Quand il s'agit de fonderie de métal, il y a beaucoup de choses à considérer, droite? Vous avez différents métaux, différentes méthodes de coulée, et tout un tas de facteurs qui peuvent influencer votre choix. Mais si vous vous demandez quel métal est le plus fréquemment utilisé dans le processus de coulée, tu es au bon endroit. Décomposons tout cela!
Aperçu du processus de casting
Le moulage du métal est un processus de fabrication dans lequel le métal en fusion est versé dans un moule et laissé refroidir et se solidifier pour prendre la forme souhaitée.. Cela semble assez simple, mais il y a plus à faire! Le type de métal que vous utilisez et la manière dont vous le coulez jouent un rôle important dans la qualité du produit final..
Le choix du métal détermine beaucoup—force, durabilité, et résistance à l'usure, entre autres. Choisir le bon métal pour votre projet? C'est essentiel, et cela dépend des exigences du produit et de l'industrie qui l'utilise.
Métaux couramment utilisés en fonderie
Critères de sélection des métaux de coulée
Donc, quel matériau est souvent utilisé dans le moulage? Tout se résume à des facteurs tels que coût, force, poids, et durabilité. Certains métaux supportent mieux la chaleur, d'autres sont plus flexibles, et certains sont simplement plus abordables pour travailler. Savoir ce qui compte le plus pour votre produit vous aide à affiner vos options.
Ferreux vs. Métaux non ferreux en fonderie
Vous avez probablement entendu parler des métaux ferreux et non ferreux. Les métaux ferreux contiennent du fer, contrairement aux métaux non ferreux. Métaux ferreux (comme l'acier et le fer) sont super solides et durables, mais ils peuvent rouiller. Métaux non ferreux (comme l'aluminium et le cuivre) sont légers et résistent à la corrosion, ce qui les rend idéaux pour de nombreux types de casting différents.
Aluminium: Le métal le plus fréquemment utilisé en fonderie
Pourquoi l'aluminium est si populaire dans le moulage? L'aluminium est un matériau durable et est largement utilisé pour le moulage.. Pourquoi? Il coche toutes les cases de ce que vous attendez d’un matériau de moulage. C'est léger, durable, résistant à la corrosion, et relativement peu coûteux. Pas étonnant que ce soit la référence pour tant d’industries!
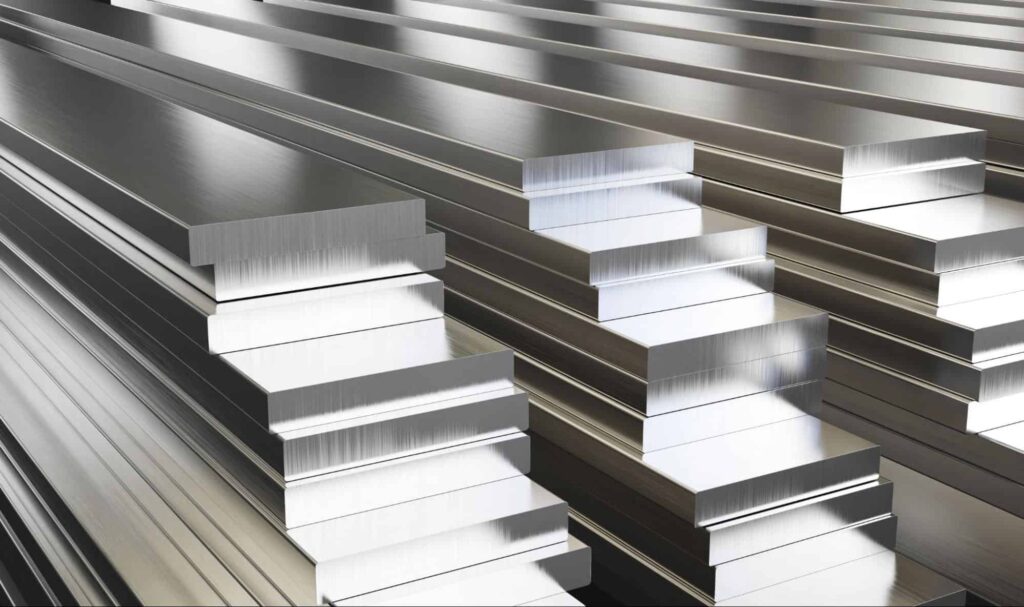
Léger et haute résistance
Même s'il est léger, l'aluminium a du punch en termes de résistance. Il est parfait pour les applications où le poids compte, comme dans l'aérospatiale et industrie automobile. Vous obtenez le meilleur des deux mondes : la force sans l'encombrement.
