Wenn Sie in Ihr Auto steigen, Man vergisst leicht, wie viele Spezialteile für eine reibungslose Fahrt erforderlich sind, sicher, und zuverlässig. Aber hinter jedem eleganten Fahrzeug steckt eine Reihe von Teilen, die im Druckgussverfahren hergestellt werden – einem fortschrittlichen Herstellungsverfahren, das für die Automobilproduktion unerlässlich ist. Wenn Sie sich jemals gefragt haben, wie einige der härtesten sind, am leichtesten, und es werden hochpräzise Bauteile gefertigt, Druckguss ist die geheime Zutat. Lassen Sie uns genauer untersuchen, was Automobildruckguss ist, die verwendeten Materialien, welche Vorteile es mit sich bringt, und einige wichtige Beispiele für Automobil-Druckgussprodukte.
Was ist Druckguss??
Im Kern, Druckguss ist eine Methode zur Herstellung von Metallteilen, bei der geschmolzenes Metall unter hohem Druck in eine Form gepresst wird. Stellen Sie sich vor, Sie drücken Zahnpasta aus einer Tube, außer in diesem Fall, Dabei handelt es sich um heißes flüssiges Metall, das in komplizierte Formen gespritzt wird, um komplexe Formen zu bilden.
In der Automobilindustrie, Zur Herstellung wird Druckguss verwendet Druckguss-Automobilteile die leicht sind, dauerhaft, und sehr detailliert. Diese Teile müssen den härtesten Bedingungen standhalten, vom Motorblock bis zum Getriebegehäuse, und Druckguss macht es möglich, dies effizient zu tun. Es ist, als hätte man das perfekte Rezept für Präzision und Stärke.
Gängige Arten von Materialien, die in der Automobilindustrie verwendet werden Druckguss
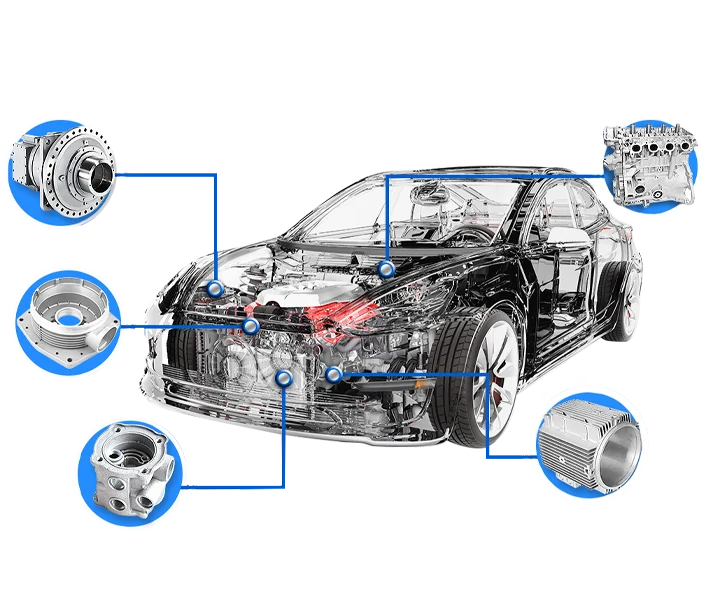
Aluminium-Druckguss
Gussteile auf Aluminiumbasis werden im Automobilsektor aufgrund ihres Verhältnisses von Festigkeit zu Gewicht bevorzugt, Das bedeutet, dass Sie ein robustes Teil erhalten, das das Fahrzeug nicht unnötig belastet. Denken Sie darüber nach: Heutige Autos müssen sowohl robust als auch leicht sein, um die Kraftstoffeffizienz zu verbessern, und Automobilkomponenten aus Aluminium kreuzen beide Kästchen an. Vom Motorblock bis zum Rad, Autoteile aus Aluminiumdruckguss sind ein wesentlicher Bestandteil des modernen Automobildesigns. Sie werden in kritischen Motorkomponenten eingesetzt, Damit spielen sie eine wichtige Rolle bei der Verbesserung der Fahrzeugleistung und senken gleichzeitig den Kraftstoffverbrauch.
Vorteile von Autoteilen aus Aluminiumdruckguss
- Leicht: Aluminium ist ein leichtes Metall, trägt dazu bei, das Gesamtgewicht des Fahrzeugs zu reduzieren, was die Kraftstoffeffizienz und Leistung verbessert.
- Stärke und Haltbarkeit: Aluminiumdruckgussteile für die Automobilindustrie sind robust und halten hohen Temperaturen und starkem Verschleiß stand, Damit sind sie ideal für Automobilanwendungen.
