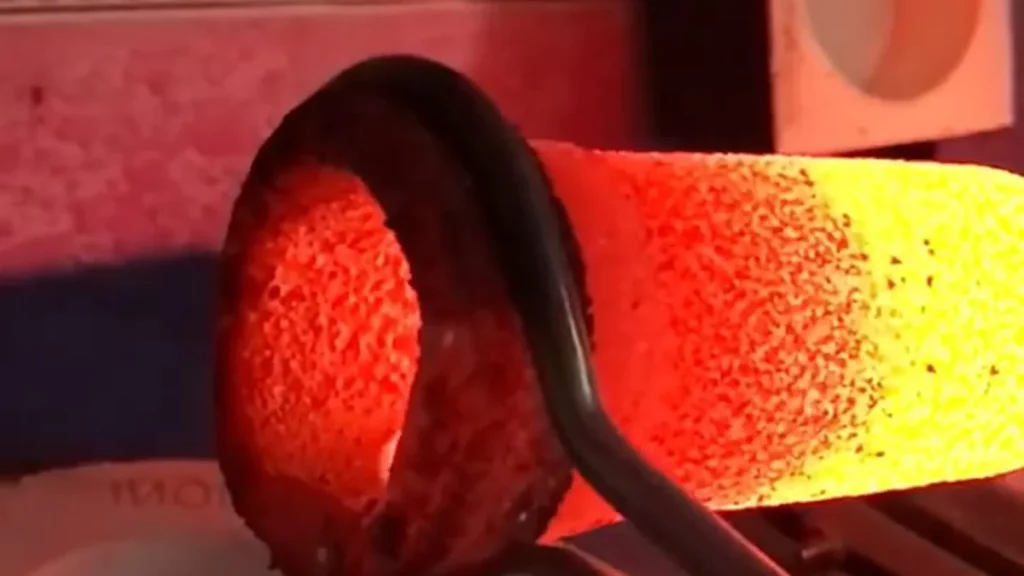
Source des images: pixels
Moulage sous pression d'aluminium et moulage au sable, chaque méthode façonne notre monde de manière unique, des voitures que nous conduisons aux gadgets sans lesquels nous ne pouvons pas vivre.
Mais qu’est-ce qui distingue ces processus? Pourquoi choisir l'un plutôt que l'autre?
Dans cet article, nous allons plonger dans le noyau fondu du moulage sous pression vs. moulage au sable. Nous explorerons leurs points forts, faiblesses, et les industries qu'ils ont révolutionnées. Que vous soyez ingénieur, un propriétaire d'entreprise, ou simplement curieux de savoir comment les choses sont fabriquées, cette comparaison mettra en lumière le talent artistique caché dans les objets du quotidien.
Présentation des méthodes de diffusion
Moulage sous pression en aluminium
Description du processus
- Le métal en fusion est forcé dans des moules en acier réutilisables sous haute pression.
- Les moules, connu sous le nom de meurt, sont conçus pour créer des formes complexes avec précision et cohérence.
- Les pièces produites ont des caractéristiques bien définies et peuvent présenter des surfaces lisses ou texturées.
Matériaux utilisés
- Aluminium: Couramment utilisé en raison de sa légèreté et de ses excellentes propriétés thermiques.
- Autres alliages: Zinc, magnésium, et les alliages à base de cuivre sont également utilisés pour des applications spécifiques.
Avantages
- Précision: Offre une précision dimensionnelle et une répétabilité élevées pour les pièces complexes.
- Finition de surface: Fournit une gamme de finitions attrayantes adaptées à diverses industries.
- Efficacité: Permet la production de pièces avec des exigences de post-traitement minimales.
Inconvénients
- Coût initial: Nécessite un investissement dans l'outillage et la configuration pour la création de matrices.
- Taille limitée: Pas idéal pour les grandes pièces en raison des contraintes de moule.
