Pièces de meubles Casting joue un rôle crucial dans la création de meubles durables et esthétiques. Pour vraiment apprécier le talent artistique et l'artisanat derrière le casting des meubles, Il est important de comprendre les secrets et les techniques qui entrent dans ce processus.

Les bases des pièces de meubles coulant:
Le coulage des pièces de meubles peut être défini comme la méthode de création composants de meubles en versant du métal ou alliage fondu dans un moule pour obtenir la forme souhaitée. Cette technique est largement utilisée dans l'industrie du meuble car elle permet de produire des pièces complexes et précises. Les matériaux utilisés dans les pièces de meubles coulant varient en fonction des caractéristiques souhaitées du produit final. Métaux comme le fer, acier, et l'aluminium, ainsi que divers alliages, sont couramment utilisés. Ces matériaux offrent une durabilité, force, et un large éventail de finitions. Différents types de pièces de mobilier peuvent être jetées à travers ce processus, y compris jambes de chaise, bases de table, et accents décoratifs, Ajout d'élégance et de fonctionnalité à la conception globale.
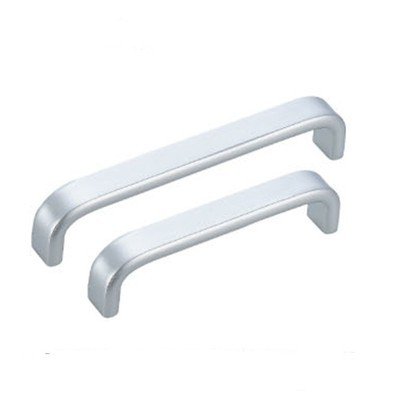
Applications de coulage de pièces de meubles communs
– Cuisses de table:
Le moulage des pièces de meubles est utilisé pour créer des jambes de table robustes et décoratives, qui assurent la stabilité et l'esthétique aux tables de différentes tailles et styles.
– Cadres de chaise:
La coulée est utilisée pour fabriquer des cadres de chaises durables et complexes, Assurer la force et le confort pour différents types de chaises.
– Accents décoratifs:
La coulée permet la création d'accents décoratifs comme les garnitures ornées, rosettes, et panneaux décoratifs qui améliorent l'apparence globale des meubles.
– Matériel:
Les pièces de meubles coulant sont utilisées pour produire des composants matériels tels que des tiroirs, boutons, charnières, et serrures, qui ajoutent des fonctionnalités et du style aux armoires, tiroirs, et les portes.
– Cadres de lit:
La coulée aide à fabriquer des cadres de lit de différents modèles et tailles, Fournir un soutien robuste et un appel visuel aux lits.
– Sofa et bras de chaise:
La coulée permet la production de canapés et de bras de chaise, Assurer l'intégrité structurelle et ajouter des éléments architecturaux aux meubles.
– Bases de table:
La coulée est utilisée pour créer des bases de table robustes et visuellement attrayantes, qui assurent la stabilité et le soutien aux tables à manger, tables basses, et d'autres meubles similaires.
– Jambes de vanité:
Le moulage permet la création de jambes de vanité élégantes et durables, Améliorer l'esthétique et les fonctionnalités des vanités de salle de bain.
– Supports d'étagère:
Les pièces de mobilier la coulée est utilisée dans la production de supports d'étagère, qui offrent un soutien fiable aux étagères, bibliothèques, et d'autres unités de stockage.
– Entourage de cheminée:
La coulée peut être utilisée pour fabriquer des environs de cheminée décoratifs, Créer un point focal et ajouter du charme aux espaces de vie.
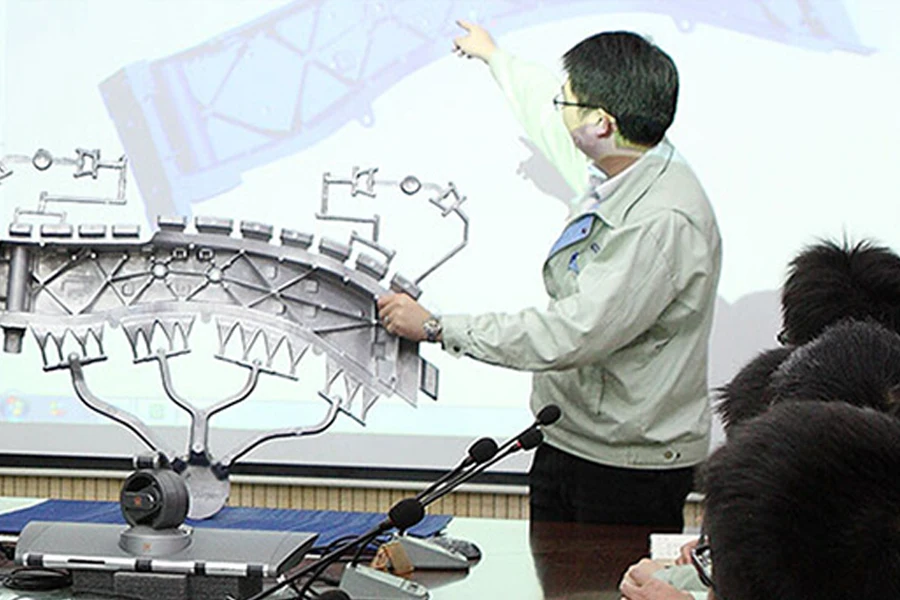
La science derrière les pièces de meubles jet:
La création de pièces de meubles par le casting est à la fois un art et une science. Le processus commence par les considérations de conception.
