Die Gussform der Gussguss spielt eine entscheidende Rolle bei der Herstellung von Präzisionsmetallteilen. In diesem Artikel, Wir werden uns mit den Feinheiten des Gussschimmeles eintauchen, Warum ist es wichtig, Die verschiedenen Arten von Stahlmaterialien, die für Würfelgussformen verwendet werden, Der Formentwurfsprozess, Herausforderungen für die Schimmelpilzherstellung, und wie man einen zuverlässigen Hersteller von Gussguss -Schimmelpilzen auswählt.
Was ist eine Druckgussform??
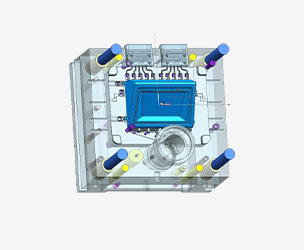
Die Gussform ist eine dauerhafte Form, die verwendet wird, um geschmolzenes Metall in ein bestimmtes Design oder eine bestimmte Form zu formen. Es ist eine entscheidende Komponente in der Druckgussverfahren, wie es das Endergebnis des hergestellten Teils bestimmt. Die Form besteht typischerweise aus hochwertigen Stahlmaterialien, um hohen Temperaturen und Druck zu standhalten.
Die Gussform besteht aus zwei Teilen: die Hohlraum, Welches ist das negative Bild des letzten Teils, Und der Kern, Das prägt die inneren Merkmale des Teils. Die Form ist so konstruiert, dass geschmolzenes Metall unter hohem Druck in den Hohlraum fließen kann, verfestigen, und dann als fertigen Teil ausgeworfen werden.
Warum ist Schimmel für das Gießen wichtig??
Die Form ist wichtig, um die dimensionale Genauigkeit aufrechtzuerhalten und Oberflächenbeschaffenheit des letzten Teils. Es spielt auch eine entscheidende Rolle bei der Gewährleistung der strukturellen Integrität des Teils. Ohne eine richtig gestaltete Form, Der Gussprozess wäre nicht in der Lage, Teile mit der erforderlichen Präzision und Qualität zu produzieren.
Allgemeine Stahlmaterialien für Würfelgussformen
Aluminium,Zink und Magnesium sind drei übliche Legierungen, die verwendet werden Die Gussform -Schimmelpilzdesign.
Aluminiumlegierung Würfelschimmel
Aluminium ist eine beliebte Wahl für die Gussformen aufgrund seiner hervorragenden thermischen Leitfähigkeit und leichten Eigenschaften. Aluminium-Würfelgussformen sind ideal für Produktionsläufe mit hoher Volumen und können wiederholte Zyklen des Erhitzens und Abkühlens standhalten, ohne sich zu verzieren oder zu knacken.
Zinklegierung Würfelschimmel
Zinklegierungen werden aufgrund ihrer überlegenen Strömungseigenschaften und der hohen dimensionalen Stabilität üblicherweise für Würfelgussformen verwendet. Zinkformen sind langlebig und gegen Korrosion beständig, Sie ideal für die Herstellung von Teilen mit komplizierten Designs und dünnen Wänden.
Magnesiumlegierung Würfelschimmel
Magnesiumlegierungen sind leicht und haben ein ausgezeichnetes Verhältnis von Kraft-Gewicht, Sie ideal für das Gussformmaterial für das Gussmaterial zu machen, das hohe Festigkeit und Haltbarkeit erfordern. Magnesiumformen können extreme Temperaturen standhalten und eine hervorragende Oberflächenbeschaffung liefern.
