アルミダイカストは非常に効率的な製造プロセスです. 金属をピンポイントの精度で複雑な形状に成形することができます。. しかし、ここがキッカーです: その利点にもかかわらず, 金属鋳造の欠陥が侵入する可能性があります, 大量の頭痛を引き起こす. アルミダイカストの欠陥に対処したことがある方, それがどれほどイライラし、コストがかかるかわかるでしょう. でも汗をかかないでください! 最も一般的なアルミニウム鋳造の欠陥について詳しく見ていきましょう, 何が彼らを引き起こすのか, そして最も重要なのは、それらを回避する方法です.
アルミニウム ダイカストの一般的な欠陥
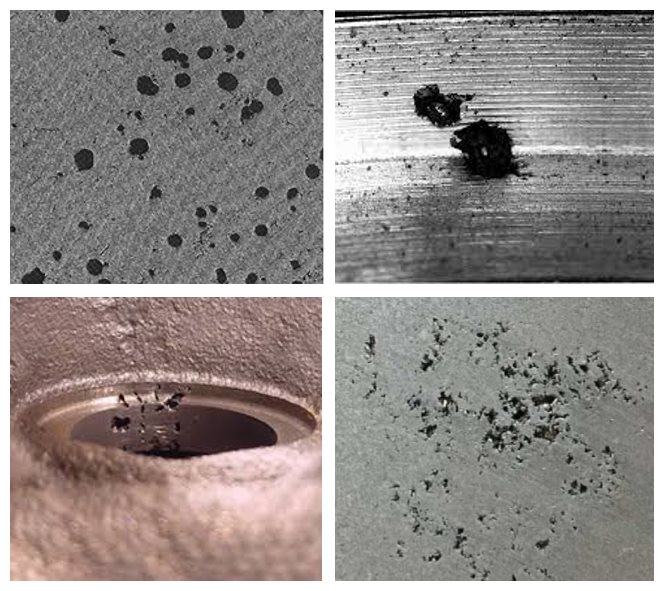
1. 気孔率
多孔性は目に見えないトラブルメーカーです ダイカスト工程. スポンジが膨らむときにできる小さなエアポケットのようなものです. 必ずしも表面的には見えない, でもそこにある, 構造を弱める.
多孔性の原因
- ガスの閉じ込めが主な原因. 鋳造中に溶融金属内に空気やその他のガスが閉じ込められた場合, それらは空隙を形成します.
- 冷却時の収縮も原因のひとつ. 金属が固まるにつれて, それは収縮します, 材料が均一に分散されていない場合、小さな空隙が残る.
多孔性を避ける方法
多孔性を回避するコツは細部にあります. 鋳造設計を最適化して金属の流れをスムーズにし、プロセス中のガスレベルを確実に制御します。. 適切な合金を使用すると、気孔率のリスクも軽減できます.
2. コールドシャット
ああ, キャスト中の恐ろしい寒さ! これは、溶融金属の 2 つの流れが合流しても適切に融合できない場合に発生します。, 目に見える縫い目を残す. カチッとはまらない 2 つのパズルのピースと考えてください.
冷温停止の原因
- 金属の温度が低いとこの問題が発生することがよくあります. 溶融金属が十分に熱くない場合, スムーズに流れず、適切にブレンドされません.
- 不完全なメタルフローもコールドシャットの原因となります, 通常、圧力が適切でないとき.
冷気停止を防ぐ方法?
単純: 鋳造温度を上げる! 流量を調整して金型が完全に充填されていることを確認してください, あまりにも. これらの調整はコールドシャットの防止に大いに役立ちます.
3. 点滅
点滅する音は無害です, しかし、これは最もイライラするアルミニウム ダイカストの欠陥の 1 つです. 余分な金属が金型から漏れ出るときに発生します, 薄いものを作成する, 後でトリミングする必要がある鋭いヒレ.
点滅の原因
- 金型内の圧力が高すぎると過剰な金属漏れが発生します, 不要な場所から金属を押し出す.
