कास्टिंग एक आकर्षक विनिर्माण प्रक्रिया है जो मोल्ड के माध्यम से पिघले हुए धातु को ठोस भागों में बदल देती है. चाहे आप जटिल गहने या बड़े पैमाने पर इंजन घटक बना रहे हों, आपके द्वारा चुनी गई कास्टिंग का प्रकार अंतर की दुनिया बना सकता है. आठ विभिन्न प्रकार की कास्टिंग में गोता लगाएँ, उनकी अनूठी विशेषताओं का अन्वेषण करें, और देखें कि कौन सा आपकी आवश्यकताओं के लिए सबसे अच्छा फिट हो सकता है.
#1: सैंड कास्टिंग
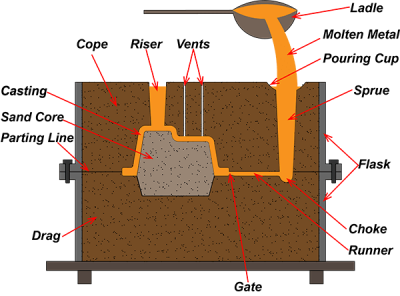
रेत कास्टिंग क्या है?
सैंड कास्टिंग सबसे पुरानी और सबसे व्यापक रूप से इस्तेमाल की जाने वाली कास्टिंग विधियों में से एक है. इसमें रेत के मिश्रण से एक मोल्ड बनाना शामिल है, मिट्टी, और पानी. एक बार सांचा तैयार हो जाए, पिघला हुआ धातु में डाला जाता है, गुहा को भरना और एक बार ठंडा और ठंडा होने के बाद वांछित आकार का निर्माण करना.
रेत कास्टिंग के अनुप्रयोग
सैंड कास्टिंग बड़े भागों और मध्यम-मात्रा के उत्पादन के लिए एकदम सही है. यह आमतौर पर विनिर्माण इंजन ब्लॉकों में उपयोग किया जाता है, मशीनरी भाग, और यहां तक कि कलात्मक मूर्तियां. इसका लचीलापन इसे विभिन्न उद्योगों में एक लोकप्रिय विकल्प बनाता है.
रेत कास्टिंग के फायदे और नुकसान
पेशेवरों:
- प्रभावी लागत: कम टूलींग लागत इसे छोटे और बड़े रन के लिए उपयुक्त बनाती है.
- बहुमुखी: आकार और जटिलताओं की एक विस्तृत श्रृंखला को समायोजित कर सकते हैं.
दोष:
- सतही समापन: आमतौर पर अन्य तरीकों की तुलना में मोटे तौर पर.
- आयामी सहिष्णुता: कम सटीक, जिससे अतिरिक्त मशीनिंग हो सकती है.
सामान्य सामग्री का उपयोग किया
सैंड कास्टिंग का उपयोग अक्सर कच्चा लोहा जैसी धातुओं के साथ किया जाता है, अल्युमीनियम, और कांस्य. ये सामग्रियां रेत मोल्ड के झरझरा प्रकृति के लिए अच्छी तरह से अनुकूल हैं.
#2: धातु - स्वरूपण तकनीक
निवेश कास्टिंग क्या है??
धातु - स्वरूपण तकनीक, इसे लॉस्ट-वैक्स कास्टिंग के रूप में भी जाना जाता है, भाग का एक मोम पैटर्न बनाना शामिल है, जो तब एक सिरेमिक शेल में लेपित होता है. एक बार शेल कठोर हो जाता है, मोम पिघल गया है, और पिघला हुआ धातु अंतिम भाग बनाने के लिए गुहा में डाला जाता है.
निवेश कास्टिंग के अनुप्रयोग
यह विधि एयरोस्पेस में उपयोग किए जाने वाले उच्च परिशुद्धता घटकों के उत्पादन के लिए आदर्श है, ऑटोमोटिव, और चिकित्सा उद्योग. यह जटिल विवरण और चिकनी खत्म की आवश्यकता वाले भागों के लिए एकदम सही है.
निवेश कास्टिंग के पक्ष और विपक्ष
पेशेवरों:
- उच्चा परिशुद्धि: के साथ जटिल ज्यामिति का उत्पादन करने में सक्षम उत्कृष्ट सतह खत्म.
