ダイカストは、溶融金属を高圧下で金型キャビティに押し込む製造プロセスです。. このプロセスにより、高レベルの精度と精度で複雑な形状の生産が可能になります. ダイキャスティングは、大量生産に費用対効果の高いソリューションを提供することにより、さまざまな業界で重要な役割を果たします. このブログでは, そのアプリケーションを掘り下げます, 利点, ダイキャスティングで使用される材料.
ダイカストは何に使用されますか?
ダイキャスティングは、一般的に幅広いアプリケーションのために金属部品を生産するために使用されます. Automotive Dieの鋳造部品から電子機器まで, ダイキャスティングは、複雑で複雑に設計されたダイキャスティング製品の需要を満たす汎用性のある方法です.
一般的なダイキャスティングアプリケーション
ダイキャスティングは、多様なコンポーネントを生産するためにさまざまな業界で広く使用されています. 最も一般的なアプリケーションには含まれます:
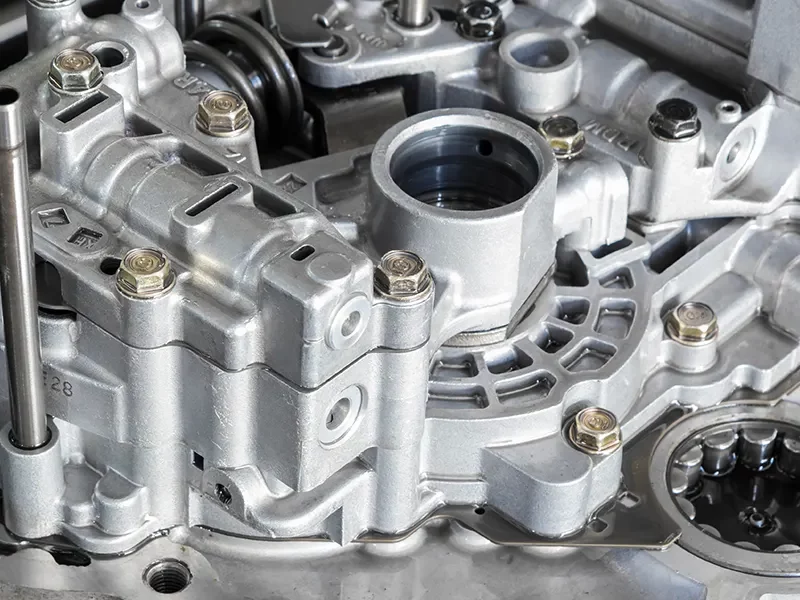
自動車産業
の 自動車分野 エンジン部品などの重要なコンポーネントの製造のためのダイキャスティングに大きく依存しています, トランスミッションコンポーネント, シャーシ要素, もっと. ダイキャスト部品の高強度比と寸法精度により、安全性を確保する上でそれらを不可欠にします, パフォーマンス, 道路上の車両の信頼性. 高圧エンジンコンポーネントから複雑なシャーシ要素まで, ダイキャスティングは、自動車の製造環境に革命をもたらし続けています.
航空宇宙産業
航空宇宙分野では, 正確な場所, 信頼性, 軽量のプロパティが最重要です, ダイキャスティングは、重要な製造プロセスとして現れます. 航空宇宙産業は、鋳造物を活用して、厳しいパフォーマンス要件に準拠した軽量コンポーネントを生産する. 航空機のエンジン部品から構造コンポーネントまで, ダイキャストコンポーネントは、航空宇宙システムの効率と安全性を高める上で重要な役割を果たします, 航空旅行技術の進歩に貢献します.
エレクトロニクス産業
の エレクトロニクス産業 住宅の製造のためにダイキャスティングを広範囲に利用しています, ヒートシンク, 電子デバイス用のさまざまなコンポーネント. ダイキャストパーツが提供する優れた熱伝導率と寸法安定性により、最適なパフォーマンスを維持するための理想的な選択肢になります, 熱散逸, 電子アプリケーションの信頼性. 複雑な電子エンクロージャーから熱管理ソリューションまで, ダイキャスティングは、私たちが日常生活で使用する電子デバイスの機能と寿命を確保する上で重要な役割を果たします.
ダイキャスティングの汎用性は、これらの業界をはるかに超えています, 消費財から産業機器に至るまでのアプリケーションがあります. として ダイカストメーカーダイキャスティングプロセスを革新し、改良し続けます, 既存の産業における新しいアプリケーションと進歩の可能性は無限のままです.
ダイカスト工程の種類
以下は、ダイキャストプロセスの3つの一般的なタイプです:
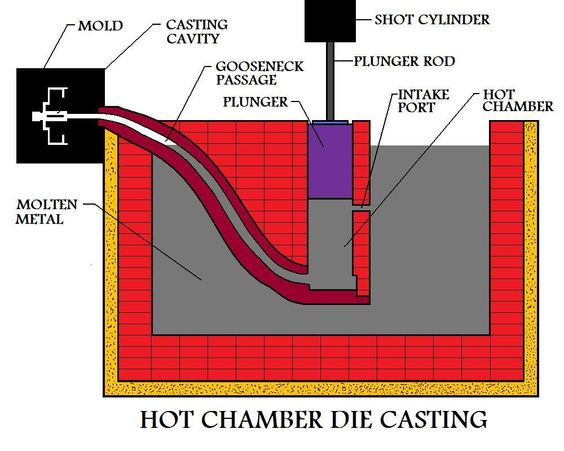
ホットチャンバーダイキャスティング
ホットチャンバー内ダイカスト, 注入システムは溶融金属のプールに浸されています. このプロセスは、融点が低い金属に最適です, 亜鉛やマグネシウムなど. 溶融金属は圧力下でカビの空洞に押し込まれます, その結果、サイクル時間が速く生産性が高くなります.