Résistance à la corrosion
La résistance naturelle de l’aluminium à la corrosion le rend idéal pour les produits exposés à des environnements difficiles, comme des meubles d'extérieur ou des composants de moteur. Il ne rouille pas comme les métaux ferreux, donc il dure plus longtemps dans des conditions difficiles.
Rentabilité dans la production à grande échelle
En production à grande échelle, moulage sous pression en aluminium est un choix rentable. Il est facile de travailler avec, nécessite moins d’énergie pour fondre, et peut être recyclé, ce qui réduit les coûts globaux pour les fabricants.
Large application dans tous les secteurs
Vous trouverez de l’aluminium partout : dans les voitures, avions, électronique, matériaux de construction, et même des biens de consommation. Sa polyvalence et sa disponibilité en font le métal le plus fréquemment utilisé en fonderie dans un large éventail d'industries..
Autres métaux fréquemment utilisés dans le moulage
Acier
L'acier est connu pour son incroyable résistance et sa durabilité.. Il est souvent utilisé dans les applications intensives où la robustesse est essentielle., comme la construction et les machines. Cependant, c'est plus lourd que l'aluminium et peut rouiller, ce n'est donc pas toujours le meilleur choix pour chaque projet.
Fer
Fonte, en particulier la fonte grise, est une autre option populaire. Il est extrêmement durable et idéal pour des applications telles que les blocs moteurs, tuyaux, et ustensiles de cuisine. Mais comme l'acier, le fer est lourd et a tendance à rouiller.
Cuivre et alliages de cuivre
Cuivre et ses alliages (comme le bronze et le laiton) sont également largement utilisés en coulée, en particulier pour les objets décoratifs ou les composants où la conductivité est importante. Le cuivre est durable et conduit bien la chaleur et l’électricité, mais c'est plus cher que l'aluminium ou l'acier.
Zinc
Le zinc est idéal pour les petits, moulages complexes en raison de son faible point de fusion et de son excellente fluidité. Il est souvent utilisé dans le moulage sous pression pour des choses comme les attaches, petit matériel, et pièces automobiles. Ce n'est pas aussi résistant que l'acier ou l'aluminium, mais il est facile à lancer et offre d'excellents détails.
Avantages et inconvénients des différents métaux en fonderie
Avantages et inconvénients de l'aluminium
- Avantages: Léger, résistant à la corrosion, rentable, très polyvalent
- Inconvénients: Résistance inférieure à celle de l'acier, sujet à la fissuration sous des contraintes extrêmes
Avantages et inconvénients de l'acier
- Avantages: Fort, durable, idéal pour les applications lourdes
- Inconvénients: Lourd, sujet à la rouille, plus cher à traiter
Avantages et inconvénients du fer
- Avantages: Excellente durabilité, haute résistance à l'usure
- Inconvénients: Lourd, sensible à la rouille, fragile par rapport aux autres métaux
Cuivre et Zinc: Forces et faiblesses
- Cuivre: Fort, hautement conducteur, mais cher et lourd
- Zinc: Facile à lancer, point de fusion bas, mais pas aussi résistant que l'aluminium ou l'acier
Comment choisir le bon métal pour votre projet de moulage?
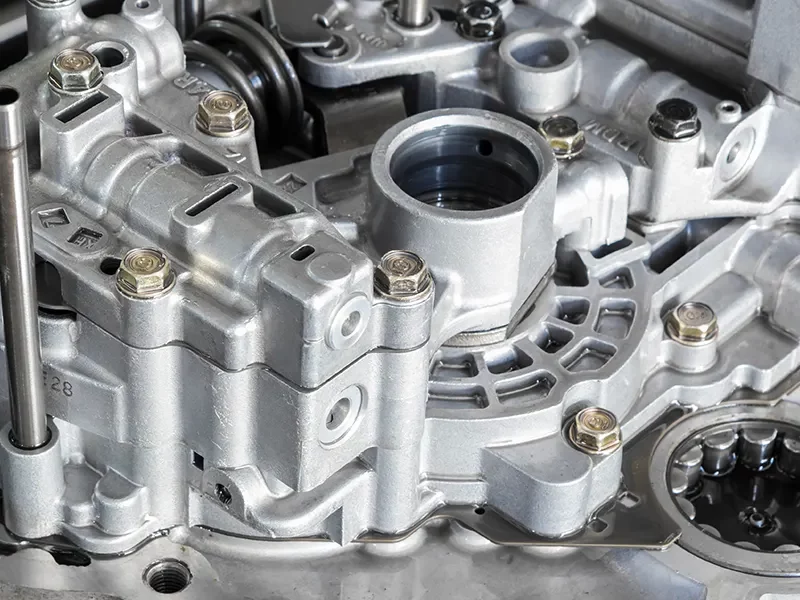
Prise en compte des propriétés des matériaux
Le choix du bon métal dépend de facteurs tels que la résistance, poids, durabilité, et résistance à la corrosion. L'aluminium peut être idéal pour les projets légers, mais si tu as besoin de quelque chose de plus fort, l'acier ou le fer pourrait être mieux. Pensez à ce qui compte le plus pour votre candidature.