- बहुमुखी प्रतिभा: धातुओं की एक विस्तृत श्रृंखला के साथ काम करता है, विदेशी मिश्र धातुओं सहित.
दोष:
- लागत: जटिल पैटर्न और गोले के कारण उच्च प्रारंभिक लागत.
- उत्पादन गति: आम तौर पर अन्य तरीकों की तुलना में धीमी गति से.
सामान्य सामग्री का उपयोग किया
निवेश कास्टिंग आमतौर पर स्टेनलेस स्टील जैसी सामग्रियों का उपयोग करता है, कार्बन स्टील, और Superalloys, जटिल मोल्ड गुहाओं में प्रवाह करने की उनकी क्षमता के लिए धन्यवाद.
#3: मेटल सांचों में ढालना
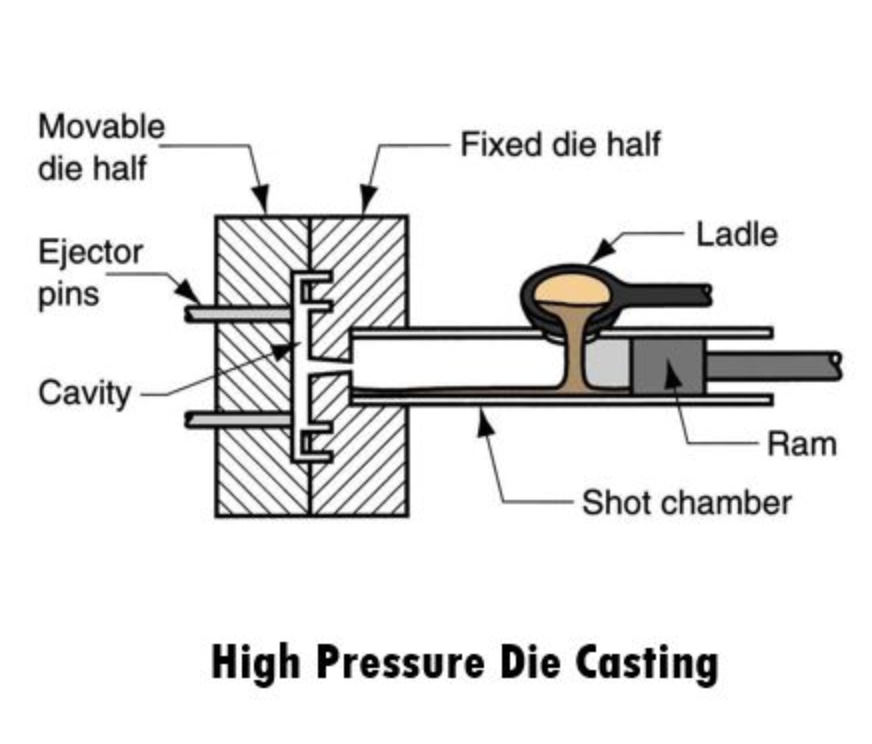
डाई कास्टिंग क्या है?
मेटल सांचों में ढालना उच्च दबाव में एक मोल्ड गुहा में पिघले हुए धातु को मजबूर करना शामिल है. सांचे, या मर जाता है, आमतौर पर स्टील से बने होते हैं और उच्च मात्रा वाले उत्पादन के लिए पुन: प्रयोज्य होने के लिए डिज़ाइन किए जाते हैं.
डाई कास्टिंग के अनुप्रयोग
डाई कास्टिंग का व्यापक रूप से उपयोग किया जाता है मोटर वाहन उद्योग इंजन घटकों और ट्रांसमिशन हाउसिंग जैसे भागों के उत्पादन के लिए. यह इलेक्ट्रॉनिक्स और उपभोक्ता वस्तुओं में भी लोकप्रिय है जो उच्च परिशुद्धता के साथ जटिल आकृतियों को बनाने की क्षमता के लिए है.
डाई कास्टिंग के फायदे और नुकसान
पेशेवरों:
- शुद्धता: उत्कृष्ट आयामी सटीकता और सतह खत्म.
