Aluminum die casting is a highly effective manufacturing process. It allows us to shape metal into complex forms with pinpoint precision. But here’s the kicker: despite its advantages, defects in metal casting can sneak in, causing a ton of headaches. If you’ve ever dealt with aluminum die casting defects, you’ll know how frustrating and costly they can be. But don’t sweat it! We’re about to dive into the most common aluminum casting defects, what causes them, and—most importantly—how to avoid them.
Common Aluminum Die Casting Defects
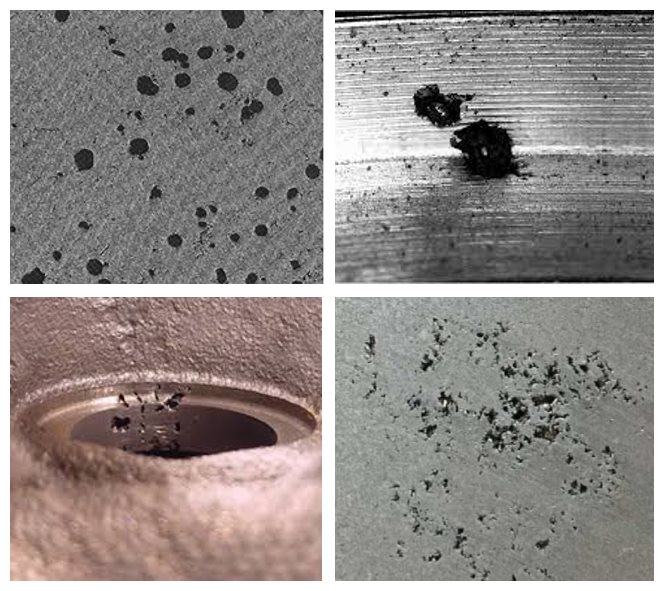
1. Porosity
Porosity is the invisible troublemaker of the die casting process. It’s like the little air pockets that form when a sponge rises. You can’t always see it on the surface, but it’s there, weakening the structure.
Causes of Porosity
- Gas entrapment is the main culprit. When air or other gases get trapped in the molten metal during casting, they form voids.
- Shrinkage during cooling is another cause. As the metal solidifies, it contracts, leaving tiny voids if the material isn’t evenly distributed.
How to Avoid Porosity
The trick to avoiding porosity is in the details. Optimize the casting design to allow for smooth metal flow and make sure the gas levels are controlled during the process. Using the right alloys can also reduce porosity risks.
2. Cold Shuts
Ah, the dreaded cold shut in casting! This happens when two streams of molten metal meet but fail to fuse properly, leaving a visible seam. Think of it as two puzzle pieces that just don’t click.
Causes of Cold Shuts
- A low metal temperature often causes this issue. If the molten metal isn’t hot enough, it won’t flow smoothly and blend properly.
- Incomplete metal flow also leads to cold shuts, usually when the pressure isn’t right.
How to Prevent Cold Shuts?
Simple: increase the casting temperature! Make sure the mold is fully filled by adjusting the flow rate, too. These tweaks go a long way in preventing cold shuts.
3. Flashing
Flashing sounds harmless, but it’s one of the most frustrating aluminum die casting defects. It occurs when excess metal escapes the mold, creating thin, sharp fins that need to be trimmed off later.
Causes of Flashing
- Excessive metal leakage happens when there’s too much pressure in the die, forcing metal out of unwanted places.
- Mold misalignment can also lead to flashing since it creates gaps for the metal to sneak through.
How to Avoid Flashing
Regular mold maintenance and ensuring the die is properly aligned and clamped down are essential steps to avoid flashing. Keep your tools in shape!
4. Warping
Ever seen a casting come out twisted or bent? That’s warping. It’s like what happens when you cook bacon—uneven heat causes it to curl up. Warping is basically metal’s version of bacon.
Causes of Warping
- Uneven cooling rates are the usual suspects here. If one part of the casting cools faster than the rest, it warps.
- Thin sections of the casting can warp more easily because they cool faster than thicker sections.
Preventive Measures for Warping
You need uniform cooling to prevent warping. Adjust the mold design to make sure all sections cool at the same rate. Thicker walls can help, too!
5. Surface Defects (Blisters, Marks)
Surface defects are like acne on the casting—ugly and hard to hide. Blisters and marks form on the surface, making the casting look sloppy.
