Nel mondo della produzione e della fabbricazione, Il routing CNC ha rivoluzionato il modo in cui creiamo progetti intricati e precisi. Con l'aiuto della tecnologia avanzata, Le macchine di routing a CNC possono tagliare e modellare una vasta gamma di materiali con precisione ed efficienza senza pari. In questo articolo, Esploreremo i dettagli del routing CNC, dai suoi principi di base alle sue applicazioni in vari settori.
Cos'è il routing CNC?
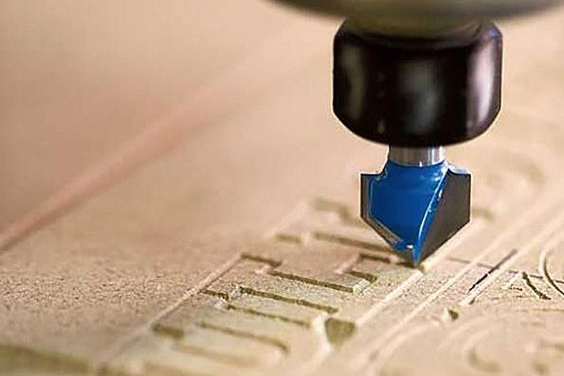
Il routing CNC sta per il routing di controllo numerico del computer, che si riferisce al processo di utilizzo di una macchina controllata da computer per tagliare e modellare i materiali secondo un design pre-programmato. Questa tecnologia consente risultati precisi e coerenti, rendendolo ideale per la produzione di parti e componenti complessi.
Cos'è una macchina per router CNC
Una macchina per router CNC è un tipo di macchina di routing CNC che è specificamente progettata per tagliare e modellare i materiali come il legno, metallo, plastica, e compositi. Queste macchine sono costituite da uno strumento di taglio collegato a un sistema controllato da computer che guida lo strumento lungo un percorso predeterminato per creare la forma o il design desiderati.
Come funzionano le macchine a CNC?
Le macchine CNC funzionano interpretando un file di progettazione digitale e utilizzando tali informazioni per controllare il movimento dello strumento di taglio. L'operatore inserisce i parametri di progettazione nel sistema informatico, che quindi traduce le istruzioni in movimenti precisi dello strumento di taglio. Questo livello di automazione consente una maggiore precisione ed efficienza nel processo di produzione.
Processo passo-passo del routing CNC
- Inserimento del design: Il primo passo nel funzionamento di una macchina CNC prevede l'inserimento dei parametri di progettazione nel sistema informatico. Questo file di progettazione digitale funge da progetto per il processo di taglio e modellatura.
- Interpretazione delle istruzioni: Una volta caricato il file di progettazione, Il sistema informatico interpreta le istruzioni e le converte in movimenti precisi dello strumento di taglio. Questa traduzione garantisce che il prodotto finale corrisponda alle specifiche di progettazione con precisione.
- Guidare lo strumento: La macchina CNC guida lo strumento di taglio lungo il percorso predeterminato delineato nel file di progettazione. Lo strumento si muove lungo la x, y, e assi z, Seguendo le istruzioni programmate per creare la forma o il modello desiderati.
- Esecuzione del processo di taglio: Mentre lo strumento di taglio si muove attraverso il materiale, Rimuove il materiale in eccesso in una serie di movimenti precisi. Questo processo di taglio viene ripetuto fino a raggiungere la forma o il design finale, risultante in un prodotto finito che soddisfa i requisiti esatti del design.
- Monitoraggio dell'operazione: Durante tutto il processo di taglio, La macchina CNC monitora continuamente e regola i parametri di taglio per garantire coerenza e accuratezza. Questo meccanismo di feedback in tempo reale aiuta a ottimizzare l'operazione di taglio e mantenere il controllo di qualità.
- Completare l'attività: Una volta completato il processo di taglio, La macchina CNC interrompe l'operazione, e il prodotto finito è pronto per l'ulteriore elaborazione o l'assemblaggio. L'efficienza e la precisione delle macchine CNC le rendono strumenti indispensabili nel settore manifatturiero.