Formentwurfsprozess für das Gießen
Der Formentwurfsprozess für das Gießen ist ein kritischer Aspekt des Gesamtgussprozesses, Da wir sich direkt auf die Qualität auswirken, Effizienz, und Kosteneffizienz der Herstellung von Stadelgussteilen. Hier finden Sie einen Überblick über den typischen Formgestaltungsprozess für das Gießen:
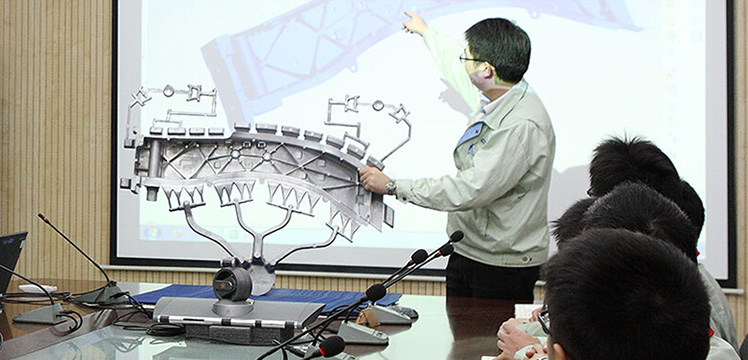
#1: Teilanforderungen definieren
Beginnen Sie damit, einschließlich Abmessungen, Merkmale, Materialeigenschaften, und Produktionsvolumen. Diese Informationen helfen dabei.
#2: Materialauswahl
Wählen Sie das geeignete Material für die Gussform aus dem Gussform auf der Grundlage von Faktoren wie der thermischen Leitfähigkeit, Verschleißfestigkeit, Wärmeausdehnung, und Kosten. Gemeinsame Materialien für Würfelgussformen umfassen Werkzeugstahl, H13, und P20.
#3: Erstellen Sie erste Designkonzepte
Basierend auf den Teilanforderungen und der Materialauswahl, Entwickeln Sie erste Designkonzepte für die Form. Berücksichtigen Sie Faktoren wie den Standort der Abschiedsleitung, Gating -Systemdesign, Kühlkanalplatzierung, Ejektionsmethoden, und Entlüftungsoptionen.
#4: CAD -Modellierung
Verwenden Sie computergestütztes Design (CAD) Software zum Erstellen detaillierter 3D -Modelle der Gussform -Formkomponenten, einschließlich der Hohlraum, Kern, Kühlkanäle, Ejektorsystem, und andere Funktionen. Die CAD -Modellierung ermöglicht eine präzise und genaue Darstellung des Schimmelpilzdesigns.
#5: Das Design analysieren und optimieren
Führen Sie Simulationen und Analysen mit spezieller Software durch, um das Formgestaltung für Faktoren wie die thermische Leistung zu bewerten, Flüssigkeitsfluss, Schrumpfung und Verzerrung, und Schimmelfüllungseigenschaften. Dies hilft bei der Optimierung des Formgestaltung.
#6: Fertigstellen Sie das Schimmeldesign
Basierend auf den Analyseergebnissen und dem Feedback, Verfeinern und schließen Sie das Schimmelpilzdesign, um sicherzustellen, dass alle Anforderungen für Teilqualität erfüllt werden, Produktionseffizienz, und Schimmelpflege. Achten Sie auf Details wie Entwurfswinkel, Filets, Oberflächenbeschaffenheit, und Teil -Auswurffunktionen.
#7: Erstellen Sie detaillierte Zeichnungen
Generieren Sie detaillierte technische Zeichnungen und Spezifikationen für die Gussgussformkomponenten, einschließlich Abmessungen, Toleranzen, Materialien, Oberflächenbehandlungen, und Montageanweisungen. Diese Zeichnungen dienen als Blaupause für die Herstellung der Form.
#8: Fertigung die Form
Übertragen Sie das endgültige Schimmelpilzdesign zur Herstellung in einen Schimmelhersteller -Hersteller. Der Herstellungsprozess kann verschiedene Techniken wie CNC -Bearbeitung beinhalten, EDM (Elektrische Entladungsbearbeitung), Schleifen, Wärmebehandlung, und Polieren, um die Formkomponenten zu erstellen.
#9: Testen und validieren Sie die Form
Sobald die Form hergestellt ist, Führen Sie Tests und Validierung durch, um sicherzustellen. Testen Sie die Form auf Faktoren wie die Genauigkeit der Teildimension, Oberflächenbeschaffenheit, Zykluszeit, und Gesamtleistung.
