¿Alguna vez te has preguntado qué aleación de aluminio elegir para tu próximo proyecto?? Bien, no estas solo. Hoy, Nos sumergimos en el meollo de la cuestión de dos aleaciones de aluminio populares.: ADC10 y ADC12. Ambos tienen sus ventajas y peculiaridades únicas., y comprenderlos puede ayudarle a tomar una decisión informada. Entonces, vayamos al grano (o debería decir tachuelas de aluminio?).
¿Qué es la aleación de aluminio ADC10??
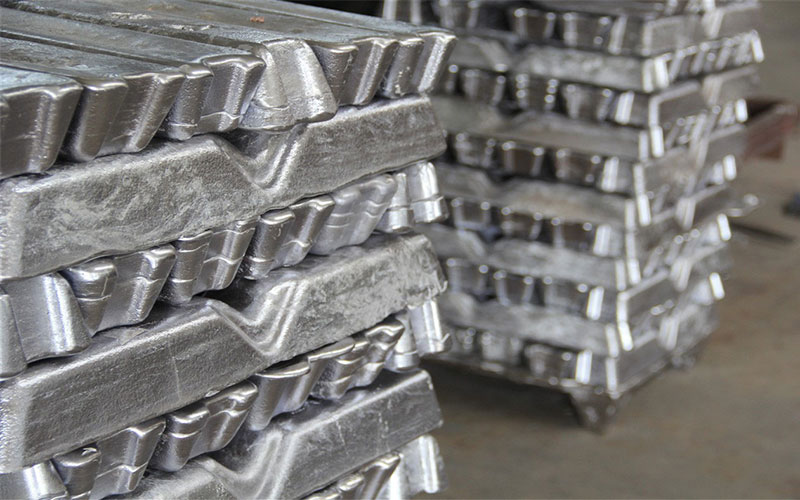
Está bien, comencemos con ADC10. Esta aleación es una especie de caballo de batalla en el fundición a presión de aluminio. Es conocido por sus sólidas propiedades mecánicas y buena conductividad térmica.. Piense en ADC10 como ese amigo confiable que siempre está ahí cuando lo necesita, proporcionando un rendimiento constante y sin decepcionarte. Se utiliza comúnmente en piezas de automóviles., componentes electricos, y aplicaciones de ingeniería general donde la robustez es clave.
¿Qué es la aleación de aluminio ADC12??
Siguiente, ADC12. Esta es una especie de estrella en el mundo de la fundición a presión de aluminio.. Tiene una habilidad especial para los detalles, haciéndolo perfecto para diseños complejos y piezas de precisión. ADC12 es como el artista del grupo., con excelente moldeabilidad y resistencia a la corrosión, lo que significa que fluye mejor en los moldes y se mantiene bien con el tiempo.. A menudo encontrará ADC12 en carcasas electrónicas y piezas automotrices de alto rendimiento..
Pros y contras de la aleación de aluminio ADC10
Ventajas de la aleación de aluminio ADC10
- Propiedades mecánicas sólidas: ADC10 cuenta con una impresionante resistencia a la tracción y límite elástico, lo que lo hace ideal para piezas que necesitan resistir tensiones.
- Buena conductividad térmica: Es genial para disipar el calor., lo cual es una ventaja para los componentes que generan mucho calor.
- Versatilidad: Adecuado para una amplia gama de aplicaciones, desde automoción hasta piezas eléctricas..
Contras de la aleación de aluminio ADC10
- Castabilidad: Si bien es bueno, no es el mejor. ADC10 no fluye tan suavemente en moldes complejos como ADC12.
- Resistencia a la corrosión: Es decente pero no tan alto como ADC12., Lo que podría ser importante en ambientes más corrosivos..
Pros y contras de la aleación de aluminio ADC12
Ventajas de la aleación de aluminio ADC12
- Excelente moldeabilidad: ADC12 fluye como un sueño en moldes intrincados, haciéndolo perfecto para componentes detallados y precisos.
- Alta resistencia a la corrosión: Resiste bien los elementos., Lo cual es ideal para piezas expuestas a condiciones duras..