Tipi di macchine di routing CNC
Esistono diversi tipi di macchine di routing CNC, ognuno con le proprie capacità e applicazioni uniche.
UN. 3-Macchine dell'asse
A partire dalle macchine di routing CNC a 3 assi, Questi sistemi sono dotati della capacità di spostare lo strumento di taglio lungo tre assi primari - x, y, e z. Questa configurazione fondamentale consente operazioni di taglio e modellatura di base, rendendoli versatili e adatti a una vasta gamma di applicazioni. 3-Le macchine dell'asse sono comunemente usate per compiti come la profilazione, incisione, e intaglio su vari materiali.
B. 4-Macchine dell'asse
Passando alle macchine di routing CNC a 4 assi, Questi sistemi fanno un ulteriore passo avanti incorporando un ulteriore asse rotante nella miscela. Oltre ai tre assi principali, 4-Le macchine dell'asse sono in grado di ruotare lo strumento di taglio lungo un quarto asse, Fornire capacità migliorate per la creazione di design e forme più complessi. Con la capacità di manovrare attorno a superfici curve e contorni intricati, 4-Le macchine dell'asse sono adatte per applicazioni che richiedono un livello più elevato di precisione e dettagli.
C. 5-Macchine dell'asse
In prima linea nella tecnologia di routing CNC ci sono le macchine a 5 assi, rinomata per la loro precisione e versatilità senza pari. Oltre ai tre assi standard, 5-Le macchine dell'asse vantano la possibilità di inclinare e ruotare lo strumento di taglio lungo due assi aggiuntivi. Questo livello avanzato di manovrabilità consente facilmente la produzione di design altamente complessi e dettagliati. 5-Le macchine dell'asse sono spesso utilizzate in settori come l'aerospaziale, settore automobilistico, e prototipazione, dove sono essenziali geometrie complesse e contorni lisci.
Vantaggi e svantaggi del routing CNC
Vantaggi del routing CNC
- Precisione: Le macchine di routing CNC offrono una precisione eccezionale, Garantire che i prodotti si allineino proprio con le specifiche di progettazione. Ciò è cruciale nelle industrie che richiedono tolleranze strette e dettagli intricati.
- Efficienza: Il routing CNC semplifica i processi di produzione, Ridurre i tempi e i costi del lavoro attraverso l'automazione. Aumenta la produttività mantenendo un'output di alta qualità.
- Versatilità: I router CNC versatili possono gestire vari materiali come il legno, metallo, plastica, e compositi, Catering a una vasta gamma di industrie e applicazioni.
- Personalizzazione: Il routing CNC consente una facile creazione di design personalizzati e complessi mediante percorsi di taglio. Questa flessibilità soddisfa i requisiti di progettazione specifici in modo efficiente.
- Coerenza: I router CNC offrono una qualità costante nelle corse di produzione, Garantire l'uniformità e soddisfare standard elevati in settori come Automotive ed Electronics.
- Efficacia in termini di costi: Nonostante l'investimento iniziale, Il routing CNC fornisce risparmi sui costi a lungo termine attraverso rifiuti ridotti, Efficienza migliorata, e scalabilità per adattarsi alle richieste di mercato.
Svantaggi del routing CNC
- Complessità: Le macchine di routing CNC operative e di programmazione richiedono competenze e formazione specializzate, che può essere una barriera per alcune aziende senza l'esperienza necessaria.
- Costo: L'investimento iniziale nelle apparecchiature di routing CNC può essere significativo, rendendolo un sostanziale impegno finanziario per le piccole imprese o per quelli con budget limitati.
- Manutenzione: Le macchine di routing CNC richiedono manutenzione e manutenzione regolari per garantire prestazioni ottimali, che può aggiungere ai costi operativi complessivi e ai tempi di inattività.
- Flessibilità limitata: Mentre le macchine di routing CNC offrono versatilità nel taglio dei materiali, Possono avere limiti in termini di dimensioni e forma del pezzo che possono gestire, limitando alcune possibilità di progettazione.
Quali materiali possono essere tagliati su un router CNC?