#10: Feinabstimmung und Verfeinerung
Basierend auf den Testergebnissen und Feedback, Nehmen Sie die erforderlichen Anpassungen oder Verfeinerungen des Formgestalts vor, um die Leistung zu optimieren und Probleme anzugehen. Die iterative Verbesserung ist üblich, um die besten Ergebnisse bei der Produktion der Casting zu erzielen.
#11: Implementieren in Produktion
Sobald das Formgestaltung validiert und genehmigt wurde, Integrieren Sie es in den Produktionsprozess für den regelmäßigen Gebrauch in den Produktionsprozess für den Gasting. Überwachen Sie die Leistung der Form während der Produktionsläufe und führen Sie regelmäßig Wartung durch, um ihre Langlebigkeit und Zuverlässigkeit sicherzustellen.
Durch die Befolgung eines strukturierten Formentwurfsprozesses zum Gießen, Hersteller können hochwertige Formen erstellen, die den spezifischen Anforderungen der zu erzeugenden Teile erfüllen, Produktionseffizienz optimieren, und sicherstellen.
Herausforderungen bei der Herstellung von Schimmelpilzen des Gusss
Die Fertigung des Gussschimmelpacks stellt mehrere Herausforderungen dar, wie z. B. enge Toleranzen zu erreichen, Porosität kontrollieren, Blitz minimieren, und Verfasser verhindern.
Unerbittliches Streben nach engen Toleranzen
Eine der bedeutendsten Hürden beim Gussform -Design ist das unerbittliches Streben nach engen Toleranzen. Sicherstellen, dass die Dimensionen, Winkel, und die Spezifikationen des letzten Teils werden mit äußersten Präzisionsanforderungen erfüllt, die sorgfältige Liebe zum Detail und technisches Fachwissen erfolgen. Jede Abweichung von den gewünschten Toleranzen kann zu fehlerhaften Teilen und Produktionsverzögerungen führen, Hervorhebung der Kritikalität dieser Herausforderung im Herstellungsprozess.
Porosität kontrollieren
Porosität kontrollieren ist eine weitere wichtige Herausforderung, die die Hersteller von Gussschimmelherstellern gegenübersehen. Porosität bezieht sich auf das Vorhandensein kleiner Hohlräume oder Löcher im Material des Teils, Dies kann seine strukturelle Integrität und ästhetische Anziehungskraft beeinträchtigen. Die Verhinderung der Porosität erfordert ein umfassendes Verständnis der Eigenschaften der Metalllegierung, optimale Casting -Parameter, und effektives Schimmelpilzdesign, um das Risiko eines Lufteinschlusses während des Gussprozesses zu minimieren.
Blitz minimieren, oder überschüssiges Material
Blitz minimieren, oder überschüssiges Material, das sich entlang der Abschiedsleitungen der Form bildet, ist eine hartnäckige Herausforderung bei der Herstellung von Gussschimmelpilzen. Flash beeinträchtigt nicht nur die visuelle Anziehungskraft des endgültigen Teils, sondern kann auch seine funktionale Leistung beeinflussen. Implementierung präziser Schimmelpilzdesigns, Aufrechterhaltung einer konsistenten Gussbedingungen, und die Verwendung fortschrittlicher Trimmechniken sind wesentliche Strategien zur Bekämpfung des Blitzes und die Gewährleistung der Produktion hochwertiger Teile.
Verfassen verhindern
Das Verhinderung von Verhandlungen ist eine weitere häufige Herausforderung, bei der die Hersteller von Schimmelpilzen sterben. Verzerrungen bezieht sich auf die Verzerrung oder Verformung des Teils aufgrund von ungleichmäßigen Kühlraten, innere Belastungen, oder materielle Inkonsistenzen. Die Bekämpfung von Verhandlungen erfordert einen ganzheitlichen Ansatz, der die Optimierung des Kühlsystemdesigns umfasst, Kontrolle der Casting -Prozessparameter, und Verwendung von stressabnehmenden Techniken zur Minderung des Verzerrungsrisikos im Endprodukt.