- 金型の位置ずれによって金属が侵入する隙間ができるため、バリが発生する可能性もあります。.
点滅を避ける方法
定期的に金型をメンテナンスし、金型が適切に位置合わせされて固定されていることを確認することは、バリを回避するために不可欠な手順です。. 工具の形を整えておく!
4. 反り
鋳物がねじれたり曲がったりして出てくるのを見たことがありますか? それは歪んでるよ. ベーコンを調理するときに起こることと同じです。熱が不均一になるとベーコンが丸まってしまいます。. ワーピングは基本的にベーコンのメタルバージョンです.
反りの原因
- ここでよく疑われるのは、不均一な冷却速度です。. 鋳造品の一部が他の部分よりも早く冷える場合, 歪む.
- 鋳物の薄い部分は厚い部分よりも早く冷却されるため、反りやすくなります。.
反り防止対策
反りを防ぐには均一な冷却が必要です. すべてのセクションが同じ速度で冷却されるように金型の設計を調整します。. 壁が厚いと効果がある, あまりにも!
5. 表面欠陥 (水疱, マーク)
表面欠陥は鋳物にできたニキビのようなもので、醜く隠すのが困難です。. 表面に水泡や跡が残る, キャスティングがずさんに見える.
表面欠陥の原因
- 金型表面の品質が低いと、これらの問題が発生することがよくあります. 粗いまたは損傷した金型は、その欠陥を鋳物に転写します。.
- 過度の圧力はアルミダイカストにブローホールを引き起こす可能性もあります, 閉じ込められたガスが抜けて泡が発生する場所.
表面欠陥を避ける方法
金型表面を最高の形状に保ちます! 通常 表面研磨とメンテナンス 金型の表面欠陥を最小限に抑えることができます. また, 鋳造圧力を制御することでガスの流出を防ぐことができます, ブローホールのリスクを軽減する.
あまり一般的ではないアルミニウム ダイカストの欠陥
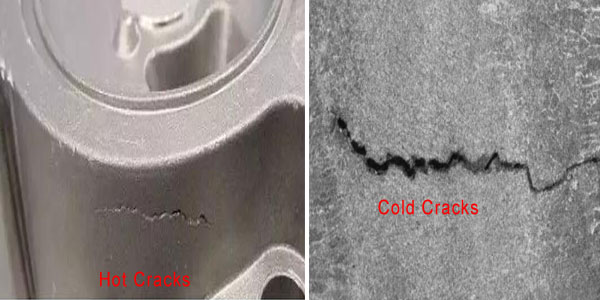
6. ホットクラッキング
ホットクラッキングはまさにその通りです: 鋳物がまだ熱いときに生じる亀裂. これは、内部応力によって金属が完全に固まる前に破損するときに起こります。.
高温割れの原因
- 内部応力は高温割れの主な原因です. 金属の冷却が不均一または速すぎる場合, ひび割れてしまう可能性があります.
- 冷却時間が不十分だと問題が悪化する可能性があります.
高温割れを防ぐ方法
鋳造品が均一に冷めるまで時間を与えます. 冷却時間を調整し、より優れた熱特性を持つ合金を使用すると、内部応力を軽減し、亀裂を防ぐことができます。.
7. コールドクラッキング
コールドクラッキング, 一方で, 鋳物が冷却された後に発生します. このタイプのクラックは、残留応力または金型温度が高すぎる場合に発生します。.
低温割れの原因
- 鋳物が冷却された後の残留応力は亀裂を引き起こす可能性があります.
- プロセス中の金型温度が過剰になると、鋳物が冷えると問題が発生する可能性があります.
コールドクラッキングを避ける方法
金型温度を注意深く監視し、鋳造後に応力除去技術の使用を検討してください。, 熱処理など.
8. 不完全な充填
金型に金属が完全に充填されない場合がある, 不完全なキャストが発生する. この欠陥は、コップに水を入れようとして半分しか満たせないようなものです。.