Causes of Surface Defects
- Poor mold surface quality often leads to these issues. A rough or damaged mold will transfer those imperfections to the casting.
- Excessive pressure can also cause blow holes in aluminum die casting, where trapped gas escapes and creates bubbles.
How to Avoid Surface Defects
Keep the mold surface in top shape! Regular surface polishing and maintenance of the mold can minimize surface defects. Also, controlling casting pressure helps prevent gas from escaping, reducing the risk of blow holes.
Less Common Aluminum Die Casting Defects
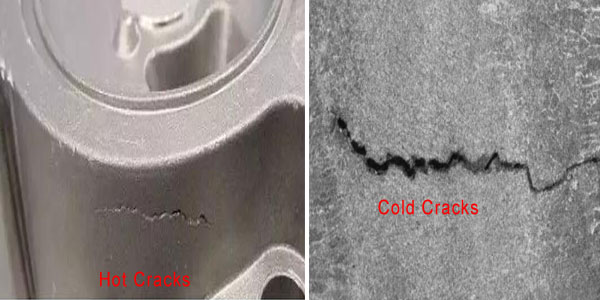
6. Hot Cracking
Hot cracking is exactly what it sounds like: cracks that form when the casting is still hot. This happens when internal stress causes the metal to break before it’s fully solidified.
Causes of Hot Cracking
- Internal stress is the main cause of hot cracking. When the metal cools unevenly or too quickly, it can crack.
- Inadequate cooling times can exacerbate the problem.
How to Prevent Hot Cracking
Give the casting time to cool evenly. Adjusting the cooling times and using alloys with better thermal properties can help reduce internal stress and prevent cracks.
7. Cold Cracking
Cold cracking, on the other hand, occurs after the casting has cooled. This type of cracking happens due to residual stress or when the mold temperature is too high.
Causes of Cold Cracking
- Residual stress after the casting has cooled can lead to cracking.
- Excessive mold temperatures during the process can cause issues once the casting cools.
How to Avoid Cold Cracking
Monitor mold temperatures closely and consider using stress relief techniques after casting, such as heat treatment.
8. Incomplete Filling
Sometimes the mold doesn’t get fully filled with metal, resulting in an incomplete casting. This defect is like trying to fill a glass of water but only getting halfway there.
Causes of Incomplete Filling
- Insufficient metal flow is a common cause. If the molten metal doesn’t flow fast enough, the mold won’t fill completely.
- Low pressure during the casting process can also result in incomplete filling.
How to Prevent Incomplete Filling
Make sure the casting speed is optimized and that the gate designs allow for smooth and rapid metal flow. This ensures the mold gets completely filled.
How to Detect and Test for Defects?
Identifying defects in aluminum die casting is crucial for ensuring quality and performance. A defect left undetected can lead to weakened parts, poor aesthetics, and even failure in application. Several methods can detect and test for defects, each suited to different types of flaws.
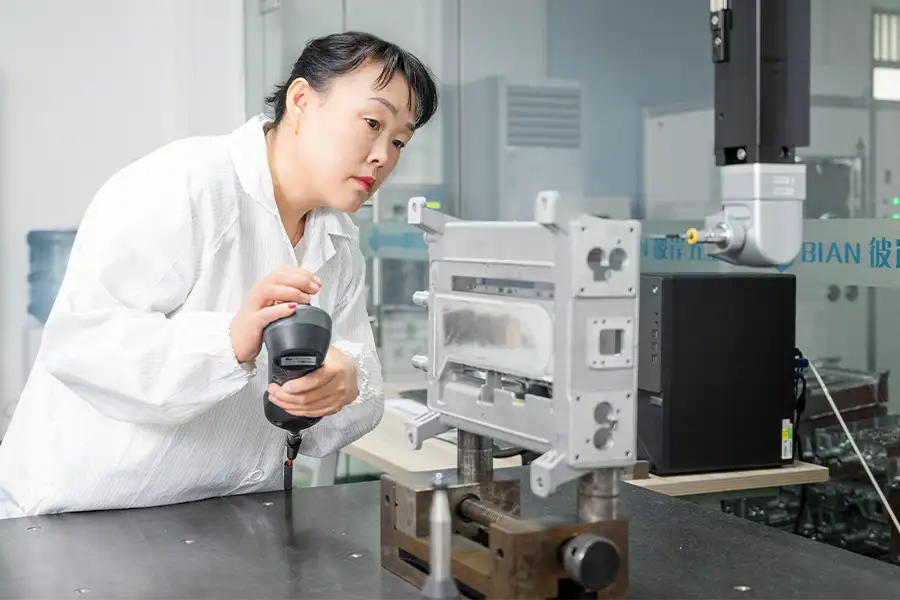
Visual Inspection
The most straightforward method of identifying defects is visual inspection. It is used to spot surface-level problems such as cold shuts, porosity, or surface defects like blisters and marks. Inspecting for irregularities in texture, color, or shape is essential for detecting defects early in the process.
