Aluminum die casting is a revolutionary process that plays a pivotal role in numerous industries. From automotive to electronics, the versatility and efficiency of aluminum die casting make it a preferred manufacturing method. But what makes aluminum die casting products so exceptional? Let’s explore the fascinating world of die casting and understand its significance.
What is Aluminum Die Casting?
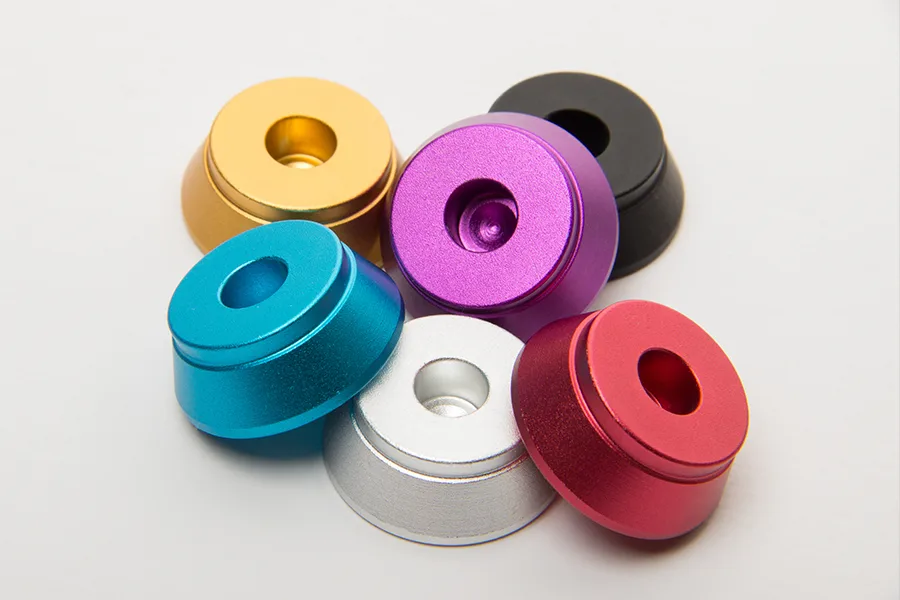
Aluminum die casting is a highly efficient manufacturing process where molten aluminum is injected into a mold cavity under high pressure. This technique produces complex and detailed metal casting products with remarkable precision and consistency. Think of it as crafting intricate sculptures, but with metal. This method is renowned for its ability to produce high-quality, durable die casting products rapidly and economically.
Process of Aluminum Die Casting
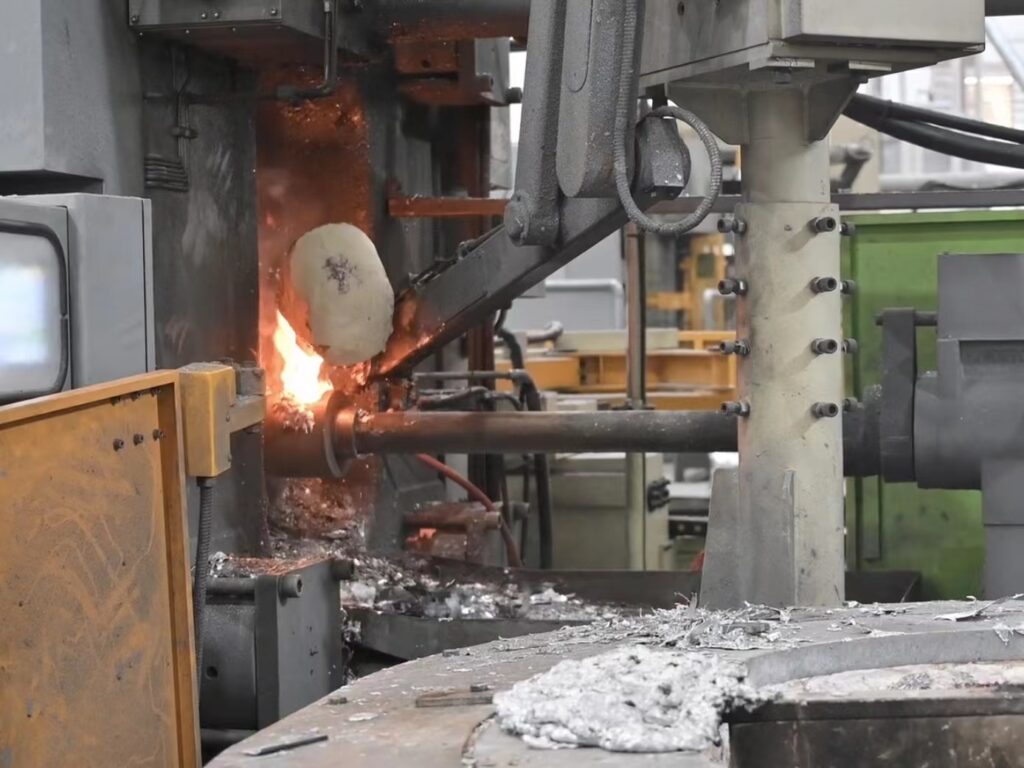
Mold Creation
The mold design process begins with the creation of a mold, also known as a die. This mold is meticulously designed to match the exact specifications of the part to be produced. Imagine crafting a detailed blueprint that will shape the molten aluminum into a perfect replica.