Moulage en sable
Description du processus
- Implique de verser du métal en fusion directement dans des moules en sable sans haute pression.
- Permet la création de formes nettes dans un niveau de tolérance d'un quart de pouce.
- Offre une polyvalence dans la production de pièces de complexité variable.
Matériaux utilisés
- Moules à sable: Des moules économiques adaptés à une large gamme de tailles et de formes de pièces.
- Alliages métalliques: Convient pour couler une variété de métaux comme le fer, acier, aluminium, et du bronze.
Avantages
- Versatilité: Accepte des pièces plus grandes avec plus de flexibilité dans les modifications de conception.
- Outillage rentable: Nécessite moins d’investissement initial par rapport aux méthodes de moulage sous pression.
Inconvénients
- Finition de surface: Donne des textures plus rugueuses par rapport aux finitions moulées sous pression.
- Précision dimensionnelle: Peut nécessiter des processus post-coulée supplémentaires pour des ajustements de précision.
Comparaison détaillée
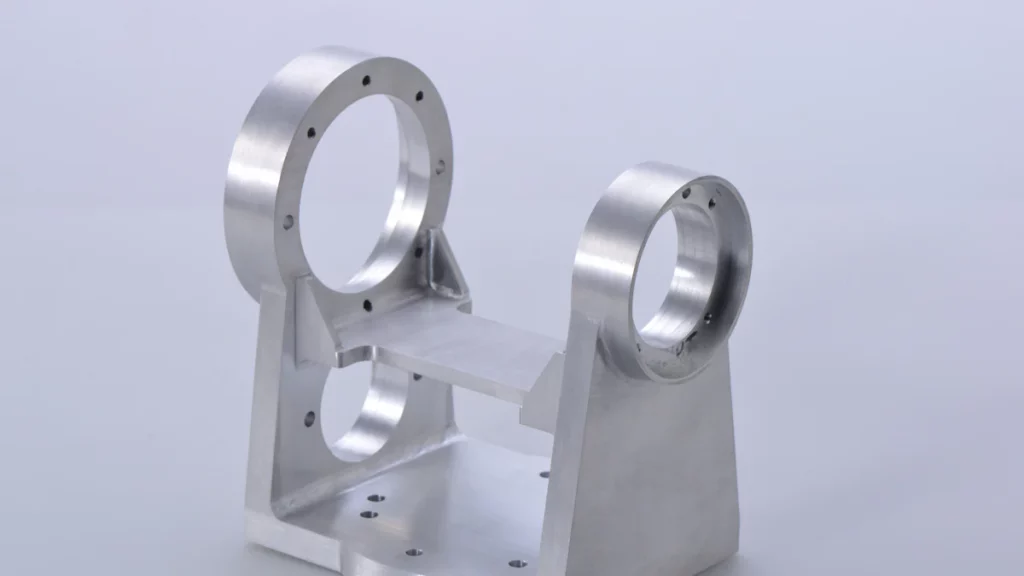
Source des images: ne pas éclabousser
Vitesse et volume de production
Vitesse de moulage sous pression en aluminium vs. vitesse de coulée au sable
- Le moulage sous pression d'aluminium excelle dans la production rapide, atteindre des vitesses élevées grâce à ses processus automatisés.
- Moulage au sable, bien que polyvalent, fonctionne à un rythme plus lent car il implique du travail manuel dans conception de moule.
Adaptation à différents volumes de production
- Moulage sous pression en aluminium:
- Idéal pour les courses de production à haut volume nécessitant une précision dimensionnelle précise.
- Convient aux composants avec des conceptions complexes et des demandes de qualité cohérentes.
- Moulage en sable:
- Plus adapté aux volumes de production faible à moyenne de pièces plus grandes.
- Offre une flexibilité à s'adapter à des tailles de pièces variables sans ajustements d'outillage significatifs.