- क्षमता: उच्च उत्पादन दर और स्थिरता.
दोष:
- टूलींग लागत: मरने के लिए उच्च प्रारंभिक लागत.
- भौतिक सीमाएँ: एल्यूमीनियम और जस्ता जैसे गैर-फेरस धातुओं के लिए सबसे उपयुक्त.
सामान्य सामग्री का उपयोग किया
अल्युमीनियम, जस्ता, और मैग्नीशियम का उपयोग आमतौर पर डाई कास्टिंग में किया जाता है, जो आसानी से जटिल मोल्ड में प्रवाहित करने की उनकी क्षमता और उच्च दबाव वाले अनुप्रयोगों के लिए उनकी उपयुक्तता के कारण होता है.
#4: स्थायी साँचे की ढलाई
परमानेंट मोल्ड कास्टिंग क्या है?
स्थायी मोल्ड कास्टिंग में एक पुन: प्रयोज्य धातु मोल्ड में पिघला हुआ धातु डालना शामिल है. रेत के सांचे के विपरीत, ये स्थायी मोल्ड स्टील या लोहे जैसी सामग्रियों से बने होते हैं और इसका उपयोग बार -बार किया जा सकता है.
स्थायी मोल्ड कास्टिंग के अनुप्रयोग
इस विधि का उपयोग अक्सर अच्छे आयामी सटीकता के साथ मध्यम से उच्च-मात्रा वाले भागों के उत्पादन के लिए किया जाता है. सामान्य अनुप्रयोगों में मोटर वाहन भाग शामिल हैं, पंप आवास, और छोटे मशीनरी घटक.
स्थायी मोल्ड कास्टिंग के फायदे और नुकसान
पेशेवरों:
- सहनशीलता: पुन: प्रयोज्य सांचे कम दीर्घकालिक लागत का नेतृत्व करते हैं.
- अच्छी सतह खत्म: रेत कास्टिंग की तुलना में एक बेहतर सतह खत्म के साथ भागों का उत्पादन करता है.
दोष:
- प्रारंभिक लागत: धातु के साँचे बनाने के लिए उच्च टूलींग लागत.
- जटिलता: बहुत जटिल डिजाइन बनाने में कम लचीला.
सामान्य सामग्री का उपयोग किया
अल्युमीनियम, मैगनीशियम, और कुछ मिश्र धातुओं का उपयोग अक्सर स्थायी मोल्ड कास्टिंग में किया जाता है क्योंकि उनकी क्षमता जल्दी और लगातार पुन: प्रयोज्य मोल्ड में ठोस करने की क्षमता के कारण होती है.
#5: शेल कास्टिंग
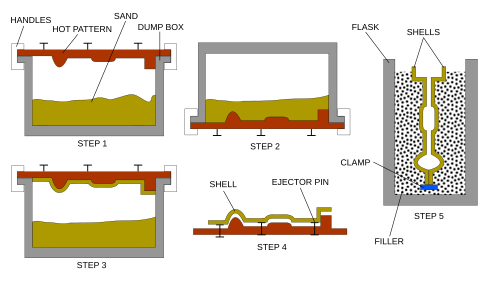
शेल कास्टिंग क्या है?
शेल कास्टिंग, या शेल मोल्ड कास्टिंग, एक पैटर्न के चारों ओर एक पतली सिरेमिक खोल बनाना शामिल है. एक बार शेल कठोर हो जाता है, पैटर्न हटा दिया जाता है, और पिघला हुआ धातु को अंतिम भाग बनाने के लिए गुहा में डाला जाता है.
शेल कास्टिंग के अनुप्रयोग
यह विधि उच्च-सटीक और जटिल भागों के उत्पादन के लिए अच्छी तरह से अनुकूल है, विशेष रूप से एयरोस्पेस और गहने उद्योगों में. यह एक ठीक सतह खत्म और जटिल विवरण की आवश्यकता वाले भागों के लिए आदर्श है.
शेल कास्टिंग के पेशेवरों और विपक्ष
पेशेवरों:
- शुद्धता: जटिल और उच्च-डिटेल भागों के लिए उत्कृष्ट.