Injection Process
Once the mold is ready, the injection process starts. Molten aluminum is forced into the mold cavity under high pressure. This step is crucial as it ensures that the aluminum fills every tiny detail of the mold, capturing intricate designs and maintaining structural integrity.
Cooling and Ejection
After the aluminum has been injected, it needs to cool and solidify. The cooling phase allows the metal to harden and take on the desired shape. Once solidified, the newly formed part is ejected from the mold, ready for finishing touches. This phase is essential to ensure the part’s durability and precision.
Properties of Aluminum
Aluminum is not just another metal; it’s a material that boasts several unique properties, making it ideal for die casting products.
Lightweight
Aluminum is incredibly lightweight, which is a significant advantage for applications where reducing weight is crucial. For instance, in the automotive industry, lighter parts contribute to better fuel efficiency and improved vehicle performance.
Corrosion Resistance
One of the standout features of aluminum is its natural resistance to corrosion. This property ensures that aluminum die casting products can withstand harsh environments and remain in excellent condition over time, reducing the need for frequent replacements.
Thermal Conductivity
Aluminum’s excellent thermal conductivity makes it perfect for applications that require efficient heat dissipation. Whether in automotive engine components or electronic devices, aluminum helps manage heat effectively, enhancing performance and longevity.
Applications of Aluminum Die Casting Products
Aluminum die casting products find applications in a wide array of industries, thanks to their versatility and reliability.
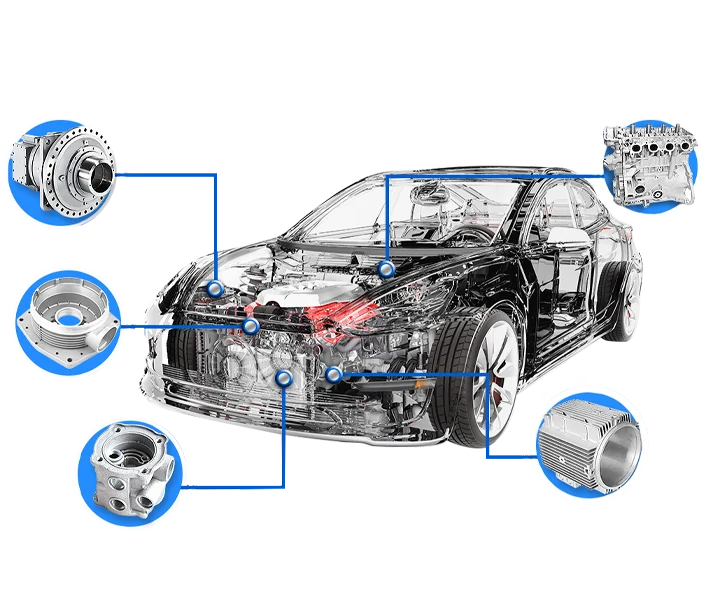
Automotive Parts
In the automotive sector, aluminum pressure die casting products are indispensable. They are used to create critical aluminum die casting auto parts such as engine blocks, cylinder heads, transmission cases, and structural parts. These parts benefit from aluminum’s lightweight and strong properties, contributing to better fuel economy and performance.