Complexité et taille en partie
Capacités et limites de chaque méthode
- Moulage sous pression en aluminium: Excelle dans la production de formes complexes avec des tolérances étroites sans avoir besoin d'un usinage post-casting approfondi.
- Moulage en sable: Mieux adapté aux grands composants avec des exigences de précision moins strictes, Permettre des variations de conception plus indulgentes.
Tailles de pièces typiques pour la moulage et la coulée de sable
- Moulage sous pression: Spécialise dans les pièces plus petites à moyennes qui exigent une précision et des murs fins.
- Moulage en sable: Accueille des pièces plus grandes avec des murs plus épais, idéal pour les applications privilégiant la rentabilité plutôt que la précision dimensionnelle.
Finition de surface et précision dimensionnelle
Tolérances réalisables
- Moulage sous pression en aluminium:
- Maintient des tolérances étroites même dans les géométries complexes, réduisant le besoin d’opérations secondaires.
- Moulage en sable:
- Les tolérances sont généralement plus souples en raison de la nature du processus, nécessitant souvent des étapes de finition supplémentaires pour des ajustements de précision.
Comparaisons de qualité de surface
- Les pièces moulées sous pression présentent des finitions plus lisses avec des détails plus fins par rapport aux pièces moulées en sable connues pour leurs textures plus rugueuses..
Options matérielles
Alliages adaptés au moulage sous pression
- Aluminium: Largement utilisé en moulage sous pression pour ses propriétés légères et son excellente conductivité thermique.
- Zinc: Idéal pour les pièces complexes en raison de son faible point de fusion et de sa grande ductilité.
- Magnésium: Offre un rapport résistance/poids exceptionnel, adapté aux composants légers.
- Alliages à base de cuivre: Fournit une résistance à la corrosion et une conductivité thermique améliorées.
Alliages adaptés au moulage au sable
- Fer: Couramment utilisé dans le moulage au sable pour sa rentabilité et son usinabilité.
- Acier: Offre une polyvalence dans la production d'une large gamme de tailles de pièces avec des complexités variables.
- Aluminium: Convient au moulage au sable en raison de son faible point de fusion et de sa bonne fluidité.
- Bronze: Offre une excellente résistance à l’usure, ce qui le rend idéal pour les applications nécessitant de la durabilité.
Coûts d’outillage et d’installation
Investissement initial pour les matrices vs. moules à sable
- Moulage sous pression:
- Nécessite un investissement initial important dans des moules en acier adaptés à des conceptions de pièces spécifiques.
- Les coûts d'outillage initiaux peuvent être plus élevés mais compensés par les avantages à long terme de la production de masse.
- Moulage en sable:
- Implique des coûts initiaux inférieurs car les moules en sable sont plus abordables que les matrices en acier.
- Les dépenses d'outillage sont minimisées, ce qui en fait une option rentable pour les petites séries de production.
Considérations relatives aux coûts à long terme
- Moulage sous pression:
- Économies à long terme réalisées grâce à des capacités de production à haut volume et un gaspillage de matériaux minimal.
- La réduction des exigences d'usinage contribue à la rentabilité globale sur des cycles de production prolongés.
- Moulage en sable:
- Offre des solutions économiques pour les volumes de production faibles à moyens avec moins de coûts de maintenance des outils.
- La flexibilité dans les modifications de conception réduit les dépenses supplémentaires associées à la modification des configurations de moules.
Flexibilité de conception
Possibilité d'apporter des modifications à la conception
- Le moulage sous pression permet des modifications de conception complexes sans ajustements approfondis de l'outillage, assurer une adaptabilité rapide à l’évolution des exigences.
- Le moulage au sable offre une flexibilité dans la modification de la géométrie des pièces pendant le processus de fabrication du moule, s'adapter efficacement aux variations de conception.
Capacités de prototypage
- Moulage sous pression:
- Permet le prototypage rapide de pièces complexes avec une précision dimensionnelle précise, faciliter des phases de tests efficaces.
