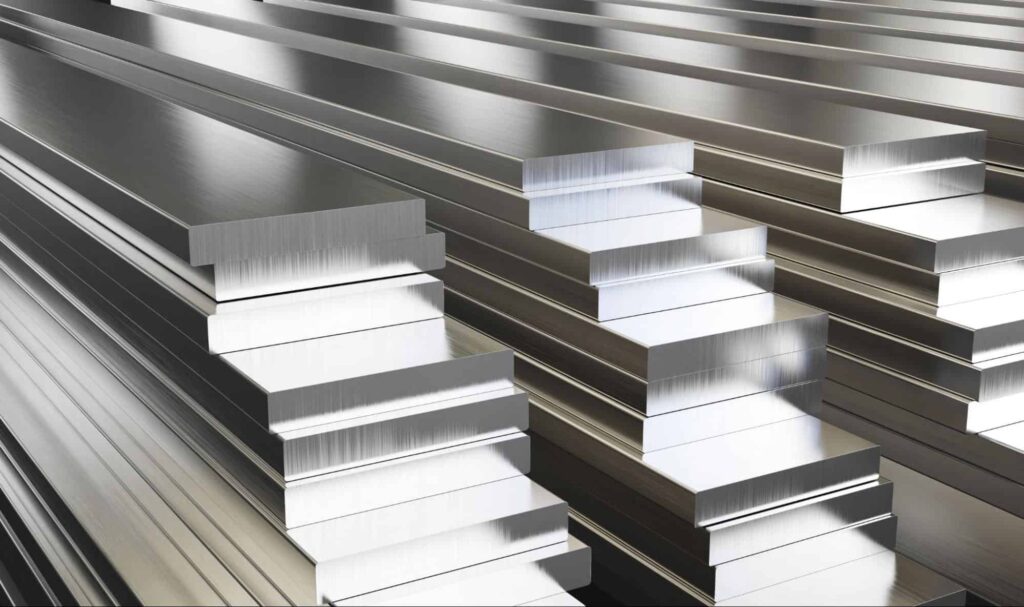
Propiedades del aluminio
El aluminio es como el hermano deportivo de los metales: liviano, fuerte, y con un perfil elegante. También es muy resistente a la corrosión, haciéndolo una opción superior para aplicaciones al aire libre.
Ventajas del uso de aluminio
El aluminio tiene su propio conjunto de características ganadoras:
- Propiedades livianas: El aluminio es un campeón de peso pluma, haciéndolo ideal para componentes que necesitan ser ligeros y ágiles, Como los que se encuentran en las industrias aeroespaciales y automotrices.
- Resistencia a la corrosión: El aluminio es una galleta dura cuando se trata de óxido y corrosión. Puede soportar condiciones duras, haciéndolo una excelente opción para los muebles de exterior, marcos de ventana, y otras aplicaciones expuestas a los elementos.
- Conductividad térmica y eléctrica: El aluminio es un conductor de calor y electricidad, haciéndolo ajustado perfecto para aplicaciones donde estas propiedades son cruciales, como disipadores de calor y componentes eléctricos.
Aplicaciones de fundición a died de aluminio
Fundición a presión de aluminio es un verdadero camaleón del mundo de la fabricación, adaptarse sin problemas a una amplia gama de industrias. No es solo un metal; Es una herramienta versátil utilizada para crear todo, desde los componentes básicos de nuestro mundo hasta los componentes intrincados que alimentan nuestros dispositivos. Encontrarás fundiciones de aluminio en piezas de construcción, donde contribuyen a estructuras duraderas y livianas, y en el mundo de piezas electrónicas, donde su capacidad para realizar calor y electricidad los hace esenciales para componentes sensibles.
La ligereza del aluminio es un activo clave, permitiendo que se elevara en la industria aeroespacial, donde el peso es un factor crítico. También es un ingrediente vital en la industria automotriz, Ayudando a crear vehículos de bajo consumo de combustible y mejorar las características de seguridad. Y no olvidemos esas bicicletas elegantes que adornan nuestras calles, Impulsado por componentes hechos posibles por fundición de troqueles de aluminio. Incluso esos gadgets elegantes sin los que no puedes vivir, Desde teléfonos inteligentes hasta tabletas, confiar en las propiedades únicas de aluminio para funcionar sin problemas.