- Korrosionsbeständigkeit: Aluminium ist von Natur aus korrosionsbeständig, Dies erhöht die Langlebigkeit und Zuverlässigkeit von Automobilteilen, insbesondere unter rauen Bedingungen.
- Designflexibilität: Druckguss ermöglicht komplexe und komplizierte Formen, Dadurch können Hersteller Teile mit dünnen Wänden und präzisen Abmessungen herstellen.
- Kostengünstige Produktion: Das Druckgussverfahren ist für die Massenproduktion äußerst effizient, Reduzierung sowohl des Materialabfalls als auch der gesamten Herstellungskosten.
Zinkdruckguss
Zink ist möglicherweise nicht das erste Material, an das Sie denken, Aber auch im Automobilgussbereich erfreut es sich großer Beliebtheit. Zinkdruckgussprodukte sind für ihre Langlebigkeit und Vielseitigkeit bekannt. Während Zink häufig in kleineren Teilen wie Verriegelungsmechanismen oder Anschlüssen verwendet wird, Es ist von entscheidender Bedeutung für Automobilhersteller, die Präzision und Festigkeit ihrer Komponenten benötigen.
Vorteile von Autoteilen aus Zinkdruckguss
- Hohe Festigkeit: Zinkdruckgussteile bieten eine hervorragende Festigkeit und Zähigkeit, Damit eignen sie sich ideal für Automobilkomponenten, die Belastungen und Stößen standhalten müssen.
- Präzision und Detail: Zink ermöglicht enge Toleranzen und komplizierte Designs, Sicherstellen, dass Teile in komplexen Automobilsystemen genau passen und wie vorgesehen funktionieren.
- Kostengünstig: Zink ist günstiger als viele andere Metalle, und das Druckgussverfahren ist für die Produktion großer Stückzahlen äußerst effizient, Dies macht es zu einer kostengünstigen Option für Automobilhersteller.
- Hervorragende Oberflächenbeschaffenheit: Zinkdruckgussteile haben eine glatte Oberfläche, poliertes Finish, Dadurch wird der Bedarf an zusätzlichen Nachbearbeitungsprozessen reduziert und das Gesamterscheinungsbild der Komponenten verbessert.
- Korrosionsbeständigkeit: Zink verfügt über inhärente korrosionsbeständige Eigenschaften, Dadurch eignet es sich gut für Automobilteile, die Feuchtigkeit und rauen Umgebungsbedingungen ausgesetzt sind, Gewährleistung einer längeren Lebensdauer.
Magnesiumdruckguss
Über Magnesium wird möglicherweise nicht so häufig gesprochen, Aber es ist eines der leichtesten verfügbaren Strukturmetalle, Damit eignet es sich ideal für Automobilanwendungen, bei denen Gewichtsreduzierung von entscheidender Bedeutung ist. Automobilteile aus Magnesiumdruckguss erfreuen sich zunehmender Beliebtheit, insbesondere in Hochleistungs- und Elektrofahrzeugen, da die Gewichtsreduzierung zur Energieeffizienz und Batterielebensdauer beiträgt.
Vorteile von Autoteilen aus Magnesiumdruckguss
- Leicht: Magnesium ist das leichteste Strukturmetall, was das Gesamtgewicht des Fahrzeugs deutlich reduziert, Verbesserung der Kraftstoffeffizienz und Leistung.
- Hohes Verhältnis von Festigkeit zu Gewicht: Obwohl es leicht ist, Magnesium bietet eine starke strukturelle Integrität, Damit eignet es sich perfekt für Hochleistungs-Automobilkomponenten.
- Wärmeleitfähigkeit: Magnesium verfügt über hervorragende Wärmeableitungseigenschaften, Dies ist entscheidend für Automobilteile wie Motorkomponenten, die hohen Temperaturen standhalten müssen.
- Verbesserte Sicherheit: Magnesiumteile sind stark und dennoch leicht, trägt zu einer besseren Handhabung bei, Bremsen, und Gesamtsicherheit des Fahrzeugs durch Absenkung des Schwerpunkts.
- Recyclingfähigkeit: Wie Aluminium, Magnesium ist recycelbar, Dies macht es zu einer umweltfreundlichen Option für eine nachhaltige Automobilherstellung.