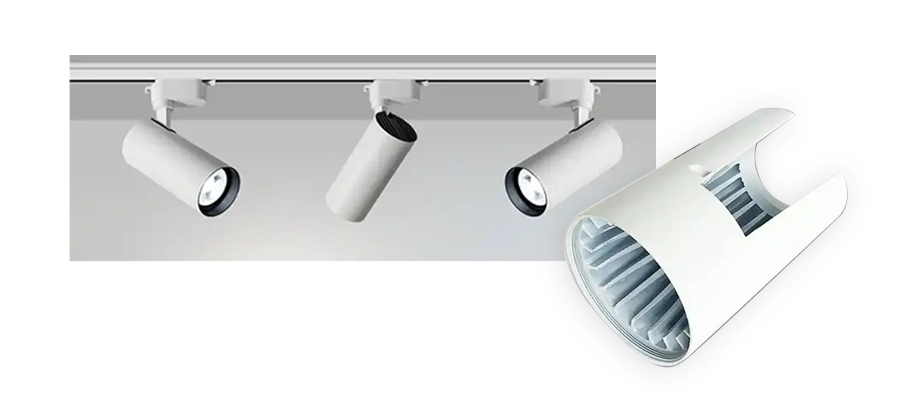
Lighting Parts
The lighting industry also relies heavily on aluminum die casting. Components like frames, housings, and heat sinks for LED lights are made using aluminum die casting. The material’s excellent thermal conductivity ensures that the lights remain cool and efficient, extending their lifespan.
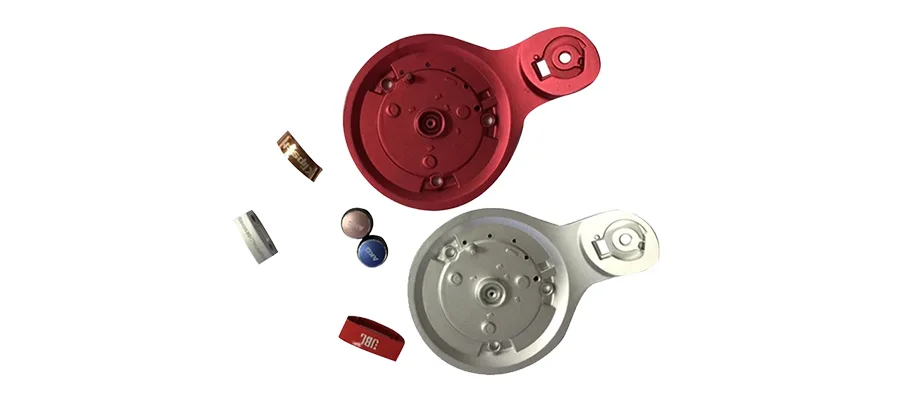
Electronic Parts
Electronic devices require precise and durable components. Aluminum die casting is used to produce parts such as enclosures, connectors, and heat sinks. These metal casting products ensure that electronic devices function reliably while effectively managing heat.
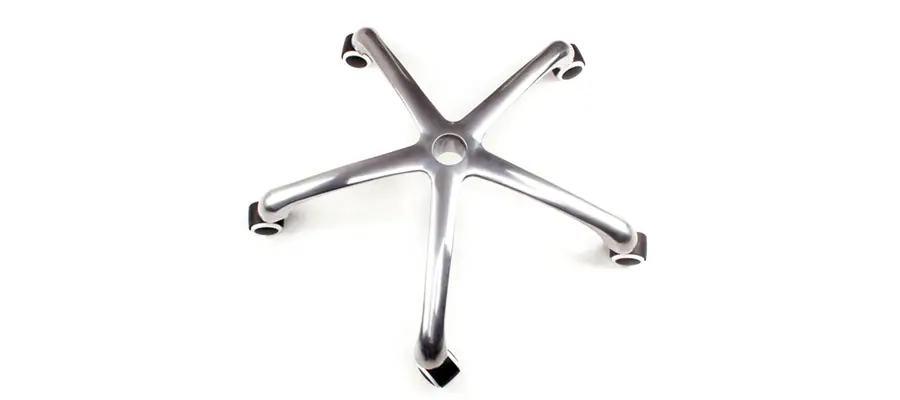
Construction Parts
In construction, aluminum die casting products are used for creating robust and lightweight structural components. From window frames to building facades, aluminum parts offer durability and ease of installation, making construction projects more efficient.