充填不完全の原因
- 不十分なメタルフローが一般的な原因です. 溶融金属が十分に速く流れない場合, 型が完全に埋まらない.
- 鋳造プロセス中の圧力が低いと充填が不完全になる可能性もあります.
充填不完全を防ぐには
鋳造速度が最適化されていること、およびゲートの設計によりスムーズかつ迅速な金属の流れが可能であることを確認してください。. これにより、金型が完全に充填されます。.
欠陥を検出してテストする方法?
欠陥の特定 アルミダイカスト 品質とパフォーマンスを確保するために重要です. 欠陥が検出されないまま放置されると、部品の脆弱化につながる可能性があります, 劣悪な美学, そしてアプリケーションの失敗さえも. いくつかの方法で欠陥を検出およびテストできます, それぞれが異なる種類の欠陥に適しています.
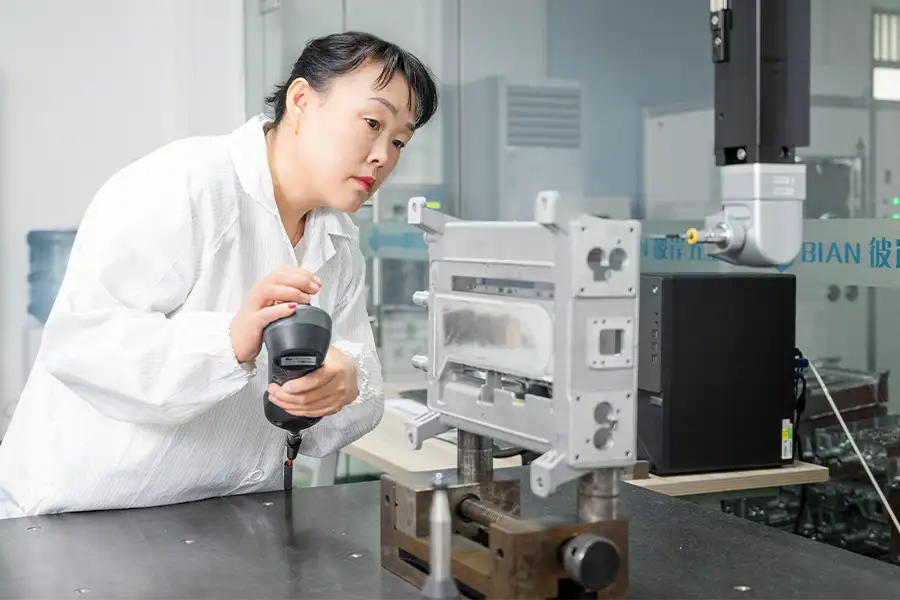
目視検査
欠陥を特定する最も簡単な方法は目視検査です。. 冷間停止などの表面レベルの問題を特定するために使用されます, 気孔率, または水泡や跡などの表面欠陥. 質感の凹凸検査, 色, または形状はプロセスの初期段階で欠陥を検出するために不可欠です.
しかし, 目視検査は表面レベルの問題に限定されます. 明らかな欠陥を見つけるのには役立ちますが、, 内部問題を明らかにすることはできません. 多くの場合、これはより詳細なテストに進む前の最初のステップです.
X線検査
内部欠陥検出用, X線検査は非常に効果的です. この方法により、鋳物を切らずに内部構造を検査することができます。. X線は材料を透過し、空隙を明らかにします, 閉じ込められたガス, または密度の不一致, アルミニウムダイカストの内部気孔やブローホールを特定するのに最適です。.
X 線検査は、内部の完全性が不可欠な高価な部品や重要な部品に特に役立ちます。. しかし, 目視検査に比べて費用も時間もかかります, 複雑な鋳造や一か八かの鋳造に最適です。.
圧力試験
圧力試験では、内部または外部の圧力に耐える鋳物の能力を評価します。, 現実世界の条件下で確実に動作できるようにする. 漏れを検出するために鋳物に流体またはガスの圧力を加えることが含まれます。, 弱点, または構造上の潜在的な欠陥.