- सतही समापन: एक चिकनी प्रदान करता है, उच्च गुणवत्ता वाला समापन.
दोष:
- लागत: सिरेमिक शेल के कारण उच्च प्रारंभिक सेटअप लागत.
- उत्पादन गति: अन्य कास्टिंग विधियों की तुलना में धीमी गति से.
सामान्य सामग्री का उपयोग किया
शेल कास्टिंग का उपयोग आमतौर पर स्टेनलेस स्टील जैसी धातुओं के साथ किया जाता है, अल्युमीनियम, और टाइटेनियम, ठीक मोल्ड विवरण भरने और उच्च गुणवत्ता वाले घटकों का उत्पादन करने की उनकी क्षमता के लिए चुना गया.
#6: अपकेंद्री प्रक्षेप
केन्द्रापसारक कास्टिंग क्या है?
सेंट्रीफ्यूगल कास्टिंग में एक घूर्णन मोल्ड में पिघला हुआ धातु डालना शामिल है. केन्द्रापसारक बल धातु को मोल्ड के बाहरी किनारों पर धकेलता है, घने और समान गुणों के साथ एक ठोस हिस्सा बनाना.
केन्द्रापसारक कास्टिंग के आवेदन
इस विधि का उपयोग पाइप जैसे बेलनाकार भागों बनाने के लिए किया जाता है, ट्यूबों, और बीयरिंग. यह उच्च शक्ति और एकरूपता की आवश्यकता वाले अनुप्रयोगों के लिए आदर्श है, जैसे कि औद्योगिक मशीनरी और निर्माण में.
केन्द्रापसारक कास्टिंग के फायदे और नुकसान
पेशेवरों:
- समान घनत्व: घने में परिणाम, कम दोषों के साथ उच्च गुणवत्ता वाले भाग.
- प्रभावी लागत: लंबे उत्पादन के लिए कुशल, खोखले घटक.
दोष:
- आकार सीमा: मुख्य रूप से बेलनाकार भागों के लिए अनुकूल.
- तिथि लागत: विशिष्ट उपकरण और मोल्ड की आवश्यकता होती है.
सामान्य सामग्री का उपयोग किया
सामान्य सामग्री में कच्चा लोहा शामिल है, इस्पात, और निकल मिश्र धातु, जो उच्च शक्ति वाले भागों का उत्पादन करने के लिए केन्द्रापसारक प्रक्रिया से लाभ की उनकी क्षमता के लिए चुने जाते हैं.
#7: प्लास्टर कास्टिंग
प्लास्टर कास्टिंग क्या है?
प्लास्टर कास्टिंग में प्लास्टर से एक मोल्ड बनाना शामिल है, जो तब पिघला हुआ धातु डालने के लिए उपयोग किया जाता है. यह विधि निवेश कास्टिंग के समान है, लेकिन सिरेमिक शेल के बजाय प्लास्टर का उपयोग करती है.
प्लास्टर कास्टिंग के आवेदन
प्लास्टर कास्टिंग का उपयोग आमतौर पर छोटी मात्रा में विस्तृत और सटीक भागों के उत्पादन के लिए किया जाता है. यह अक्सर कला के टुकड़ों के लिए उपयोग किया जाता है, जेवर, और ठीक विवरणों को पकड़ने की क्षमता के कारण प्रोटोटाइप.
प्लास्टर कास्टिंग के पेशेवरों और विपक्ष
पेशेवरों:
- विवरण: जटिल और विस्तृत भागों के उत्पादन के लिए उत्कृष्ट.
- प्रभावी लागत: कुछ अन्य तरीकों की तुलना में कम टूलींग लागत.
दोष:
- भौतिक सीमाएँ: आम तौर पर कम पिघलने बिंदु धातुओं के लिए उपयोग किया जाता है.
- सहनशीलता: प्लास्टर मोल्ड धातु के मोल्ड के रूप में टिकाऊ नहीं हैं.
सामान्य सामग्री का उपयोग किया
एल्यूमीनियम जैसी सामग्री, पीतल, और कुछ कम-पिघलने-बिंदु मिश्र धातुओं का उपयोग अक्सर प्लास्टर कास्टिंग में प्रक्रिया के साथ उनकी संगतता के लिए किया जाता है.
