우리가 내구성이 내구성을 생각할 때, 경량, 복잡한 모양의 금속 성분, 알루미늄 다이 캐스팅은 종종 중심 무대를 차지합니다. 그러나 알루미늄 다이 캐스팅은 정확히 무엇입니까?, 그리고 왜 알루미늄 이이 과정에서 선택한 금속입니까?? 이 매혹적인 제조 방법의 견과류와 볼트에 뛰어 들어 봅시다..
알루미늄 다이캐스팅이란??
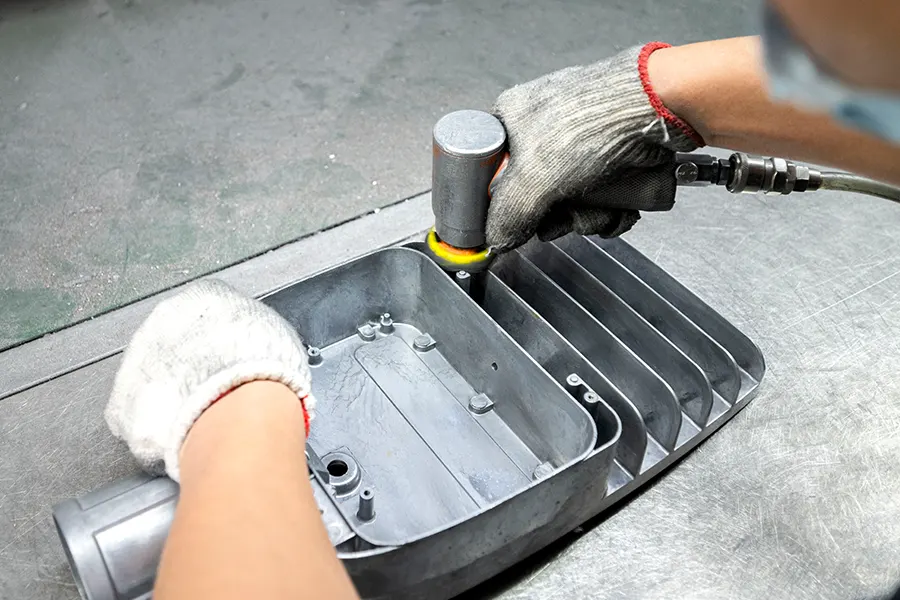
다이 캐스팅. 젤로 곰팡이의 금속 버전을 만드는 것과 같습니다. – 오직, 젤라틴 대신, 우리는 알루미늄을 사용하고 있습니다! 이 방법은 높은 정확도와 복잡한 모양을 생산할 수 있습니다. 표면 마무리.
알루미늄 다이 캐스팅 과정
알루미늄 다이 캐스팅 프로세스에는 몇 가지 주요 단계가 포함됩니다, 곰팡이 준비에서 주조의 방출까지. 분해합시다.