コールドチャンバーダイキャスティング
コールドチャンバーダイキャスティングには、注入システムに移す前に、金属を別の炉で溶かすことが含まれます. このプロセスは、融点が高い金属に適しています, アルミニウムなど. コールドチャンバーダイキャスティングにより、より強度と耐久性の高いより複雑な部品の生産が可能になります.
マルチスライドダイキャスティング
マルチスライドダイキャスティングは複数のスライドを使用して複雑な形状とデザインを作成します. このプロセスは、複雑なジオメトリまたは正確な詳細を必要とする機能を備えた部品によく使用されます. マルチスライドダイキャスティングは、複雑で詳細な部品の作成を許可することにより、ダイキャスティングの生産能力を強化します.
ダイキャスティングの利点は何ですか?
ダイキャスティングは、多くの業界にとって優先製造方法になるいくつかの利点を提供します. 重要な利点には含まれます:
高精度と複雑さ
ダイキャスティングは、非常に厳しい許容範囲を持つ複雑な形状とコンポーネントの生産に優れています. このプロセスにより、比類のない精度のある複雑な幾何学と複雑なデザインを作成できます. このレベルの精度により、各パーツが必要な仕様に準拠することが保証されます, 生産ラン全体で一貫した品質を維持します.
コスト効率の高い生産
ダイキャスティングの主な利点の1つは、大量生産の費用対効果にあります. このプロセスは非常に効率的です, ユニットあたりの低コストで多数の部品の迅速な製造を可能にする. ダイキャスティングの高速生産能力は、人件費の最小化と材料の廃棄物の削減に役立ちます, 大量生産シナリオの費用対効果の高いソリューションにします.
クイックサイクル時間
ダイキャスティングは、急速なサイクル時間を誇っています, つまり、部品は迅速なペースで生産できることを意味します. ダイキャスティングが提供するクイックターンアラウンド時間は、生産スケジュールの要求に応えるのに役立ちます, 厳しい締め切りに対応します, 緊急の命令を満たします. サイクル時間の観点からダイキャスティングの効率により、部品のタイムリーな配信が保証されます, 製造業の運用をスムーズに稼働させます.
優れた機械的特性
ダイキャスト部品は、優れた機械的特性を示します, 高い引張強度を含む, 耐久性, 寸法安定性. ダイキャストコンポーネントの冶金特性は、その優れた性能特性に貢献しています, 堅牢で信頼できる部品を必要とするアプリケーションに最適にする. 重要な自動車コンポーネントから複雑な電子機器まで, ダイキャスト部品の機械的特性は、それらの機能と寿命を強化します.
汎用性と設計の柔軟性
ダイキャスティングは、高度な汎用性と設計の柔軟性を提供します, 複雑な形の作成を可能にします, 薄い壁, そして複雑な詳細. メーカーは、ダイキャスティングを通じてユニークなデザインと革新的なソリューションを実現できます, 特定の要件と審美的な考慮事項を満たすカスタマイズされた部品の生産を可能にする.
ダイカストに使用される材料
ダイキャスティングは、さまざまな金属で実行できます, しかし、使用される最も一般的な材料には含まれます:

アルミダイカスト
アルミニウムは軽量でありながら耐久性があります, 強さと柔軟性を必要とするアプリケーションに理想的な選択肢となる. アルミダイカスト 自動車および航空宇宙産業で一般的に使用されています。高強度比率を必要とするコンポーネントを生産するために.
亜鉛ダイカスト
亜鉛は、優れた腐食抵抗と寸法の安定性を提供する汎用性のある材料です. 亜鉛ダイキャスティングは、多くの場合、家電に使用されます, 家電製品, コストが低く、キャスティングの容易さが原因で医療機器.
マグネシウムダイカスト
マグネシウムは、利用可能な最も軽い構造金属です, 高強度と耐衝撃性のある軽量コンポーネントを必要とするアプリケーションに理想的なものにします. マグネシウムダイキャスティングは、優れた熱伝導率と強度と重量の比率を必要とする部品を生産するために、自動車産業で一般的に使用されています.
結論
ダイキャスティングは、高品質の金属部品を生産するための多くの利点を提供する多目的で効率的な製造プロセスです. 自動車から航空宇宙産業まで, ダイキャスティングは、複雑で複雑に設計されたコンポーネントの需要を満たす上で重要な役割を果たします. テクノロジーと材料の進歩があります, ダイキャスティングの将来の可能性は無限です, 革新的なソリューションと製造能力の強化への道を開く.
Bian Diecastと提携しています: 信頼できるアルミニウムダイキャスティングメーカー
Bian Diecastは、大手アルミニウムダイキャスティングメーカーとしての強い評判を確立しています, さまざまな産業の厳しい要件を満たす高品質のコンポーネントを一貫して提供する. 精度に焦点を当てています, 効率, 顧客満足度, Bian Diecastは、一流のアルミニウムダイキャスティングソリューションを求めている企業にとって好ましいパートナーになりました. Bian Diecastは、あなたがあなたの生産目標を達成し、あなたの業界で成功を促進するのに役立つ完璧なパートナーです.