Le moulage sous pression d'aluminium est un procédé de fabrication très efficace. Cela nous permet de façonner le métal en formes complexes avec une précision extrême.. Mais voici le kicker: malgré ses avantages, des défauts dans la coulée du métal peuvent se faufiler, causant une tonne de maux de tête. Si vous avez déjà été confronté à des défauts de moulage sous pression en aluminium, vous saurez à quel point cela peut être frustrant et coûteux. Mais ne t'en fais pas! Nous sommes sur le point de plonger dans les défauts de fonderie d’aluminium les plus courants, qu'est-ce qui les cause, et, surtout, comment les éviter.
Défauts courants de moulage sous pression en aluminium
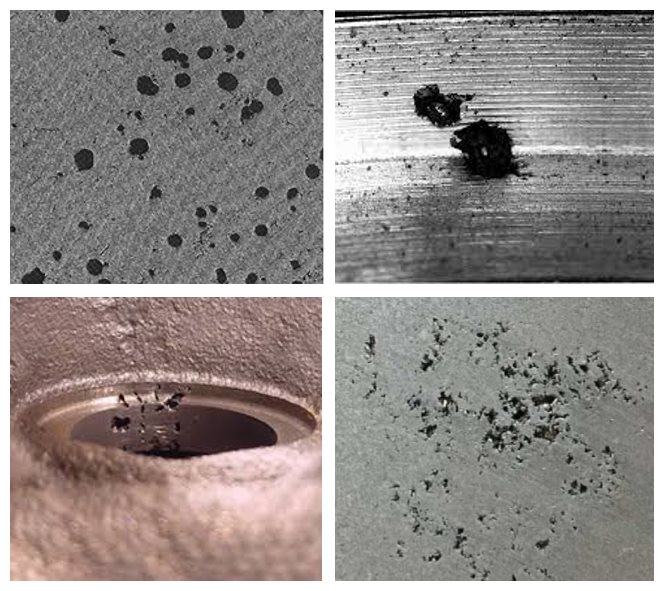
1. Porosité
La porosité est le fauteur de troubles invisible du processus de moulage sous pression. C'est comme les petites poches d'air qui se forment lorsqu'une éponge remonte. On ne peut pas toujours le voir en surface, mais c'est là, affaiblir la structure.
Causes de porosité
- Le piégeage du gaz est le principal coupable. Lorsque de l'air ou d'autres gaz sont piégés dans le métal en fusion pendant la coulée, ils forment des vides.
- Le retrait pendant le refroidissement est une autre cause. Alors que le métal se solidifie, il se contracte, laissant de minuscules vides si le matériau n’est pas uniformément réparti.
Comment éviter la porosité
L’astuce pour éviter la porosité réside dans les détails. Optimisez la conception de la coulée pour permettre un écoulement fluide du métal et assurez-vous que les niveaux de gaz sont contrôlés pendant le processus.. Utiliser les bons alliages peut également réduire les risques de porosité.
2. Fermetures à froid
Ah, le redoutable froid s'est arrêté au casting! Cela se produit lorsque deux flux de métal en fusion se rencontrent mais ne parviennent pas à fusionner correctement., laissant une couture visible. Considérez-le comme deux pièces de puzzle qui ne cliquent pas.
Causes des arrêts à froid
- Une basse température du métal provoque souvent ce problème. Si le métal en fusion n'est pas assez chaud, il ne coulera pas facilement et ne se mélangera pas correctement.
- Un flux de métal incomplet entraîne également des arrêts à froid, généralement quand la pression n'est pas bonne.
Comment prévenir les arrêts à froid?
Simple: augmenter la température de coulée! Assurez-vous que le moule est entièrement rempli en ajustant le débit, aussi. Ces ajustements contribuent grandement à prévenir les fermetures à froid.
3. Clignotant
Le clignotement semble inoffensif, mais c’est l’un des défauts les plus frustrants du moulage sous pression de l’aluminium. Cela se produit lorsque l'excès de métal s'échappe du moule., créer mince, nageoires pointues qui doivent être coupées plus tard.
Causes du clignotement
- Une fuite excessive de métal se produit lorsqu’il y a trop de pression dans la matrice, forcer le métal à sortir des endroits indésirables.