この方法は、高レベルの応力にさらされる部品に特に効果的です。, エンジン部品や油圧システムなど. 圧力試験により気孔などの欠陥が判明, ひび割れ, または不完全な充填を調査し、鋳造品の全体的な耐久性と信頼性についての洞察を提供します。.
アルミニウムダイカストの欠陥を減らすためのベストプラクティス
金型設計の最適化
欠陥を最小限に抑えるには、適切に設計された金型が重要です. 金型は、金属の流れを均一にし、均一な冷却を促進して、多孔性や反りなどの問題のリスクを軽減する必要があります。. デザインでは鋭い角や薄い壁の使用を避けてください。, これらの領域は応力集中や不均一な冷却につながる可能性があるため、, 欠陥の可能性が高まる.
ダイカストの温度管理
ダイカストプロセス中に正確な温度制御を維持することが重要です. 金型と溶融金属の両方を最適な温度範囲内に維持する必要があります. 暑すぎたり寒すぎたりすると, 冷間遮断などの不具合, 気孔率, または反りが発生する可能性があります. プロセス全体を通じて温度が一定であるため、欠陥を最小限に抑えた滑らかな鋳造が保証されます。.
定期的な金型のメンテナンス
鋳造品質に影響を与える磨耗を防ぐために、金型の定期的なメンテナンスが不可欠です. 時間とともに, 金型の表面に損傷が生じたり、精度が低下したりする可能性があります, バリや表面の欠陥などの欠陥が発生する可能性があります. 頻繁な検査と必要な修理により、金型を最高の状態に保ち、より良い鋳造結果を保証します。.
適切な合金の選択
適切なアルミニウム合金の選択は、鋳造の品質に大きな影響を与える可能性があります. 一部の合金は欠陥が発生しやすい, 他のものはより安定していて信頼性があります. 流動性の良い合金の選択, 低収縮, 低欠陥率の実証済みの実績により、鋳造に関する一般的な問題が軽減され、一貫した結果が保証されます。.
結論
一日の終わりに, アルミダイカストの欠陥はプロセスの一部にすぎません. しかし、正しいテクニックを使えば、, それらを最小限に抑えて最高品質の鋳物を製造できます. 鋳造の一般的な欠陥 (気孔率など) を理解することで, 鋳造時のコールドシャット, またはアルミダイカストのブローホールなど、正面から取り組む準備ができています。. これで、欠陥の種類を抑制し、完璧な鋳物を得ることができます。!
よくある質問
- ダイカストの気孔率とは何ですか, そしてそれを最小限に抑えるにはどうすればよいでしょうか? 気孔率とは、ガスの閉じ込めや収縮によって生じる鋳造品内の小さなエアポケットまたは空隙を指します。. 設計を最適化し、ガスレベルを制御することで最小限に抑えることができます。.
- 金型設計は鋳造欠陥にどのような影響を与えるか? 金型の設計が不十分だと、金属の流れや冷却が不均一になる可能性があります, 反りや充填不完全などの欠陥が発生する. 優れた設計によりスムーズなプロセスが保証されます.
- 温度変動はアルミダイカストに欠陥を引き起こす可能性がありますか?? はい! 金型と金属の温度は両方とも慎重に制御する必要がある. ばらつきが多すぎるとコールドシャットなどの欠陥が発生する可能性があります, 気孔率, または反り.
- 鋳物の内部欠陥を検出する最も効果的な方法は何ですか? X 線検査は、鋳物に損傷を与えることなく、気孔やブローホールなどの内部欠陥を検出する最良の方法です。.
- ダイカスト中に欠陥が発生する可能性が最も低いアルミニウム合金はどれですか? ダイカスト用に特別に設計された合金, A380 や ADC12 など, 優れた流動性と低い収縮率により、欠陥が少ないことで知られています。. “`