Andere beim Druckguss verwendete Materialien
Während Aluminium, Zink, und Magnesium sind die am häufigsten verwendeten Druckgussmaterialien, Druckgusshersteller gelegentlich Kupfer verwenden, führen, Zinn, und sogar Stahl in ihren Druckgussprozessen, abhängig von den spezifischen Anforderungen des Teils. Kupferlegierungen, Zum Beispiel, werden häufig in Teilen verwendet, die hohen Temperaturen standhalten müssen.
Beispiele für Druckguss-Automobilteile
Druckguss ist für die Herstellung einiger der wichtigsten Teile Ihres Autos verantwortlich. Werfen wir einen Blick auf einige wichtige Beispiele dafür, wie Druckguss bei Automobilteilen eine Rolle spielt.
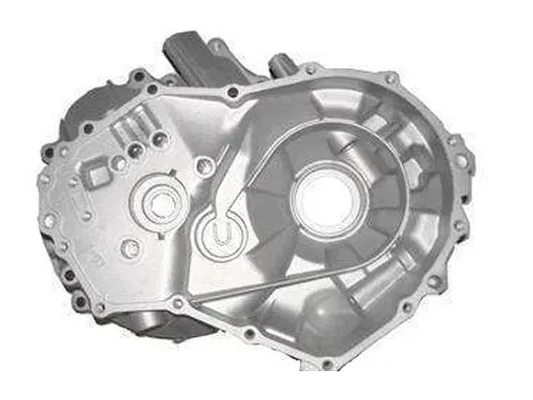
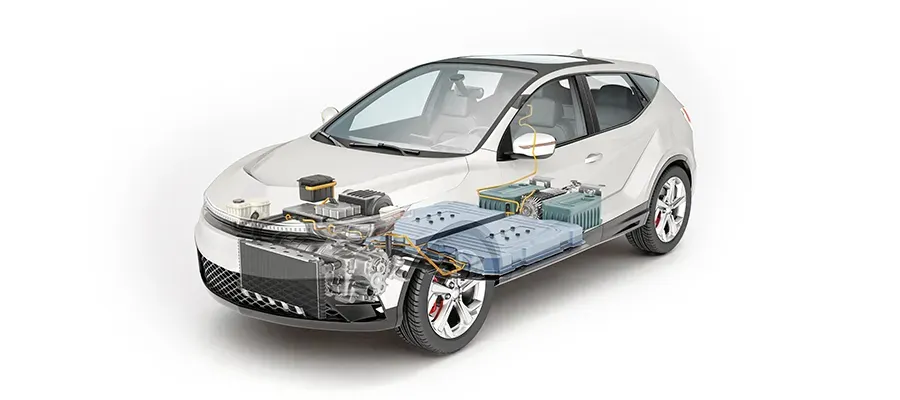
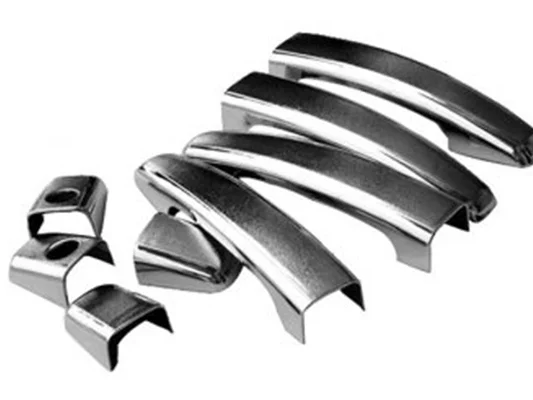
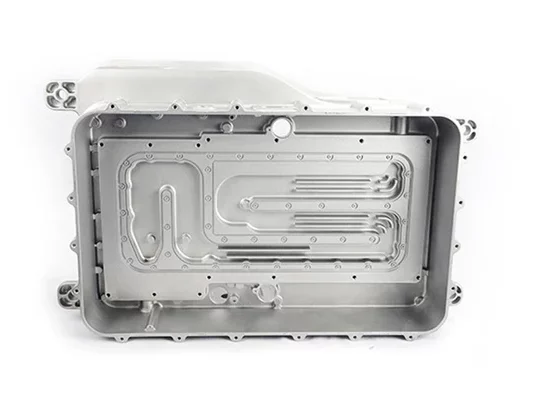
Motorkomponenten
Besonders wertvoll ist Druckguss bei Motorkomponenten. Autoteile aus Aluminiumdruckguss, wie Zylinderköpfe und Motorblöcke, sind leicht und dennoch unglaublich langlebig. Diese Teile müssen extremen Temperaturen und Drücken standhalten, Und Druckguss sorgt dafür, dass dies der Fall ist.