- Moulage en sable:
- Prend en charge le développement de prototypes de composants plus grands avec diverses géométries, permettant des améliorations de conception itératives.
Épaisseur de paroi
Épaisseur minimale réalisable pour chaque méthode
En aluminium moulé sous pression, l'épaisseur minimale de la paroi peut atteindre 1 mm, permettant des conceptions complexes avec des détails précis. Cette méthode excelle dans la production de pièces à paroi mince qui maintiennent l'intégrité structurelle. D'autre part, le moulage au sable nécessite généralement des parois plus épaisses, avec une épaisseur minimale d'environ 3 mm en raison de la nature du processus. L'épaisseur de paroi accrue dans le moulage au sable offre plus de flexibilité pendant la production et permet un processus post-coulée indulgent pour corriger efficacement toute inexactitude..
Implications pour le poids et la résistance des pièces
Lorsque l’on considère le moulage sous pression d’aluminium par rapport au moulage au sable, l'épaisseur de la paroi a un impact direct sur le poids et la résistance des pièces finales. Des parois plus fines obtenues grâce au moulage sous pression en aluminium permettent d'obtenir des composants plus légers sans compromettre la durabilité.. En revanche, les pièces moulées au sable avec des parois plus épaisses ont tendance à être plus lourdes mais offrent une résistance accrue, ce qui les rend adaptés aux applications nécessitant des structures robustes.
Exigences de post-traitement
Besoins de finition des pièces moulées sous pression
Les pièces moulées sous pression en aluminium nécessitent souvent un post-traitement minimal en raison de leur grande précision dimensionnelle et de leurs finitions de surface lisses.. Cependant, certaines touches de finition peuvent être nécessaires pour améliorer l'esthétique ou la fonctionnalité. Les techniques de post-traitement courantes incluent l'ébavurage, grenaillage, et revêtement en poudre pour affiner l'apparence et les performances des composants moulés sous pression.
Besoins de finition pour les pièces moulées en sable
En moulage au sable, le post-traitement joue un rôle crucial dans l'affinement des textures rugueuses inhérentes à cette méthode. Les pièces moulées au sable subissent généralement des processus de finition approfondis tels que le meulage, ponçage, ou usinage pour obtenir les qualités de surface et les précisions dimensionnelles souhaitées. Des traitements supplémentaires comme la peinture ou le placage peuvent également être appliqués pour améliorer l'apparence générale et la fonctionnalité des composants moulés au sable..
Considérations environnementales
Efficacité énergétique
Lorsque l'on compare le moulage sous pression d'aluminium au moulage en sable d'un point de vue environnemental, l’efficacité énergétique est un facteur clé. Le moulage sous pression de l'aluminium implique la fusion du métal à haute température en utilisant d'importantes ressources énergétiques.. En revanche, La coulée de sable consomme moins d'énergie car elle ne nécessite pas de processus de chauffage intenses. La baisse de la consommation d'énergie dans la coulée de sable contribue à une réduction de l'impact environnemental et des coûts opérationnels.
Déchets matériels et recyclabilité
La coulée de matrice en aluminium et la coulée de sable génèrent des déchets pendant la production; cependant, Leur recyclabilité diffère considérablement. La ferraille moulée peut être facilement recyclée dans de nouveaux composants sans compromettre la qualité ni les performances. D'autre part, Les moules de sable utilisés dans la coulée de sable ont une recyclabilité limitée en raison des problèmes de contamination de l'exposition aux métaux fondu. Des pratiques appropriées de gestion des déchets sont essentielles pour minimiser l'impact environnemental tout en maximisant l'efficacité des ressources.