Zinc vs.. Fundición a presión de aluminio
Ahora, Para el enfrentamiento, todos hemos estado esperando: zinc versus aluminio! Pesemos sus pros y contras con cara a cara:
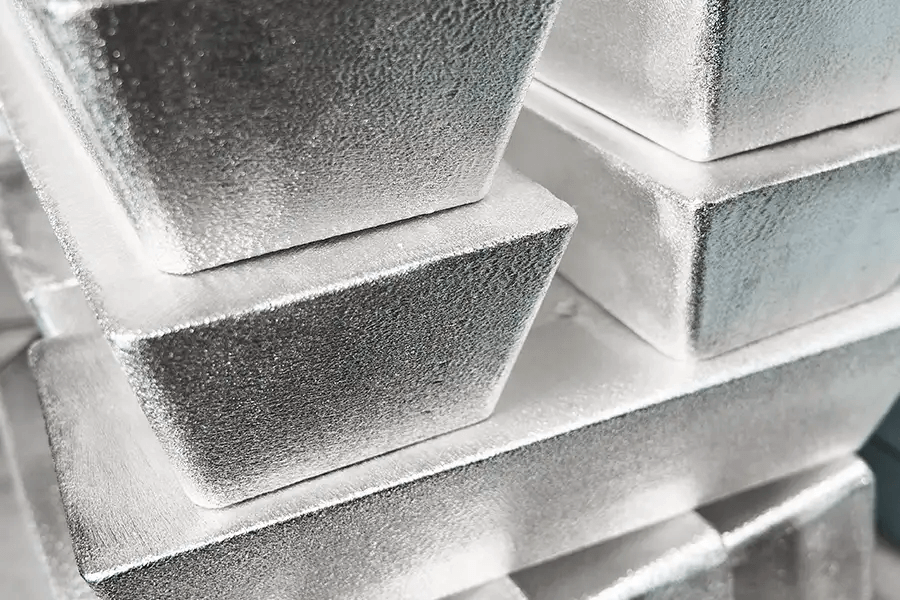
Zinc vs.. Aluminio: Fortaleza
Al comparar la aleación de zinc vs. resistencia al aluminio, El aluminio toma la delantera en la categoría de fuerza, con una mayor resistencia a la tracción que el zinc. Es como el Muscleman of the Metal World. Pero no subestimes el zinc! Sigue siendo un contendiente sólido y a menudo es lo suficientemente fuerte para muchas aplicaciones..
Consideraciones de peso
Las propiedades de peso pluma de aluminio lo convierten en el claro ganador aquí. Es el campeón del diseño liviano, permitido Fabricante de piezas de fundición de aluminio para crear partes fundidas de aluminio más ligero sin comprometer la fuerza. El zinc es más pesado, Pero sigue siendo una opción sólida para muchas aplicaciones en las que el peso del producto de fundición de died de zinc no es una gran preocupación.
Costo de casting de die
El casting de la aleación de zinc es la elección del presupuesto. Es como la opción de menú de valor, ofreciendo calidad sin romper el banco. El aluminio puede ser más caro, Pero sus propiedades únicas pueden justificar el mayor costo para aplicaciones específicas.
Conclusión
Entonces, quien gana la última batalla de zinc vs. aluminio? No hay una respuesta única para todos. Todo depende de sus necesidades y aplicación específicas. Necesito un peso ligero, fuerte, y componente resistente a la corrosión? El aluminio es tu campeón. Buscando un rentable, durable, y parte orientada a los detalles? El zinc es tu opción. Por último, Se trata de comprender los requisitos de su proyecto y elegir el metal que mejor se adapte a sus necesidades.
Preguntas frecuentes
1. ¿Cuáles son las principales diferencias entre el lanzamiento de zinc y aluminio??
El zinc es conocido por su rentabilidad, durabilidad, y capacidad para capturar detalles finos, mientras que el aluminio brilla en sus propiedades livianas, resistencia a la corrosión, y conductividad térmica.
2. ¿Qué metal es mejor para la producción de alto volumen??
Tanto el zinc como el aluminio son adecuados para la producción de alto volumen, Pero el zinc a menudo se prefiere debido a su menor costo.
3. ¿Se puede utilizar el zinc para aplicaciones al aire libre??
Mientras que el zinc es naturalmente resistente a la corrosión, No es tan resistente a la corrosión como el aluminio. Para condiciones de exteriores duras, El aluminio es la mejor opción.
4. ¿Qué factores debo considerar al elegir entre zinc y aluminio??
Considere los requisitos de su proyecto, incluido el peso, fortaleza, resistencia a la corrosión, nivel de detalle, y costo.
5. Se pueden reciclar tanto el zinc como el aluminio?
Sí, Tanto el zinc como el aluminio son metales altamente reciclables, Haciéndolos decisiones ecológicas.