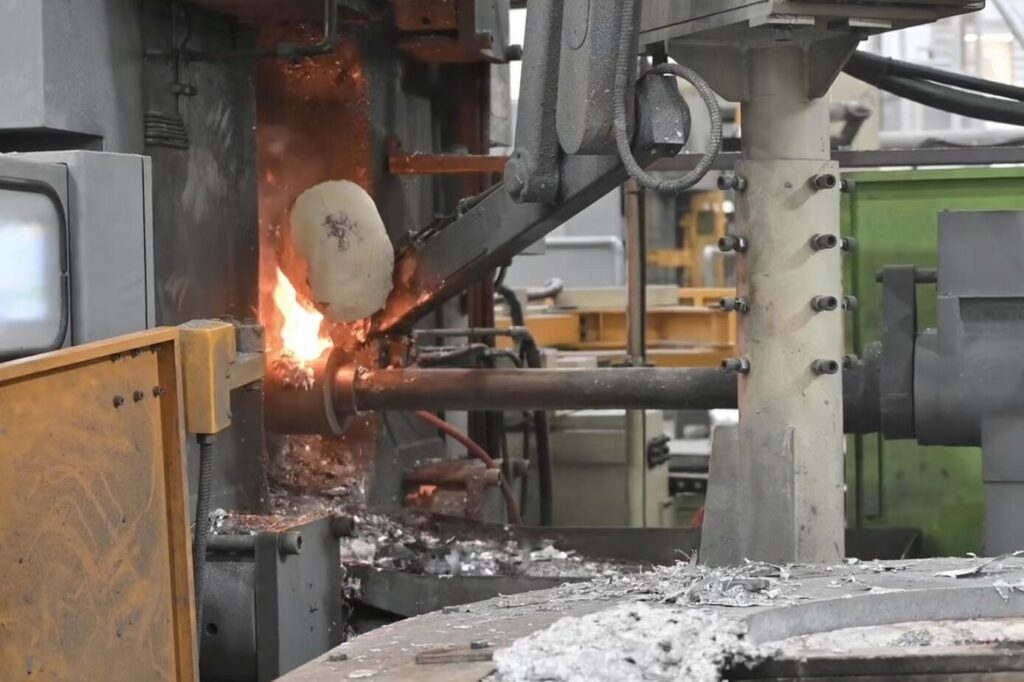
#1: 금형 준비
먼저 먼저, 우리는 곰팡이가 필요합니다. 이 곰팡이, 일반적으로 강철로 만들어졌습니다, 원하는 부분의 정확한 사양에 따라 생성됩니다.. 금속을위한 맞춤형 쿠키 커터를 갖는 것과 같습니다!
#2: 융합 및 주사 알루미늄
금형이 준비되면, 이제 일을 가열 할 때입니다. 알루미늄 잉곳은 용광로에서 녹은 다음 고압 하에서 금형 구멍에 주입됩니다.. 용융 알루미늄을 금속 금형 모양의 풍선에 주입하는 것으로 생각하십시오.!
#3: 냉각 및 응고
알루미늄이 금형에 주입 된 후, 몰드 캐비티의 모양을 취하기 위해 빠르게 식고 굳어집니다.. 이 과정은 당신이 말할 수있는 것보다 빠르게 발생합니다 “알루미늄 응고.”
#4: 캐스팅의 배출
일단 알루미늄이 고형화되면, 새로 형성된 부품이 금형에서 배출됩니다., 다듬을 준비가되었습니다, 완성된, 그리고 일을 시작합니다.
다이 캐스팅에 사용되는 일반적인 알루미늄 합금
알루미늄 다이캐스팅 올바른 합금 없이는 불가능합니다. 다이 캐스팅 과정에 사용되는 가장 일반적인 알루미늄 합금을 살펴 보겠습니다..
알루미늄 합금 380
알루미늄 합금 380 우수한 주파수와 기계적 특성으로 인해 다이 캐스팅에서 가장 널리 사용되는 합금 중 하나입니다.. 그것은 좋은 힘과 경도를 제공합니다, 부식에 대한 탁월한 저항과 함께. 합금 380 복잡한 모양과 얇은 벽이 필요한 부품에 종종 사용됩니다., 다양한 산업에서 인기있는 선택입니다, 자동차 및 소비자 전자 장치를 포함하여.
알루미늄 합금 383
알루미늄 합금 383 합금과 유사합니다 380 그러나 뜨거운 균열에 대한 저항성이 향상되었습니다, 특히 고온을 포함하는 다이 캐스팅 응용 프로그램에 특히 적합합니다.. 유동성이 우수하며 종종 우수한 표면 마감과 치수 안정성이 필요한 구성 요소에 사용됩니다..
알루미늄 합금 360
알루미늄 합금 360 높은 부식성과 탁월한 압력 압박감으로 유명합니다.. 우수한 유동성과 연성이 필요한 부품에 일반적으로 사용됩니다., 전기 부품 및 배관 공구의 하우징과 같은. 합금 360 또한 가공 가능합니다, 사후 캐스팅 가공 작업이 필요한 부품에 적합합니다..