Getriebeteile
Getriebeteile, einschließlich Getriebe und Gehäuse, profitieren Sie stark von der Präzision, die der Druckguss bietet. Druckguss-Automobilteile ermöglichen komplexe Konstruktionen, die den ständigen Schaltvorgängen und Belastungen eines Getriebes standhalten.
Strukturteile
Klammern, Gehäuse, Auch Rahmenteile werden üblicherweise im Druckgussverfahren hergestellt. Diese Teile müssen viel Belastung und Stößen standhalten, Durch Druckguss können Hersteller Teile herstellen, die sowohl stabil als auch leicht sind – entscheidend für die Gesamtleistung des Fahrzeugs.
Andere Automobilteile
Von Rädern über Beleuchtungsgehäuse bis hin zu Kupplungskomponenten, Druckguss spielt auch bei der Herstellung vieler kleinerer, aber ebenso wichtiger Teile, aus denen die Systeme eines Fahrzeugs bestehen, eine Rolle.
Vorteile des Druckgusses in der Automobilindustrie
Also, Warum setzt die Automobilindustrie so stark auf Druckguss?? Also, Die Vorteile sind schwer zu ignorieren.
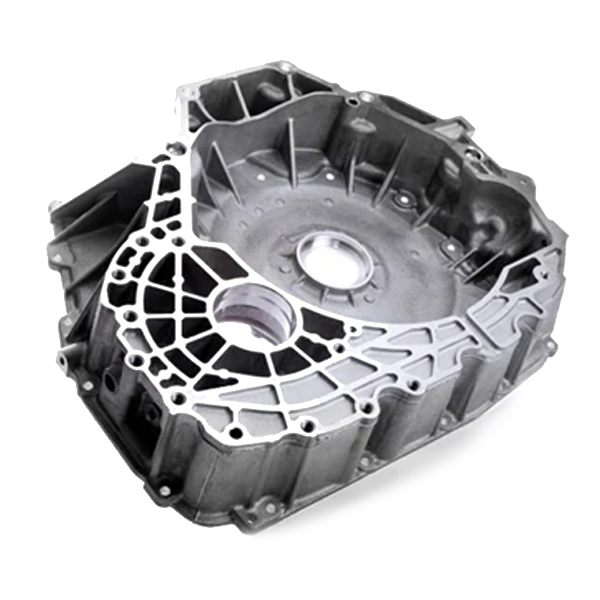
Präzision und Detail
Einer der Hauptgründe für den Einsatz von Druckguss im Automobilbau ist seine Fähigkeit, Teile mit engen Toleranzen und komplizierten Designs herzustellen. Diese Präzision ist in der Automobilwelt unerlässlich, Dabei muss auch das kleinste Bauteil perfekt passen und einwandfrei funktionieren.
Haltbarkeit und Stärke
Druckgussprodukte sind auf Langlebigkeit ausgelegt. Ob es sich um ein Aluminiumlegierungsteil oder einen Magnesiumrahmen handelt, Diese Komponenten müssen extremen Belastungen standhalten, Temperaturschwankungen, und tragen. Das Druckgussverfahren stellt sicher, dass jedes Teil stabil ist und den Strapazen der Straße standhält.
Leicht und effizient
Druckguss bietet einen erheblichen Vorteil hinsichtlich der Gewichtsreduzierung. Da Autos leichter werden, Sie verbrauchen weniger Kraftstoff und sind leistungsfähiger. Gussteile auf Aluminiumbasis, insbesondere, sind großartig darin, Dinge leicht zu halten, ohne die Festigkeit zu beeinträchtigen.
Kosteneffizienz und Skalierbarkeit
Druckguss ist für die Massenproduktion äußerst effizient. Sobald eine Form erstellt ist, Der Prozess kann im großen Maßstab wiederholt werden, Reduzierung der Kosten pro Teil. Das ist perfekt für die Automobilindustrie, das Tausende produzieren muss (oder sogar Millionen) von Teilen auf konsistenter Basis.