- Le désalignement du moule peut également entraîner des bavures, car il crée des espaces permettant au métal de se faufiler..
Comment éviter de clignoter
Un entretien régulier du moule et la garantie que la matrice est correctement alignée et serrée sont des étapes essentielles pour éviter les bavures.. Gardez vos outils en forme!
4. Gauchissement
Avez-vous déjà vu un moulage sortir tordu ou plié? C'est une déformation. C'est comme ce qui se passe lorsque vous faites cuire du bacon : une chaleur inégale le fait se recroqueviller.. Le Warping est essentiellement la version métallique du bacon.
Causes de déformation
- Des taux de refroidissement inégaux sont les suspects habituels ici. Si une partie du moulage refroidit plus vite que le reste, ça se déforme.
- Les sections minces du moulage peuvent se déformer plus facilement car elles refroidissent plus rapidement que les sections plus épaisses..
Mesures préventives contre la déformation
Vous avez besoin d’un refroidissement uniforme pour éviter la déformation. Ajustez la conception du moule pour vous assurer que toutes les sections refroidissent au même rythme. Des murs plus épais peuvent aider, aussi!
5. Défauts de surface (Ampoules, Marques)
Les défauts de surface sont comme l’acné sur le moulage : laids et difficiles à cacher. Des cloques et des marques se forment à la surface, ce qui rend le casting bâclé.
Causes des défauts de surface
- Une mauvaise qualité de surface du moule conduit souvent à ces problèmes. Un moule rugueux ou endommagé transférera ces imperfections au moulage.
- Une pression excessive peut également provoquer des trous de soufflage dans le moulage sous pression en aluminium., où le gaz piégé s'échappe et crée des bulles.
Comment éviter les défauts de surface
Gardez la surface du moule en parfait état! Régulier polissage et entretien des surfaces du moule peut minimiser les défauts de surface. Aussi, le contrôle de la pression de coulée aide à empêcher le gaz de s'échapper, réduisant le risque de trous de soufflage.
Défauts moins courants de moulage sous pression en aluminium
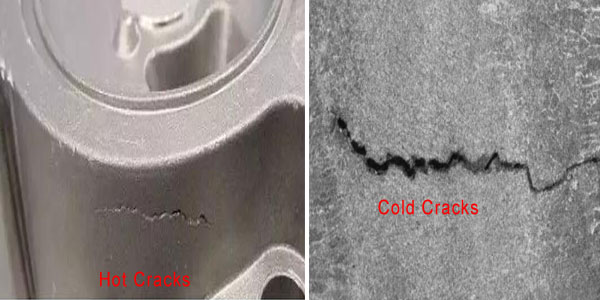
6. Craquage à chaud
Le craquage à chaud est exactement ce à quoi cela ressemble: fissures qui se forment lorsque la pièce moulée est encore chaude. Cela se produit lorsque des contraintes internes provoquent la rupture du métal avant qu’il ne soit complètement solidifié..
Causes de fissuration à chaud
- Les contraintes internes sont la principale cause de fissuration à chaud. Lorsque le métal refroidit de manière inégale ou trop rapide, ça peut craquer.
- Des temps de refroidissement inadéquats peuvent aggraver le problème.
Comment prévenir les fissures à chaud
Laissez le temps de coulée refroidir uniformément. L'ajustement des temps de refroidissement et l'utilisation d'alliages dotés de meilleures propriétés thermiques peuvent contribuer à réduire les contraintes internes et à prévenir les fissures..
7. Craquage à froid
Fissuration à froid, d'autre part, se produit après le refroidissement de la pièce moulée. Ce type de fissuration se produit en raison de contraintes résiduelles ou lorsque la température du moule est trop élevée..
Causes de la fissuration à froid
- Les contraintes résiduelles après refroidissement de la pièce moulée peuvent entraîner des fissures..
- Des températures excessives du moule pendant le processus peuvent causer des problèmes une fois la pièce refroidie..
Comment éviter la fissuration à froid
Surveillez de près les températures du moule et envisagez d'utiliser des techniques de réduction des contraintes après la coulée., comme le traitement thermique.
8. Remplissage incomplet
Parfois, le moule n’est pas entièrement rempli de métal, ce qui entraîne un casting incomplet. Ce défaut, c'est comme essayer de remplir un verre d'eau mais n'en arriver qu'à la moitié du chemin..