알루미늄 합금 390
알루미늄 합금 390 탁월한 내마모성과 치수 안정성을 가진 고강도 합금입니다.. 높은 기계적 특성이 필요한 부품에 종종 사용됩니다., 자동차 및 항공 우주 응용 분야의 엔진 구성 요소 및 구조 부품과 같은. 합금 390 우수한 주파수를 제공하고 얇은 벽으로 복잡한 모양을 생산하는 데 적합합니다..
알루미늄 다이 캐스팅의 유형
이제 우리는 프로세스를 이해합니다, 알루미늄 다이 캐스팅의 두 가지 주요 유형을 살펴 보겠습니다.: 뜨거운 챔버와 차가운 챔버 다이 캐스팅.
핫 챔버 다이 캐스팅
핫 챔버 다이 캐스팅에서, 주사 시스템은 용융 금속 욕조에 담겨 있습니다.. 이 과정은 녹는 점이 낮은 금속에 이상적입니다., 아연, 마그네슘과 같은. 그것은 버블 링 가마솥에서 금속 마법을 만드는 것과 같습니다!
콜드 챔버 다이 캐스팅
콜드 챔버 다이 캐스팅, 반면에, 용융 금속을 차가운 챔버에 담그기 전에 곰팡이에 주입합니다.. 이 방법은 녹는 점이 높은 금속에 선호됩니다., 알루미늄이나 구리와 같은. 액체 금속을 대기 금형에 조심스럽게 붓는 것과 같습니다..
알루미늄 다이 캐스팅 기계의 유형
다이 캐스팅 기계는 다이 캐스팅 과정과 관련된 고압과 온도를 견딜 수 있도록 설계되었습니다.. 그들은 다양한 모양과 크기로 제공됩니다, 각각은 다른 생산 요구에 적합합니다. 다이 캐스팅 머신에는 세 가지 주요 유형이 있습니다:
- 수평 차가운 챔버 기계: 이 기계는 대량 생산에 이상적이며 자동차 및 항공 우주와 같은 산업에서 일반적으로 사용됩니다..
- Vertical Cold Chamber Machines: Vertical cold chamber machines are used for smaller production runs and offer greater flexibility in terms of mold size and configuration.
- Horizontal Hot Chamber Machines: They are best suited for metals with low melting points and are often used for zinc and magnesium die casting applications.
Key Components of an Aluminum Die Casting Machine
Now that we know the types of machines used, let’s delve into the key components that make them tick.
Injection Unit
The injection unit is responsible for melting the metal and injecting it into the mold cavity under high pressure. It’s like the beating heart of the die casting machine, pumping molten metal into the waiting mold.
Clamping Unit
The clamping unit holds the two halves of the mold together under immense pressure during the casting process. It’s like the strong arms that keep everything in place while the magic happens.
Hydraulic System
The hydraulic system provides the power needed to operate the various components of the die casting machine. It’s like the muscles that power the entire operation, ensuring everything runs smoothly.
Advantages of Aluminum Die Casting
Now that we have a solid understanding of how aluminum die casting works, let’s explore some of its key advantages.
높은 강도 대 중량비
Aluminum die cast parts offer an excellent strength-to-weight ratio, making them ideal for applications where weight savings are crucial, such as in the automotive and aerospace industries.
치수 정확도
다이 캐스팅 과정의 정확성 덕분에, 알루미늄 부품은 타이트한 공차와 높은 차원 정확도로 생산할 수 있습니다., 매번 완벽한 착용감을 보장합니다.
고속 생산
알루미늄 다이 캐스팅은 비교적 짧은 시간 내에 다량의 부품을 생산할 수있는 매우 효율적인 프로세스입니다.. 그것은 제조 공정의 Usain 볼트와 같습니다!
비용 효율성
많은 이점에도 불구하고, 알루미늄 다이 캐스팅은 비용 효율적인 제조 솔루션으로 남아 있습니다, 다른 생산 방법에 비해 상당한 비용을 절감합니다, 특히 대량의 생산에 대한 경우.