Der Druckgussprozess im Automobilbau
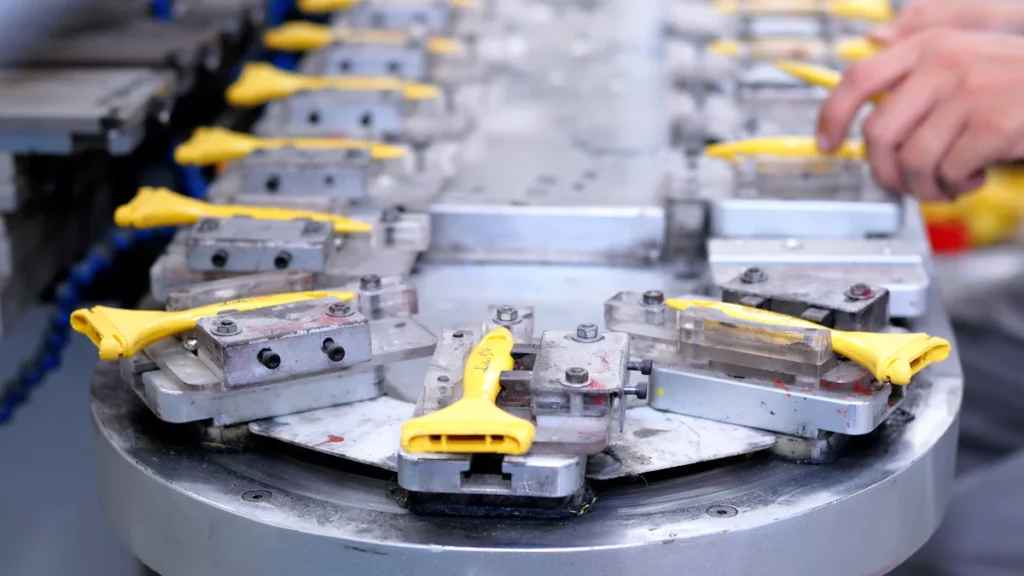
Schritte des Gießprozesses
Der Druckgussprozess umfasst mehrere wichtige Schritte: Formenbau, Metallinjektion, Kühlung, und Auswurf. Nachdem die Form entworfen und erstellt wurde, geschmolzenes Metall (oft Aluminium) wird unter hohem Druck in die Form eingespritzt. Nach dem Abkühlen, Das Teil wird ausgeworfen, und der Prozess beginnt von vorne.
Automatisierung im Druckguss
Einer der Gründe, warum Druckguss so beliebt geworden ist, ist seine Automatisierung. Automatisierung im Druckguss trägt zur Gewährleistung der Präzision bei, Wiederholbarkeit, und Geschwindigkeit. Dies ist im Automobilbau von entscheidender Bedeutung, wo Fristen und Qualitätskontrolle entscheidend sind.
Herausforderungen beim Druckguss für Automobilteile
Dabei bietet Druckguss viele Vorteile, es ist nicht ohne Herausforderungen. Der Prozess kann teuer sein, insbesondere wenn es um komplexe Formen oder hochwertigere Materialien geht. Zusätzlich, Qualitätskontrolle ist von größter Bedeutung – sicherzustellen, dass jedes Teil die erforderlichen Spezifikationen erfüllt, kann schwierig sein, insbesondere bei hochpräzisen Bauteilen.
Abschluss
Druckguss ist aus der Automobilfertigung nicht mehr wegzudenken. Die Kombination aus hoher Präzision, Stärke, und die dadurch erzielte Effizienz haben es der Automobilindustrie ermöglicht, komplexe und leichte Komponenten herzustellen, die für moderne Fahrzeuge unerlässlich sind. Ob es darum geht, Gewicht zu reduzieren, Verbesserung der Haltbarkeit, oder komplizierte Designs erstellen, Druckguss-Automobilteile spielen auch in Zukunft eine entscheidende Rolle in der Automobilwelt.
FAQs
- Welches Material wird am häufigsten im Automobildruckguss verwendet?? Aluminium ist das am häufigsten verwendete Material, dank seines Festigkeit-Gewichts-Verhältnisses und seiner Kosteneffizienz.
- Warum wird Aluminium für Automobilteile verwendet?? Aluminium ist leicht, dauerhaft, und korrosionsbeständig, Damit eignet es sich perfekt für Automobilkomponenten, die unter harten Bedingungen funktionieren müssen.
- Welche Automobilteile werden typischerweise aus Druckguss hergestellt?? Motorblöcke, Getriebeteile, Strukturbauteile, Räder, und Beleuchtungsgehäuse sind nur einige Beispiele für Automobil-Druckgussprodukte.
- Wie verbessert Druckguss die Kraftstoffeffizienz?? Durch die Herstellung von Leichtbauteilen, Druckguss trägt dazu bei, das Gesamtgewicht des Fahrzeugs zu reduzieren, was zu einer besseren Kraftstoffeffizienz führt.
- Ist Druckguss für die Massenproduktion in der Automobilindustrie geeignet?? Ja, Druckguss ist aufgrund seiner hohen Geschwindigkeit perfekt für die Massenproduktion geeignet, Präzision, und Wirtschaftlichkeit.