I router CNC possono tagliare una vasta gamma di materiali, compreso il legno, metallo, plastica, acrilico, e compositi. Questa versatilità li rende ideali per una varietà di settori, dalla lavorazione del legno all'aerospaziale.
- Boschi: I router CNC eccellono nel tagliare una varietà di tipi di legno, compresi i legni duri come quercia, acero, e noce, così come boschi più morbidi come pino e cedro.
- Plastica: I router CNC sono anche abili nel tagliare diversi tipi di materie plastiche, come acrilico, PVC, policarbonato, e nylon.
- Metalli: Mentre non tutti i router CNC sono progettati per tagliare i metalli, Alcuni modelli dotati degli strumenti e delle funzionalità necessari possono gestire l'alluminio, ottone, rame, e altri metalli morbidi.
- Compositi: I router CNC sono comunemente usati per tagliare materiali compositi come la fibra di vetro, fibra di carbonio, e laminati
- Materiali in schiuma e schiuma: I router CNC possono anche tagliare in schiuma e materiali da schiuma, come il polistirene espanso (EPS) e schiuma di poliuretano.
Applicazioni del routing CNC
La versatilità e l'efficienza dei router CNC li rendono strumenti indispensabili per una vasta gamma di applicazioni, consentendo ai produttori di ottenere progetti complessi, semplificare i processi di produzione, e migliorare la qualità del prodotto.
Lavorazione del legno
La tecnologia di routing CNC si è affermata come una pietra miliare nel settore della lavorazione del legno, Fornire lavoratori del legno gli strumenti e le capacità necessari per creare progetti intricati, tagliare forme complesse, e produrre mobili e mobili personalizzati. Dall'elaborazione di mulini decorativi alla progettazione di mobili su misura, I router CNC offrono capacità di taglio e modellatura di precisione che elevano l'artigianato per la lavorazione del legno a nuove altezze di creatività e precisione.
Fabbricazione di metalli
Nel regno della fabbricazione dei metalli, La tecnologia di routing CNC svolge un ruolo fondamentale nella produzione di parti metalliche con precisione e precisione eccezionali. Utilizzando i router CNC, I fabbricanti di metallo possono tagliare e modellare i componenti metallici, compresi quelli usati in pressofusione di alluminio, con dettagli meticolosi e coerenza. La capacità di creare progetti intricati e tagli precisi rende il routing CNC uno strumento indispensabile per la produzione di componenti per diversi settori, Dall'automotivo e aerospaziale all'elettronica e ai macchinari.
Fabbricazione di plastica
Allo stesso modo, La tecnologia di routing CNC trova un'applicazione diffusa nel settore della fabbricazione in plastica, dove viene utilizzato per tagliare e modellare le parti di plastica, stampi, e prototipi con precisione e ripetibilità senza pari. Dalla creazione di segnaletica e display personalizzati alla produzione di intricati componenti di plastica per vari prodotti, I router CNC consentono ai fabbricanti di plastica di ottenere risultati di alta qualità in modo efficiente ed economico. La versatilità del routing CNC nella gestione di diversi tipi di materie plastiche lo rende una soluzione versatile per soddisfare le diverse esigenze del settore della fabbricazione di plastica.
Collaborare con Bian die Cast
Se stai cercando un protagonista che offre casting, Lavorazione CNC, e servizi di finitura, Non guardare oltre Bian die Cast. Con anni di esperienza e competenza nel settore, Bian Die Cast si impegna a fornire prodotti di alta qualità e un servizio clienti eccezionale.
Conclusione
Insomma, Il routing CNC è una tecnologia potente che ha trasformato l'industria manifatturiera fornendo precisione senza pari, efficienza, e versatilità. Che tu sia in lavorazione del legno, fabbricazione di metalli, o fabbricazione di plastica, Le macchine di routing CNC offrono una soluzione economica per produrre parti complesse e componenti con facilità. La collaborazione con un produttore di fiducia come Bian Die Cast può aiutarti a portare il tuo progetto al livello successivo e raggiungere il successo negli sforzi di produzione.