Bian Diecast: Ein vertrauenswürdiger Hersteller von Gussform -Schimmelpilzen
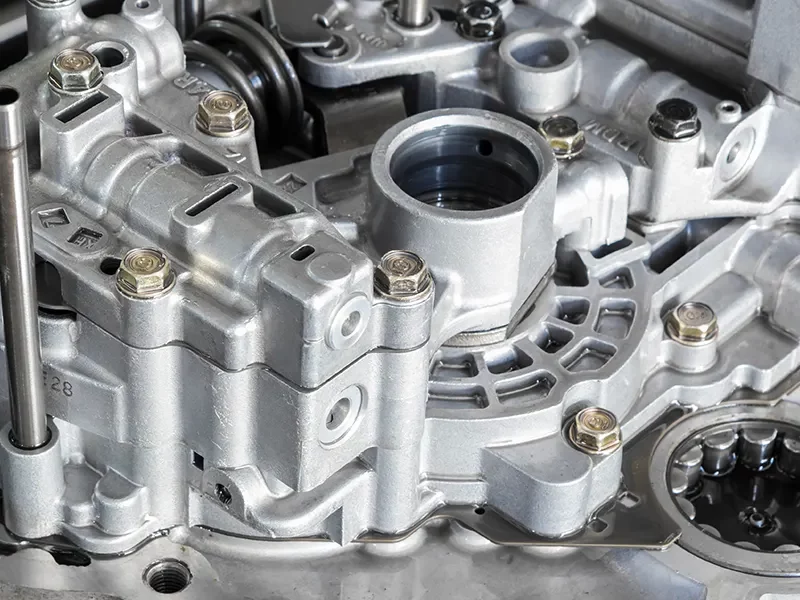
Bei der Auswahl eines Herstellers für die Gussschimmelpilze, Es ist wichtig, ihre Erfahrungen zu berücksichtigen, Sachverstand, Fähigkeiten, und Qualitätskontrollmaßnahmen. Suchen Sie nach einem Hersteller, der nachweislich eine nachgewiesene Erfolgsgeschichte hat, um hochwertige Formen rechtzeitig und innerhalb des Budgets zu liefern.
Mit einer reichen Geschichte der Exzellenz und des Fachwissens in der Herstellung von Gussform -Schimmelpilzen, Bian Diecast hat sich einen hervorragenden Ruf für die Bereitstellung erstklassiger Formen verdient, die den höchsten Branchenstandards entsprechen. Bei Bian Diecast, Präzision ist nicht nur ein Ziel, sondern ein Leitprinzip in jedem Aspekt ihres Schimmelpilzherstellungsprozesses. Unser Team von erfahrenen Handwerkern und Ingenieuren entwirft und fertigt Formen mit engen Toleranzen, Stellen Sie sicher, dass jeder produzierte Teil den genauen Spezifikationen und Anforderungen ihrer Kunden erfüllt. Die Partnerschaft mit Bian Diecast garantiert einen nahtlosen und erfolgreichen Herstellungsprozess, ebnen den Weg für die Herstellung hochwertiger Teile, die die Erwartungen erfüllen und übertreffen.
Abschluss
Die Gussform für die Gussguss ist eine kritische Komponente im Stempelgussprozess, Eine wichtige Rolle bei der Gestaltung von Metallteilen mit Präzision und Genauigkeit spielen. Verständnis der Bedeutung des Schimmelpilzdesigns, Materialauswahl, Qualitätskontrollmaßnahmen, und die Überwindung der Herstellungsherausforderungen ist für die Herstellung hochwertiger Würfel-Cast-Teile von wesentlicher Bedeutung. Durch die Auswahl eines zuverlässigen und erfahrenen Herstellers für die Gussformform, Unternehmen können den Erfolg ihrer Casting -Operationen sicherstellen.