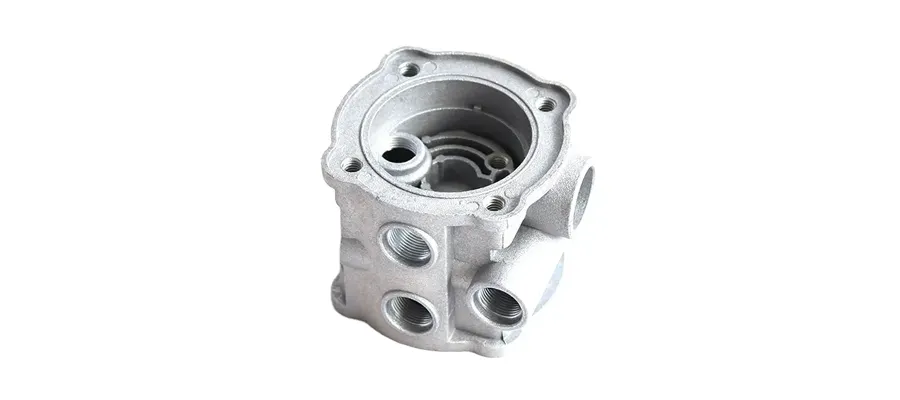
Furniture Parts
Even the furniture industry benefits from aluminum die casting. Parts such as chair bases, table frames, and decorative elements are crafted using this process. The result is stylish, modern furniture that combines aesthetic appeal with structural integrity.
Benefits of Aluminum Die Casting Parts
Aluminum die casting parts offer a remarkable blend of strength and lightness, making them ideal for modern manufacturing. Some benefits are as follow:
Lightweight and Strong
Aluminum die casting parts provide an ideal combination of lightness and strength, crucial for enhancing vehicle performance and efficiency. This balance reduces fuel consumption while maintaining durability, making them essential for modern automotive design. By lowering the overall weight of vehicles, aluminum parts contribute to better handling and acceleration.
Corrosion Resistance
These parts naturally resist corrosion, ensuring longevity and reducing the need for frequent replacements. This makes them perfect for applications in harsh environments, such as automotive and outdoor equipment. The inherent corrosion resistance of aluminum helps maintain the appearance and structural integrity of components over time.
Thermal Conductivity
Aluminum’s excellent thermal conductivity allows parts to effectively manage heat, improving the performance and lifespan of components like engine blocks and electronic housings. This property is crucial in high-temperature environments, where efficient heat dissipation can prevent overheating and enhance overall functionality.
Design Versatility
The flexibility of die casting allows for intricate and complex designs, enabling innovative solutions tailored to specific requirements across industries. Manufacturers can produce detailed and precise components, allowing for creative and efficient designs that meet various application needs.
Cost Efficiency
Die casting is cost-effective, offering high-volume production with minimal waste, which reduces manufacturing expenses without sacrificing quality. The process streamlines manufacturing, enabling rapid production of parts at lower costs, benefiting industries that require large quantities of components.
Conclusion
Aluminum die casting is a cornerstone of modern manufacturing, offering unparalleled versatility, efficiency, and quality. Its applications span various industries, driving innovation and performance. As we continue to advance technologically, aluminum die casting products will undoubtedly play a crucial role in shaping the future of manufacturing.
FAQs
- What products are made from die casting? Die casting is used to create a wide range of products, including automotive parts, electronic enclosures, lighting fixtures, construction fittings, and furniture components.
- Why is aluminum preferred for die casting? Aluminum is preferred for die casting due to its lightweight, corrosion resistance, excellent thermal conductivity, and ability to produce detailed and complex shapes.
- How does die casting improve product quality? Die casting improves product quality by ensuring high precision, consistency, and structural integrity in the parts produced. This results in reliable and durable products.
- Is die casting cost-effective? Yes, die casting is cost-effective because it allows for high-volume production with minimal material waste, reducing overall manufacturing costs.
- Can die casting be used for custom designs? Absolutely! Die casting offers significant design flexibility, making it possible to create custom and intricate designs that meet specific industry needs.