Applications et aptitude
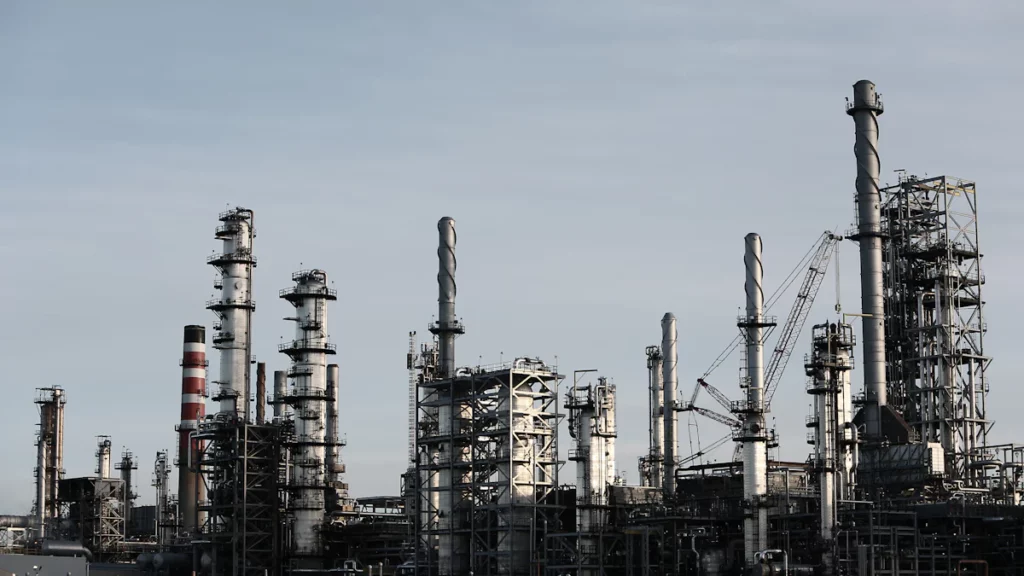
Source des images: pixels
Moulage sous pression en aluminium
Applications idéales
- Fabrication de composants complexes avec des géométries précises.
- Produire des pièces légères avec d'excellentes propriétés thermiques.
- Création de prototypes automobiles de haute qualité pour les tests et la validation.
Aptitude aux pièces de précision
- Assurer la précision dimensionnelle des composants critiques.
- Atteindre des normes de qualité cohérentes pour les applications aérospatiales.
- Fournir des solutions fiables pour la fabrication d’équipements médicaux.
Moulage en sable
Applications idéales
- Fabrication de composants de machines industrielles à grande échelle.
- Réalisation de sculptures artistiques et de pièces ornementales.
- Développer des éléments architecturaux rentables pour les projets de construction.
Aptitude aux grandes pièces
- Restauration pour la production de pièces de moteurs marins surdimensionnées.
- Construire des composants d’équipement agricole durables.
- Construire des éléments structurels pour des projets de développement d’infrastructures.
L'étude sur la fabrication additive pour la coulée rapide de sable met en évidence l'étude mécanique et microstructurale des prototypes automobiles en alliage en aluminium, souligner l'importance de maintenir les niveaux de ductilité pendant les phases de prototypage pour améliorer efficacement les propriétés des composants. Les efforts de recherche future visent à optimiser davantage les processus de fabrication tout en améliorant les caractéristiques mécaniques pour répondre efficacement à l'évolution de l'industrie (Métaux, 2024).
Conclusion
Lorsque vous comparez le moulage de la matrice en aluminium et le moulage de sable, Les principales différences résident dans la vitesse de production, complexité de la pièce, et les options matérielles. La coulée de matrice en aluminium excelle dans la précision et la finition de surface, Idéal pour les composants complexes. D'autre part, La coulée de sable offre une polyvalence pour des pièces plus grandes avec des outils rentables. En fonction de vos besoins d'application, Choisissez une moulage de dépérisation pour des géométries précises et une coulée de sable pour les composants à grande échelle. Considérez l'importance historique des origines de la coulée de sable dans la Chine ancienne et les progrès rapides de la fabrication additive pour les prototypes en aluminium pour prendre une décision éclairée sur la bonne méthode de casting.