- Buenas propiedades mecánicas: Aunque ligeramente inferior a ADC10, sus resistencias a la tracción y al rendimiento siguen siendo encomiables.
Contras de la aleación de aluminio ADC12
- Conductividad térmica: No tan alto como ADC10, lo que podría ser un inconveniente para aplicaciones de disipación de calor.
- Fuerza ligeramente menor: Es fuerte pero no alcanza las altas calificaciones del ADC10 en términos de resistencia mecánica..
ADC10 frente a. ADC12 Aluminio
ADC10 y ADC12 son aleaciones de fundición a presión de aluminio comúnmente utilizadas en la fabricación debido a sus propiedades favorables.. Aquí hay una comparación de los dos.:
Criterios | ADC10 | ADC12 |
Composición | Contiene un poco más de silicio. (Y) y hierro (fe) | Normalmente tiene un porcentaje ligeramente mayor de cobre. (Cu) |
Resistencia a la tracción | Alrededor 310 MPa | Alrededor 290 MPa |
Fuerza de producción | Aproximadamente 140 MPa | Aproximadamente 130 MPa |
Dureza (Brinell) | Acerca de 85 media pensión | Acerca de 80 media pensión |
Alargamiento | Normalmente alrededor 3% | Alrededor 2.5% |
Castabilidad | Buena castabilidad, pero no tan fluido en moldes complejos | Mejor moldeabilidad, preferido para fundición compleja |
Resistencia a la corrosión | Resistencia a la corrosión decente | Generalmente exhibe una mejor resistencia a la corrosión. |
Conductividad térmica | Conductividad térmica ligeramente mejor, disipación de calor eficiente | Menor conductividad térmica en comparación con ADC10 |
Aplicaciones | Piezas de automóviles, componentes electricos, ingenieria general | Alta precisión y diseños complejos., carcasas electrónicas, piezas automotrices de alto rendimiento |
Costo | Generalmente no hay diferencia de precio significativa | Generalmente no hay diferencia de precio significativa |
para resumir:
- ADC10: Propiedades mecánicas ligeramente mejores., conductividad térmica, y bueno para aplicaciones que requieren robustez.
- ADC12: Mejor moldeabilidad y resistencia a la corrosión., ideal para aplicaciones complejas y de alta precisión.
Conclusión
La elección entre aleaciones de aluminio ADC10 y ADC12 se reduce a lo que necesita para su proyecto específico. ¿Estás buscando fuerza y control del calor?? Opte por ADC10. Necesita algo para fundición detallada y resistencia a la corrosión.? ADC12 es tu amigo. Ambas aleaciones aportan sus propios puntos fuertes., y conocerlos puede ayudarle a elegir el material perfecto para sus necesidades..
Preguntas frecuentes
- ¿Cuál es la principal diferencia entre el aluminio ADC10 y ADC12?? La principal diferencia radica en sus propiedades.: ADC10 tiene mejor resistencia mecánica y conductividad térmica., mientras que ADC12 ofrece una capacidad de fundición y resistencia a la corrosión superiores.
- ¿Qué aleación es mejor para aplicaciones automotrices?? Depende de la aplicación específica.. ADC10 es mejor para piezas que requieren resistencia y disipación de calor, mientras que ADC12 se prefiere para complejos, piezas resistentes a la corrosión.
- ¿Cómo afecta la composición de ADC10 y ADC12 a sus propiedades?? ADC10 generalmente tiene más silicio y hierro, mejorando su resistencia y propiedades térmicas. ADC12 tiene más cobre, mejorando su moldeabilidad y resistencia a la corrosión.
- ¿Existen diferencias de costos significativas entre ADC10 y ADC12?? Típicamente, No hay una gran diferencia de costo entre las dos aleaciones.. La elección suele depender más de las necesidades específicas del proyecto que del coste..
- ¿Cuáles son las aplicaciones comunes del aluminio ADC10 y ADC12?? ADC10 se usa comúnmente en piezas de automóviles., componentes electricos, y aplicaciones generales de ingeniería. ADC12 es el preferido para carcasas electrónicas, piezas automotrices de alta precisión, y otras piezas fundidas intrincadas.