복잡한 모양과 얇은 벽
알루미늄 다이 캐스팅의 가장 중요한 장점 중 하나는 복잡한 형상과 얇은 벽을 가진 부품을 생산하는 능력이 없으며 다른 방법을 사용하여 달성하기에는 불가능하거나 엄청나게 비쌉니다..
알루미늄 다이 캐스팅의 응용
이제 우리는 왜 알루미늄이 바위를 캐스팅하는지 알았습니다, 다양한 산업 분야에서 가장 일반적인 응용 프로그램을 살펴 보겠습니다..
자동차 산업
엔진 구성 요소에서 변속기 부품까지, 알루미늄 다이 캐스팅은에서 중요한 역할을합니다 자동차 산업, 가벼운 곳, 내구성 부품은 연료 효율과 성능에 필수적입니다.
가전제품
세계에서 가전제품, 알루미늄 다이 캐스팅, 스타일과 내구성을 보장합니다.
항공우주 산업
항공 우주 응용 프로그램에서, 체중이 중요한 요소 인 경우, 알루미늄 다이 캐스팅.
의료 장비
의료 산업에서, 알루미늄 다이 캐스팅은 광범위한 구성 요소를 생산하는 데 사용됩니다., 수술 기기에서 의료 기기까지, 정밀도와 신뢰성이 가장 중요합니다.
산업 기계
펌프 및 밸브에서 기어 박스 및 하우징까지, 알루미늄 다이 캐스팅은 산업 기계 부문에서 고품질을 생산하는 데 널리 사용됩니다., 까다로운 작동 조건을 견딜 수있는 내구성있는 구성 요소.
알루미늄 다이 캐스팅의 품질 관리
엄격한 품질 관리 표준 유지 알루미늄 다이 캐스트 부품의 무결성과 일관성을 보장하는 데 필수적입니다.. 몇 가지 일반적인 품질 관리 조치를 살펴 보겠습니다.
검사 방법
육안 검사에서 고급 비파괴 테스트 기술에 이르기까지, 다이 캐스트 부품의 품질과 무결성을 확인하는 데 다양한 검사 방법이 사용됩니다..
결함과 예방
알루미늄 다이 캐스팅의 일반적인 결함, 다공성과 같은, 수축, 그리고 춥습니다, 적절한 프로세스 제어를 통해 최소화 할 수 있습니다, 재료 선택, 설계 최적화.
올바른 알루미늄 다이 캐스팅 제조업체 선택
너무 많은 다이 캐스팅 제조업체와 함께, 올바른 것을 선택하는 것은 어려운 일이 될 수 있습니다. 다음은 제조업체를 선택할 때 고려해야 할 몇 가지 주요 요소입니다..
경험과 전문성
알루미늄 다이 캐스팅에서 성공한 결과와 광범위한 경험에 대한 입증 된 실적을 가진 제조업체를 찾으십시오.. 프로세스의 내부를 아는 회사는 사양을 충족하는 고품질 부품을 제공 할 가능성이 높습니다..
품질 인증
확인하십시오 다이 캐스팅 제조업체 ISO와 같은 산업 표준에 인증되었습니다 9001 및 IATF 16949, 품질과 지속적인 개선에 대한 그들의 헌신을 보여줍니다.
고객 리뷰
제조업체의 명성과 고객 만족도 수준을 이해하려면 고객 리뷰 및 평가를 확인하십시오.. 과거 고객의 확실한 명성과 긍정적 인 피드백을 가진 제조업체는 귀하의 기대를 충족시킬 가능성이 높습니다..
결론
결론적으로, 알루미늄 다이 캐스팅. 높은 정확도로 복잡한 모양을 생산하는 능력에서 다양한 산업 분야의 광범위한 응용 프로그램에 이르기까지, 알루미늄 다이 캐스팅은 계속해서 재생됩니다