#8: वैक्यूम कास्टिंग
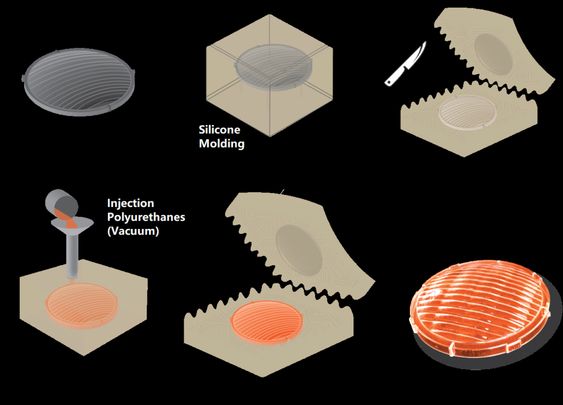
वैक्यूम कास्टिंग क्या है?
वैक्यूम कास्टिंग में हवा और गैसों को हटाने के लिए एक वैक्यूम बनाते समय एक मोल्ड में पिघला हुआ धातु डालना शामिल है. यह विधि दोषों को कम करने और कास्ट भागों की गुणवत्ता में सुधार करने में मदद करती है.
वैक्यूम कास्टिंग के आवेदन
वैक्यूम कास्टिंग उच्च परिशुद्धता और उच्च गुणवत्ता वाले भागों के लिए आदर्श है, अक्सर एयरोस्पेस में उपयोग किया जाता है, ऑटोमोटिव, और इलेक्ट्रॉनिक्स उद्योग. यह उन अनुप्रयोगों के लिए विशेष रूप से उपयोगी है जहां वायु बुलबुले या गैस पोरसिटी भाग की अखंडता से समझौता कर सकते हैं.
वैक्यूम कास्टिंग के फायदे और नुकसान
पेशेवरों:
- उच्च गुणवत्ता: कम दोषों और बेहतर सतह खत्म के साथ भागों का उत्पादन करता है.
- शुद्धता: विस्तृत और जटिल घटकों के लिए उत्कृष्ट.
दोष:
- लागत: वैक्यूम उपकरण और सामग्री से जुड़ी उच्च लागत.
- जटिलता: अन्य कास्टिंग विधियों की तुलना में अधिक जटिल सेटअप और प्रक्रिया.
सामान्य सामग्री का उपयोग किया
वैक्यूम कास्टिंग का उपयोग अक्सर एल्यूमीनियम जैसी सामग्रियों के साथ किया जाता है, स्टेनलेस स्टील, और टाइटेनियम, जो बेहतर गुणवत्ता से लाभान्वित होता है और वैक्यूम प्रक्रिया द्वारा प्रदान की गई पोरसिटी कम हो जाती है.
कास्टिंग विधियों की तुलना
लागत क्षमता
जब लागत की बात आती है, कम टूलींग और सेटअप लागत के कारण सैंड कास्टिंग और प्लास्टर कास्टिंग आम तौर पर अधिक सस्ती होती है. तथापि, डाई कास्टिंग और निवेश कास्टिंग जैसे तरीके, जबकि शुरू में अधिक महंगा है, उनकी दक्षता और स्थिरता के कारण उच्च-मात्रा उत्पादन के लिए लंबे समय में अधिक लागत प्रभावी हो सकता है.
सामग्री उपयुक्तता
विभिन्न कास्टिंग विधियां विभिन्न सामग्रियों के अनुकूल हैं. उदाहरण के लिए, एल्यूमीनियम और जिंक जैसी गैर-फेरस धातुओं के साथ कास्टिंग एक्सेल डाई, जबकि निवेश कास्टिंग मिश्र धातुओं की एक विस्तृत श्रृंखला को संभाल सकती है, उच्च तापमान सामग्री सहित.