Des facteurs tels que la fonctionnalité, esthétique, et la faisabilité de la fabrication doit être soigneusement analysée avant de continuer.
Un moule est ensuite créé, soit par conception assistée par ordinateur (GOUJAT) logiciel ou par des artisans experts. Le moule, Souvent fait de silicone ou de plâtre, joue un rôle essentiel dans le processus de casting.
Le métal fondu est versé dans le moule, remplir l'espace et prendre la forme de la partie de meubles souhaitée.
Une fois que le métal se solidifie, le moule est retiré, Et la pièce subit d'autres processus de finition pour atteindre la texture souhaitée, couleur, et qualité de surface.
Techniques de pièces de rejet de meubles:
Diverses méthodes de coulée sont utilisées dans la fabrication de meubles, chacun avec ses propres avantages et limitations.
Moulage au sable, L'une des méthodes les plus traditionnelles, implique la création d'un moule en emballant le sable autour d'un motif, qui est ensuite supprimé pour créer une cavité.
Moulage de précision, également connu sous le nom de fonte à la cire perdue, nécessite de créer un modèle de cire qui est recouvert de céramique avant que la cire ne soit fondée. La coque en céramique restante est ensuite remplie de métal fondu.
Moulage sous pression, d'autre part, implique l'utilisation d'un moule en acier, où le métal fondu est injecté sous haute pression.
Chaque technique de coulée offre des avantages uniques, comme créer des formes complexes ou atteindre une haute précision. La sélection de la méthode la plus appropriée dépend des exigences spécifiques de la partie de la partie de meubles.
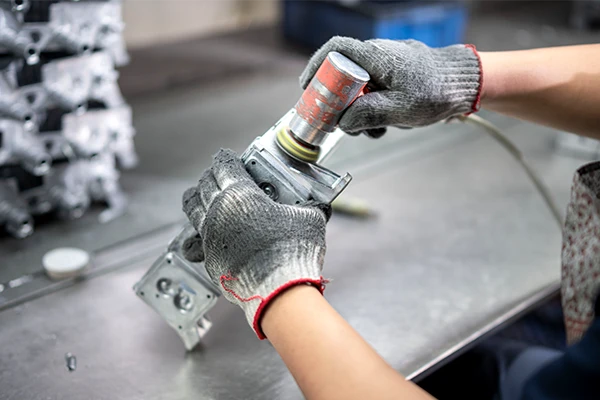
Contrôle de la qualité dans les pièces de meubles Casting:
Le contrôle de la qualité est de la plus haute importance dans le casting de pièces de meubles. Techniques de coulée appropriées, matériels, et les processus de finition doivent être mis en œuvre pour assurer des composants de meubles durables et esthétiques. Tester la composition du métal ou de l'alliage, ainsi que la réalisation d'inspections tout au long du processus de coulée, aide à identifier et à prévenir les défauts communs, comme la porosité, rétrécissement, ou imperfections de surface. La mise en œuvre de mesures strictes de contrôle de la qualité garantit que le produit final répond aux normes les plus élevées de l'artisanat et de la durabilité.
Eco Pratiques dans les pièces de meubles Casting:
À mesure que la demande de pratiques durables dans la fabrication augmente, L'industrie du casting de pièces de meubles adopte également des approches respectueuses de l'environnement. Les fabricants s'efforcent activement de réduire les déchets et la consommation d'énergie, ainsi que minimiser l'impact environnemental du processus de coulée. Cela comprend la mise en œuvre de programmes de recyclage pour l'excès de matériel et l'exploration des techniques de coulée alternatives qui nécessitent moins d'énergie. L'utilisation de matériaux recyclés ajoute un élément écologique à la coulée de meubles, mettre en évidence l'engagement de l'industrie à une approche plus verte.
Conclusion
Révéler les secrets et les techniques des pièces de meubles Casting a mis en lumière le processus complexe derrière la création de composants de meubles. En mettant l'accent sur la tradition et l'innovation, Le monde des pièces de mobilier continue continue d'évoluer et de captiver, Inspirer la création de meubles intemporels et époustouflants.