However, visual inspection is limited to surface-level issues. While it’s useful for spotting obvious defects, it cannot reveal internal issues. It’s often the first step before proceeding with more detailed testing.
X-ray Testing
For detecting internal defects, X-ray testing is highly effective. This method allows you to examine the internal structure of the casting without cutting into it. X-rays penetrate the material and reveal any voids, trapped gas, or inconsistencies in density, making it ideal for identifying internal porosity or blow holes in aluminum die casting.
X-ray testing is especially useful for high-value or critical parts where internal integrity is essential. However, it is more expensive and time-consuming compared to visual inspection, making it best suited for complex or high-stakes castings.
Pressure Testing
Pressure testing assesses the casting’s ability to withstand internal or external pressure, ensuring it can perform under real-world conditions. It involves subjecting the casting to fluid or gas pressure to detect leaks, weak spots, or potential failures in the structure.
This method is particularly effective for parts that will be exposed to high levels of stress, such as engine components or hydraulic systems. Pressure testing reveals defects like porosity, cracks, or incomplete filling and provides insight into the overall durability and reliability of the casting.
Best Practices for Reducing Defects in Aluminum Die Casting
Optimizing Mold Design
A well-designed mold is key to minimizing defects. The mold should facilitate even metal flow and promote uniform cooling to reduce the risk of issues like porosity and warping. Avoid using sharp corners and thin walls in the design, as these areas can lead to stress concentrations and uneven cooling, increasing the chances of defects.
Temperature Control in Die Casting
Maintaining precise temperature control during the die casting process is crucial. Both the mold and molten metal must be kept within an optimal temperature range. If either gets too hot or too cold, defects such as cold shuts, porosity, or warping are likely to occur. Consistency in temperature throughout the process ensures a smooth casting with minimal flaws.
Regular Mold Maintenance
Regular maintenance of molds is essential to prevent wear and tear from affecting casting quality. Over time, molds can develop surface damage or lose their precision, which can result in defects like flashing or surface imperfections. Frequent inspections and necessary repairs keep molds in top condition and ensure better casting outcomes.
Selecting the Right Alloy
Choosing the appropriate aluminum alloy can significantly impact casting quality. Some alloys are more prone to defects, while others are more stable and reliable. Selecting an alloy with good fluidity, low shrinkage, and a proven track record for low defect rates helps reduce common casting issues and ensures consistent results.
Conclusion
At the end of the day, aluminum die casting defects are just part of the process. But with the right techniques, you can minimize them and produce top-quality castings. By understanding the common casting defects—whether it’s porosity, cold shut in casting, or blow holes in aluminum die casting—you’re better equipped to tackle them head-on. Now you can keep your types of defects in check and get those perfect castings!
Frequently Asked Questions
- What is porosity in die casting, and how can it be minimized? Porosity refers to small air pockets or voids in the casting caused by gas entrapment or shrinkage. It can be minimized by optimizing the design and controlling gas levels.
- How does mold design affect casting defects? Poor mold design can lead to uneven metal flow and cooling, resulting in defects like warping and incomplete filling. A good design ensures a smooth process.
- Can temperature fluctuations cause defects in aluminum die casting? Yes! Both mold and metal temperatures need to be carefully regulated. Too much variation can lead to defects like cold shuts, porosity, or warping.
- What are the most effective methods to detect internal casting defects? X-ray testing is the best way to detect internal defects like porosity and blow holes without damaging the casting.
- Which aluminum alloys are least likely to develop defects during die casting? Alloys specifically designed for die casting, like A380 or ADC12, are known for producing fewer defects due to their excellent fluidity and low shrinkage rates. “`