Causes d'un remplissage incomplet
- Un flux de métal insuffisant est une cause fréquente. Si le métal en fusion ne coule pas assez vite, le moule ne se remplit pas complètement.
- Une faible pression pendant le processus de coulée peut également entraîner un remplissage incomplet.
Comment éviter un remplissage incomplet
Assurez-vous que la vitesse de coulée est optimisée et que la conception des portes permet un flux de métal fluide et rapide.. Cela garantit que le moule est complètement rempli.
Comment détecter et tester les défauts?
Identifier les défauts dans moulage sous pression en aluminium est crucial pour garantir la qualité et la performance. Un défaut non détecté peut entraîner une fragilisation des pièces, mauvaise esthétique, et même un échec dans l'application. Plusieurs méthodes peuvent détecter et tester les défauts, chacun adapté à différents types de défauts.
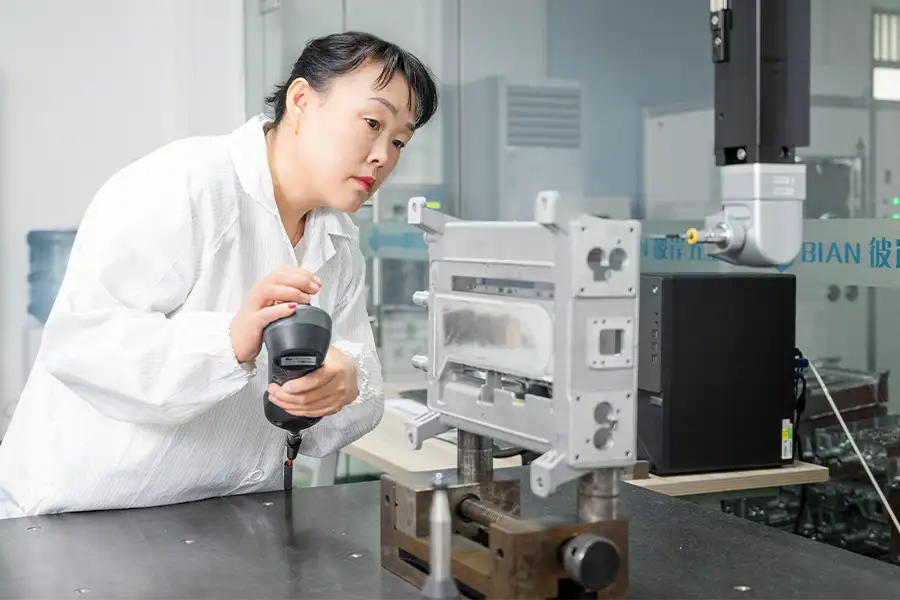
Inspection visuelle
La méthode la plus simple pour identifier les défauts est l’inspection visuelle. Il est utilisé pour détecter les problèmes de surface tels que les fermetures à froid, porosité, ou des défauts de surface comme des cloques et des marques. Inspection des irrégularités de texture, couleur, ou la forme est essentielle pour détecter les défauts dès le début du processus.
Cependant, l'inspection visuelle est limitée aux problèmes au niveau de la surface. Bien que ce soit utile pour repérer les défauts évidents, il ne peut pas révéler des problèmes internes. C’est souvent la première étape avant de procéder à des tests plus détaillés.
Tests aux rayons X
Pour détecter les défauts internes, Les tests aux rayons X sont très efficaces. Cette méthode permet d'examiner la structure interne de la pièce moulée sans la découper. Les rayons X pénètrent dans le matériau et révèlent les vides, gaz piégé, ou incohérences de densité, ce qui le rend idéal pour identifier la porosité interne ou les trous de soufflage dans le moulage sous pression en aluminium.
Les tests aux rayons X sont particulièrement utiles pour les pièces de grande valeur ou critiques où l'intégrité interne est essentielle.. Cependant, c'est plus coûteux et plus long que l'inspection visuelle, ce qui le rend idéal pour les moulages complexes ou à enjeux élevés.
Test de pression
Les tests de pression évaluent la capacité du moulage à résister à la pression interne ou externe, s'assurer qu'il peut fonctionner dans des conditions réelles. Il s'agit de soumettre la pièce moulée à une pression de fluide ou de gaz pour détecter les fuites., points faibles, ou des défaillances potentielles dans la structure.