Exigences du projet et normes de l’industrie
Différentes industries ont des normes différentes. Par exemple, l'industrie aérospatiale a besoin de poids léger, métaux forts comme l'aluminium, tandis que l'industrie de la construction s'appuie sur des matériaux plus lourds, des métaux plus durables comme l'acier. Alignez toujours votre choix avec les exigences de votre projet spécifique. Vous pouvez également consulter le fabricant de moulage sous pression. Ces experts peuvent vous guider en fonction de leur expérience avec différentes méthodes de coulée et différents métaux..
Préférences de métaux spécifiques à l'industrie
Industrie automobile
Dans le monde automobile, l'aluminium est le premier choix en raison de sa combinaison de légèreté et de haute résistance. Il est couramment utilisé dans les blocs moteurs, cas de transmission, et panneaux de carrosserie. En réduisant le poids global des véhicules, l'aluminium contribue à améliorer le rendement énergétique et les performances. Cela en fait un matériau essentiel pour la conception et la fabrication automobiles modernes..
Industrie aérospatiale
Pour le secteur aérospatial, chaque once compte. L'aluminium est privilégié en raison de son faible poids et de sa haute résistance., qui sont cruciaux pour les composants aéronautiques. L'utilisation de l'aluminium permet de minimiser la masse globale de l'avion, améliorer le rendement énergétique et les performances sans compromettre la durabilité. C’est un matériau clé pour répondre aux exigences de performance strictes de l’ingénierie aérospatiale..
Biens de consommation
L'aluminium est largement utilisé dans les biens de consommation, y compris les smartphones et les appareils de cuisine, grâce à son aspect élégant et sa légèreté. Il offre une durabilité et un look moderne, ce qui en fait un choix populaire pour une gamme de produits. En plus, le cuivre et ses alliages sont souvent utilisés dans les objets de décoration, appréciés pour leur attrait esthétique et leur polyvalence.
Construction
En chantier, la résistance et la durabilité sont essentielles. L'acier et le fer sont généralement moulés en gros, des composants robustes tels que des poutres, tuyaux, et pièces de machines. Ces métaux sont privilégiés pour leur capacité à supporter de lourdes charges et à résister à l'usure dans le temps., ce qui les rend essentiels à l'intégrité structurelle et aux performances durables dans projets de construction.
Conclusion
L'aluminium se distingue comme le métal le plus fréquemment utilisé dans le moulage en raison de sa légèreté., force, résistance à la corrosion, et la rentabilité. Mais cela ne veut pas dire que c'est la seule option. Acier, fer, cuivre, et le zinc jouent également un rôle important dans la coulée, chacun offrant des avantages uniques pour des applications spécifiques. Choisir le bon métal revient à comprendre les besoins de votre projet et à équilibrer des facteurs comme le poids., durabilité, et le coût. Maintenant que tu sais quel métal est le plus fréquemment utilisé dans le processus de coulée, vous êtes sur le point de prendre la meilleure décision pour votre prochain projet de casting.
FAQ
- Quel métal est le plus fréquemment utilisé dans le processus de coulée? L'aluminium est le métal le plus fréquemment utilisé dans le moulage sous pression en raison de sa légèreté., force, et résistance à la corrosion.
- Quel matériau est souvent utilisé dans le moulage pour les applications intensives ?? L'acier et le fer sont couramment utilisés pour les applications intensives en raison de leur résistance et de leur durabilité..
- Quelles méthodes de coulée fonctionnent le mieux pour l'aluminium? L'aluminium est souvent utilisé dans le moulage sous pression, moulage au sable, et le moulage de précision en raison de sa polyvalence et de sa facilité d'utilisation.
- L'aluminium est-il recyclable lors du processus de coulée? Oui, l'aluminium est hautement recyclable et peut être réutilisé sans perdre ses propriétés, ce qui en fait une option écologique.
- Quels sont les inconvénients de l'utilisation de l'acier dans la coulée? L'acier est lourd et sujet à la rouille, ce qui le rend moins adapté aux applications où le poids et la résistance à la corrosion sont importants.