सटीक और सटीकता
यदि परिशुद्धता आपकी सर्वोच्च प्राथमिकता है, निवेश कास्टिंग और वैक्यूम कास्टिंग अत्यधिक विस्तृत और सटीक भागों का उत्पादन करने की उनकी क्षमता के कारण उत्कृष्ट विकल्प हैं. वहीं दूसरी ओर, सैंड कास्टिंग और प्लास्टर कास्टिंग कम सटीकता प्रदान कर सकते हैं लेकिन बड़े और कम जटिल भागों को संभालने में अधिक बहुमुखी हैं.
उत्पादन गति
कास्टिंग विधियों के बीच उत्पादन की गति काफी भिन्न होती है. डाई कास्टिंग और सेंट्रीफ्यूगल कास्टिंग को उनकी उच्च गति क्षमताओं के लिए जाना जाता है, उन्हें बड़े उत्पादन रन के लिए उपयुक्त बनाना. इसके विपरीत, निवेश कास्टिंग और शेल कास्टिंग जैसी विधियाँ उनकी जटिल प्रक्रियाओं और विस्तृत मोल्ड आवश्यकताओं के कारण धीमी हो सकती हैं.
सही कास्टिंग विधि चुनना
विचार करने के लिए कारक
सबसे अच्छी कास्टिंग विधि का चयन करते समय, आवश्यक परिशुद्धता जैसे कारकों पर विचार करें, उत्पादन की मात्रा, और सामग्री का प्रकार. प्रत्येक कास्टिंग विधि की अपनी ताकत और सीमाएँ होती हैं, इसलिए इन पहलुओं को समझने से आपको एक सूचित निर्णय लेने में मदद मिलेगी.
सामग्री आवश्यकताएँ
विभिन्न सामग्रियों में विशिष्ट कास्टिंग आवश्यकताएं होती हैं. उदाहरण के लिए, एल्यूमीनियम और जस्ता मरने के लिए अच्छी तरह से अनुकूल हैं, जबकि उच्च तापमान वाले मिश्र धातुओं को उचित भरने और संरचनात्मक अखंडता सुनिश्चित करने के लिए निवेश या वैक्यूम कास्टिंग की आवश्यकता हो सकती है.
वांछित उत्पाद विशेषताओं
अंतिम उत्पाद की विशेषताओं के बारे में सोचें - जैसे कि सतह खत्म, ताकत, और आयामी सटीकता. निवेश कास्टिंग और वैक्यूम कास्टिंग जैसे तरीके विस्तृत के लिए उत्कृष्ट हैं, उच्च परिशुद्धता भागों, जबकि सैंड कास्टिंग बड़े के लिए बेहतर हो सकता है, कम विस्तृत घटक.
लागत संबंधी विचार
बजट की कमी एक कास्टिंग विधि चुनने में महत्वपूर्ण भूमिका निभाती है. यदि आप एक तंग बजट और छोटे उत्पादन के साथ काम कर रहे हैं, सैंड कास्टिंग या प्लास्टर कास्टिंग अधिक किफायती हो सकती है. तथापि, उच्च-मात्रा वाले उत्पादन के लिए जहां दीर्घकालिक लागत दक्षता महत्वपूर्ण है, डाई कास्टिंग और स्थायी मोल्ड कास्टिंग बेहतर निवेश हो सकता है.
निष्कर्ष
सही कास्टिंग विधि का चयन करने से गुणवत्ता पर महत्वपूर्ण प्रभाव पड़ सकता है, लागत, और आपकी विनिर्माण प्रक्रिया की दक्षता. आठ कास्टिंग प्रकारों में से प्रत्येक -कास्टिंग, धातु - स्वरूपण तकनीक, मेटल सांचों में ढालना, स्थायी मोल्ड कास्टिंग, शेल कास्टिंग, अपकेंद्री प्रक्षेप, प्लास्टर कास्टिंग, और वैक्यूम कास्टिंग - अलग -अलग फायदे के रूप में और विभिन्न अनुप्रयोगों के लिए अनुकूल है. इन विकल्पों को समझकर और अपनी परियोजना की विशिष्ट आवश्यकताओं पर विचार करके, आप एक सूचित निर्णय ले सकते हैं जो आपकी कास्टिंग आवश्यकताओं के लिए सर्वोत्तम परिणाम सुनिश्चित करता है.