Cette méthode est particulièrement efficace pour les pièces qui seront exposées à des niveaux de contraintes élevés, tels que des composants de moteur ou des systèmes hydrauliques. Les tests de pression révèlent des défauts comme la porosité, fissures, ou un remplissage incomplet et donne un aperçu de la durabilité et de la fiabilité globales de la pièce moulée.
Meilleures pratiques pour réduire les défauts dans le moulage sous pression d'aluminium
Optimisation de la conception des moules
Un moule bien conçu est essentiel pour minimiser les défauts. Le moule doit faciliter un écoulement uniforme du métal et favoriser un refroidissement uniforme pour réduire le risque de problèmes tels que la porosité et la déformation.. Évitez d'utiliser des coins pointus et des parois minces dans la conception, car ces zones peuvent entraîner des concentrations de contraintes et un refroidissement inégal, augmenter les risques de défauts.
Contrôle de la température dans le moulage sous pression
Il est crucial de maintenir un contrôle précis de la température pendant le processus de moulage sous pression.. Le moule et le métal en fusion doivent être maintenus dans une plage de température optimale.. S'il fait trop chaud ou trop froid, défauts tels que les fermetures à froid, porosité, ou une déformation est susceptible de se produire. La constance de la température tout au long du processus garantit une coulée fluide avec un minimum de défauts.
Entretien régulier des moules
Un entretien régulier des moules est essentiel pour éviter que l'usure n'affecte la qualité de la coulée.. Au fil du temps, les moules peuvent développer des dommages de surface ou perdre leur précision, ce qui peut entraîner des défauts comme des solins ou des imperfections de surface. Des inspections fréquentes et les réparations nécessaires maintiennent les moules en parfait état et garantissent de meilleurs résultats de coulée..
Choisir le bon alliage
Le choix de l'alliage d'aluminium approprié peut avoir un impact significatif sur la qualité du moulage. Certains alliages sont plus sujets aux défauts, tandis que d'autres sont plus stables et fiables. Choisir un alliage avec une bonne fluidité, faible retrait, et une expérience éprouvée en matière de faibles taux de défauts aide à réduire les problèmes de coulée courants et garantit des résultats cohérents..
Conclusion
En fin de journée, Les défauts du moulage sous pression de l'aluminium ne sont qu'une partie du processus. Mais avec les bonnes techniques, vous pouvez les minimiser et produire des pièces moulées de qualité supérieure. En comprenant les défauts de coulée courants, qu'il s'agisse de porosité, fermeture à froid lors du casting, ou des trous de soufflage dans du moulage sous pression en aluminium : vous êtes mieux équipé pour les affronter de front. Vous pouvez désormais contrôler vos types de défauts et obtenir des pièces moulées parfaites.!
Foire aux questions
- Qu'est-ce que la porosité en moulage sous pression, et comment peut-il être minimisé? La porosité fait référence à de petites poches d'air ou vides dans la pièce moulée causés par le piégeage de gaz ou le retrait.. Il peut être minimisé en optimisant la conception et en contrôlant les niveaux de gaz.
- Comment la conception du moule affecte-t-elle les défauts de coulée? Une mauvaise conception du moule peut entraîner un écoulement et un refroidissement irréguliers du métal., entraînant des défauts comme une déformation et un remplissage incomplet. Une bonne conception garantit un processus fluide.
- Les fluctuations de température peuvent-elles provoquer des défauts dans le moulage sous pression de l'aluminium? Oui! Les températures du moule et du métal doivent être soigneusement régulées. Trop de variations peuvent entraîner des défauts comme des fermetures à froid, porosité, ou une déformation.
- Quelles sont les méthodes les plus efficaces pour détecter les défauts internes de coulée? Les tests aux rayons X sont le meilleur moyen de détecter les défauts internes comme la porosité et les trous de soufflage sans endommager la pièce moulée..
- Quels alliages d'aluminium sont les moins susceptibles de développer des défauts lors du moulage sous pression? Alliages spécialement conçus pour le moulage sous pression, comme l'A380 ou l'ADC12, sont connus pour produire moins de défauts en raison de leur excellente fluidité et de leurs faibles taux de retrait. “`